Unlock Savings: The Ultimate Guide to Mask Supplier (2025)
Introduction: Navigating the Global Market for mask supplier
In today’s global market, sourcing high-quality mask suppliers can be a daunting task for international B2B buyers, particularly those operating in regions like Africa, South America, the Middle East, and Europe. As the demand for effective personal protective equipment (PPE) continues to rise, businesses face challenges not only in ensuring product quality but also in navigating the complexities of international procurement. This guide aims to streamline the process by providing a comprehensive overview of mask types, applications, supplier vetting criteria, and cost considerations.
Throughout this guide, we delve into the various categories of masks available, including disposable, KN95, and surgical masks, and their specific applications across different industries. We will also explore the critical factors to consider when selecting suppliers, such as certifications, manufacturing standards, and delivery capabilities. Additionally, understanding the cost structures associated with bulk purchases will empower buyers to make informed financial decisions that align with their organizational budgets.
By leveraging the insights provided in this guide, international B2B buyers can confidently navigate the global market for mask suppliers. Whether you are a healthcare provider in Brazil seeking reliable PPE or a business in Germany aiming to secure a consistent supply chain, this resource is designed to enhance your purchasing strategy and ensure the safety of your workforce.
Understanding mask supplier Types and Variations
Type Name | Key Distinguishing Features | Primary B2B Applications | Brief Pros & Cons for Buyers |
---|---|---|---|
Disposable Face Masks | Typically 3-ply or 4-ply, single-use, cost-effective | Healthcare, hospitality, retail | Pros: Affordable, easy to use; Cons: Not reusable, lower filtration efficiency compared to respirators. |
N95 Respirators | Tight-fitting, filters at least 95% of airborne particles | Healthcare, industrial environments | Pros: High filtration efficiency; Cons: More expensive, requires proper fit testing. |
KN95 Masks | Similar to N95, meets Chinese standards, adjustable | Healthcare, manufacturing, logistics | Pros: Good balance of cost and filtration; Cons: Quality can vary widely among suppliers. |
Surgical Masks | Fluid-resistant, designed for medical procedures | Hospitals, clinics, dental practices | Pros: Protects against fluid exposure; Cons: Limited protection against airborne pathogens. |
Custom Branded Masks | Personalized with company logos or designs | Corporate events, promotional use | Pros: Enhances brand visibility; Cons: Higher cost, longer lead times. |
What Are Disposable Face Masks and Their B2B Applications?
Disposable face masks, typically made of 3-ply or 4-ply materials, are designed for single use and are a cost-effective solution for various industries. They are widely used in healthcare settings, hospitality, and retail environments where there is a need for basic respiratory protection. Buyers should consider their low cost and ease of use, but be aware that they do not provide the same level of filtration as respirators, making them less effective against smaller airborne particles.
How Do N95 Respirators Differ from Other Masks?
N95 respirators are designed to achieve a very close facial fit and filter at least 95% of airborne particles, making them suitable for high-risk environments such as healthcare and industrial settings. When purchasing N95 masks, businesses must consider the need for fit testing, as improper fit can significantly reduce their effectiveness. While they offer superior protection, they also come at a higher price point compared to disposable masks.
What Are KN95 Masks and Their Suitability?
KN95 masks are similar to N95 respirators but are manufactured to meet Chinese standards. They are adjustable and provide a good level of filtration, making them suitable for healthcare, manufacturing, and logistics sectors. When sourcing KN95 masks, buyers should ensure that they are purchasing from reputable suppliers, as the quality can vary widely. They strike a balance between cost and protection, making them a popular choice for many businesses.
What Are Surgical Masks and Their Key Uses?
Surgical masks are fluid-resistant and designed specifically for medical procedures to protect against the transfer of pathogens. They are primarily used in hospitals, clinics, and dental practices. While surgical masks provide some protection against splashes and droplets, they do not offer the same level of respiratory protection as N95 or KN95 masks. B2B buyers should consider the specific needs of their medical environments when choosing surgical masks.
Why Consider Custom Branded Masks for Your Business?
Custom branded masks allow businesses to enhance their brand visibility while providing essential protection. These masks can be personalized with company logos or designs, making them suitable for corporate events and promotional use. However, buyers should keep in mind that custom masks often come at a higher cost and may require longer lead times for production. This option is ideal for companies looking to combine safety with marketing efforts.
Related Video: How Surgical N95 Face Mask are made using Ultrasonic Welding By Sonitek
Key Industrial Applications of mask supplier
Industry/Sector | Specific Application of mask supplier | Value/Benefit for the Business | Key Sourcing Considerations for this Application |
---|---|---|---|
Healthcare | Surgical and procedural masks | Protects healthcare workers from infections | Compliance with medical standards (e.g., ASTM, FDA) |
Manufacturing | Masks for industrial settings | Ensures worker safety and compliance with regulations | Durability and filtration efficiency for specific applications |
Hospitality | Masks for staff and guests | Enhances safety and builds customer confidence | Comfort and breathability for extended wear |
Education | Masks for students and staff | Reduces transmission of airborne diseases | Size variations for children and adults |
Retail | Disposable masks for customers | Provides a safe shopping environment | Bulk purchasing options and branding opportunities |
How Are Masks Used in Healthcare Settings?
In healthcare, surgical and procedural masks are essential for protecting medical staff and patients from infections. These masks are designed to filter out bacteria and viruses, ensuring a sterile environment during procedures. For international B2B buyers, especially from regions like Africa and South America, sourcing masks that meet rigorous medical standards (such as ASTM and FDA approvals) is crucial. This ensures that the masks provide adequate protection and comply with local health regulations.
What Are the Benefits of Masks in Manufacturing?
In manufacturing environments, masks are utilized to safeguard workers against harmful dust, chemicals, and other airborne particles. The right mask can help businesses adhere to occupational safety regulations, minimizing the risk of workplace injuries and illnesses. Buyers from the Middle East and Europe should prioritize sourcing masks that offer high durability and filtration efficiency, tailored to the specific hazards present in their manufacturing processes.
How Do Masks Enhance Safety in Hospitality?
In the hospitality industry, masks are used by staff and guests to promote a safe environment, especially during health crises. This practice not only protects employees but also instills confidence in customers, enhancing the business’s reputation. When sourcing masks, buyers should consider comfort and breathability, as staff may need to wear them for extended periods. This is particularly relevant for businesses operating in high-tourism areas in Africa and South America.
Why Are Masks Important in Educational Institutions?
Educational institutions utilize masks to reduce the spread of airborne diseases among students and staff. This is especially important during flu seasons or pandemics, where close contact is common. Buyers should look for masks that come in various sizes to accommodate both children and adults, ensuring a proper fit for effective protection. Educational institutions in Europe and the Middle East can benefit from sourcing masks that are both effective and comfortable for prolonged use.
How Can Retailers Utilize Disposable Masks?
In retail settings, disposable masks serve as a safety measure for customers, creating a secure shopping atmosphere. Retailers can also use branded masks as part of their marketing strategy, enhancing brand visibility while promoting health safety. For international buyers, especially in regions like South America, sourcing masks in bulk can provide significant cost savings and support the implementation of health protocols in stores.
3 Common User Pain Points for ‘mask supplier’ & Their Solutions
Scenario 1: Inconsistent Quality of Masks from Suppliers
The Problem: B2B buyers often face the challenge of inconsistent quality in disposable masks from various suppliers. This inconsistency can lead to significant issues, particularly for businesses in sectors like healthcare or manufacturing, where safety and compliance are paramount. For instance, a hospital purchasing masks for its staff may receive batches that do not meet required safety standards, risking the health of employees and patients. Additionally, inconsistent quality can result in increased returns and lost trust in the supplier, leading to disruptions in operations.
The Solution: To combat this issue, buyers should prioritize sourcing masks from suppliers that provide comprehensive documentation, including certifications and testing results. It is essential to request samples before making bulk purchases to assess the quality firsthand. Furthermore, establishing a long-term relationship with a trusted supplier can lead to better consistency in product quality. Buyers should also consider implementing a quality assurance process upon receipt of masks, including random sampling and testing to ensure compliance with safety standards. By doing so, businesses can mitigate risks and ensure a reliable supply of high-quality masks.
Scenario 2: Complicated Sourcing Process for Bulk Orders
The Problem: For international buyers, particularly from regions like Africa or South America, navigating the sourcing process for bulk mask orders can be daunting. Factors such as language barriers, different regulatory standards, and shipping complexities can create significant hurdles. Additionally, the lack of clear communication from suppliers can lead to misunderstandings about product specifications, delivery timelines, and pricing, resulting in delays and unexpected costs.
The Solution: To simplify the sourcing process, buyers should engage with suppliers who have experience in international trade and can provide clear, multilingual support. It’s advisable to utilize platforms that facilitate direct communication and offer user-friendly interfaces for placing orders. Buyers can also benefit from establishing detailed contracts that outline all aspects of the transaction, including payment terms, product specifications, and delivery schedules. Leveraging freight forwarders or logistics companies with expertise in the region can help streamline the shipping process, ensuring timely delivery and minimizing complications.
Scenario 3: Lack of Transparency in Pricing and Costs
The Problem: Another common pain point for B2B buyers is the lack of transparency in pricing and additional costs associated with purchasing masks. Hidden fees such as shipping costs, customs duties, or surcharges can significantly inflate the overall expenditure, leading to budget overruns. This can be particularly problematic for businesses that operate under tight financial constraints or those that have allocated specific budgets for PPE supplies.
The Solution: To address this issue, buyers should seek suppliers who provide clear and comprehensive pricing breakdowns. It’s beneficial to request a detailed quote that includes all potential costs upfront, such as production, shipping, and any applicable taxes or duties. Engaging in open discussions with suppliers about pricing structures and negotiating terms can also lead to more favorable conditions. Additionally, buyers should consider using contracts that stipulate fixed pricing for the duration of the agreement, which can protect against unexpected price hikes. By ensuring a transparent pricing process, businesses can make more informed financial decisions and maintain better control over their budgets.
Strategic Material Selection Guide for mask supplier
When selecting materials for masks, it is essential to consider various factors that influence performance, cost, and compliance with international standards. Below, we analyze four common materials used in mask production, focusing on their properties, advantages, disadvantages, and implications for international B2B buyers.
What Are the Key Properties of Non-Woven Polypropylene for Masks?
Non-woven polypropylene is the most widely used material in disposable face masks, particularly the 3-ply surgical masks. This material is characterized by its excellent filtration capabilities, lightweight nature, and breathability. It can withstand temperatures up to 130°C, making it suitable for sterilization processes.
Pros and Cons:
– Pros: High filtration efficiency, cost-effective, and comfortable for extended wear.
– Cons: Limited durability under high humidity and can degrade when exposed to UV light.
Impact on Application:
Non-woven polypropylene is compatible with various media, including airborne particles and droplets, making it ideal for medical and industrial applications.
Considerations for International Buyers:
Buyers from regions like Africa and South America should ensure compliance with ASTM standards, which are crucial for medical-grade masks. In Europe, adherence to the EN 14683 standard is essential.
How Does Meltblown Fabric Enhance Mask Performance?
Meltblown fabric is a critical component in the filtration layers of masks, providing high filtration efficiency. This material is produced by extruding thermoplastic polymers and is known for its fine fiber structure, which captures smaller particles effectively.
Pros and Cons:
– Pros: Superior filtration performance, lightweight, and customizable thickness.
– Cons: Higher manufacturing complexity and cost compared to non-woven polypropylene.
Impact on Application:
Meltblown fabric is particularly effective in environments requiring high levels of protection, such as healthcare settings.
Considerations for International Buyers:
Buyers should prioritize suppliers who can provide certifications proving compliance with relevant filtration standards, such as NIOSH in the U.S. or FFP standards in Europe.
What Are the Benefits of Cotton as a Mask Material?
Cotton is increasingly being used in reusable masks, particularly in non-medical applications. It is breathable, comfortable, and can be easily washed and reused, making it a sustainable choice.
Pros and Cons:
– Pros: Eco-friendly, comfortable, and widely available.
– Cons: Lower filtration efficiency compared to synthetic materials and can retain moisture.
Impact on Application:
Cotton masks are suitable for general public use and in low-risk environments but may not provide adequate protection in healthcare settings.
Considerations for International Buyers:
Buyers should verify that cotton masks meet local regulations regarding fabric type and filtration efficiency, especially in regions with strict health guidelines.
Why Choose Activated Carbon for Specialized Masks?
Activated carbon is often used in masks designed for industrial applications, such as those protecting against fumes and odors. This material enhances the mask’s ability to filter out harmful gases and volatile organic compounds (VOCs).
Pros and Cons:
– Pros: Effective at adsorbing gases and odors, providing additional protection.
– Cons: Higher cost and may require more frequent replacement due to saturation.
Impact on Application:
Activated carbon masks are ideal for workers in industries such as construction and manufacturing, where exposure to harmful substances is common.
Considerations for International Buyers:
Buyers should ensure that activated carbon masks comply with local safety standards and regulations, particularly in regions with stringent occupational health requirements.
Summary Table of Material Properties for Mask Suppliers
Material | Typical Use Case for mask supplier | Key Advantage | Key Disadvantage/Limitation | Relative Cost (Low/Med/High) |
---|---|---|---|---|
Non-Woven Polypropylene | Disposable surgical masks | High filtration efficiency | Limited durability under humidity | Low |
Meltblown Fabric | Medical-grade masks | Superior filtration performance | Higher manufacturing complexity | Medium |
Cotton | Reusable masks | Eco-friendly and comfortable | Lower filtration efficiency | Low |
Activated Carbon | Industrial masks | Adsorbs gases and odors | Higher cost and frequent replacement | High |
By understanding the properties and implications of these materials, international B2B buyers can make informed decisions that align with their specific needs and compliance requirements.
In-depth Look: Manufacturing Processes and Quality Assurance for mask supplier
What Are the Key Stages in the Manufacturing Process of Masks?
The manufacturing process for masks, particularly disposable face masks, typically involves several crucial stages. Understanding these stages can help B2B buyers ensure they are sourcing products that meet their quality and safety requirements.
1. Material Preparation
The first stage involves the selection and preparation of raw materials. Masks are generally made from non-woven fabrics, which are created using techniques such as spunbond and meltblown processes. These materials are then cut into appropriate sizes for the mask layers. For example, a standard 3-ply mask consists of two layers of spunbond fabric sandwiching a meltblown filter layer. Buyers should inquire about the origin of these materials, as locally sourced materials may have different quality assurances than imported ones.
2. Forming the Mask
Once the materials are prepared, they move to the forming stage. This stage typically uses automated machines to shape the mask layers and attach them. Key techniques include ultrasonic welding, which bonds the layers together without the need for adhesives. This method is crucial for maintaining the integrity of the mask’s filtration capabilities. B2B buyers should look for manufacturers that utilize advanced technologies to ensure consistency and quality in their products.
3. Assembly
After forming, the mask components are assembled. This may include adding ear loops, nose wires, or other features that enhance fit and usability. The assembly process is critical, as any defects at this stage can compromise the mask’s effectiveness. Buyers should verify that suppliers have robust assembly protocols in place to minimize errors.
4. Finishing
The final stage of production involves quality checks and packaging. Masks are often sterilized before packaging to ensure they are free from contaminants. B2B buyers should pay attention to how the finished products are stored and packaged, as this can affect their safety and usability upon arrival.
How Is Quality Assurance Implemented in Mask Manufacturing?
Quality assurance (QA) is a vital aspect of mask manufacturing, ensuring that products meet international standards and buyer expectations.
Relevant International Standards for Masks
B2B buyers should be familiar with the relevant international standards for masks, such as:
- ISO 9001: This standard outlines the criteria for a quality management system and is crucial for any manufacturing process, including masks.
- CE Marking: In Europe, masks must comply with CE standards to be marketed. This indicates that the product meets health, safety, and environmental protection standards.
- ASTM Standards: In the U.S., ASTM standards classify masks based on their filtration efficiency and fluid resistance, such as ASTM Level 1, 2, or 3.
Understanding these certifications helps buyers assess the credibility of suppliers.
What Are the Key Quality Control Checkpoints?
Quality control (QC) involves several checkpoints throughout the manufacturing process:
-
Incoming Quality Control (IQC): This initial checkpoint ensures that raw materials meet specified standards before production begins. Buyers should ask suppliers for documentation proving the quality of incoming materials.
-
In-Process Quality Control (IPQC): During manufacturing, IPQC checks are conducted to monitor production processes and ensure that specifications are being met. This includes regular inspections of machinery and processes.
-
Final Quality Control (FQC): After production, FQC involves comprehensive testing of finished masks. Common tests include:
- Bacterial Filtration Efficiency (BFE) Testing: Measures the mask’s ability to filter bacteria.
- Particulate Filtration Efficiency (PFE) Testing: Assesses the mask’s filtration performance against particles.
- Breathability Testing: Evaluates the ease of breathing through the mask.
How Can B2B Buyers Verify Supplier Quality Control?
B2B buyers should take proactive steps to verify the quality control practices of their suppliers. Here are some actionable methods:
Conduct Supplier Audits
Regular audits of suppliers help ensure they adhere to quality standards. Buyers can request access to audit reports or even conduct on-site visits if feasible. This hands-on approach allows buyers to assess the manufacturing environment and processes directly.
Request Quality Assurance Documentation
Buyers should ask suppliers for quality assurance documentation, including certificates of compliance, test results, and records of past inspections. This paperwork provides insights into the supplier’s commitment to quality and adherence to international standards.
Utilize Third-Party Inspection Services
Engaging third-party inspection services can offer an unbiased assessment of a supplier’s quality control processes. These services often perform random inspections and testing, providing an additional layer of security for buyers.
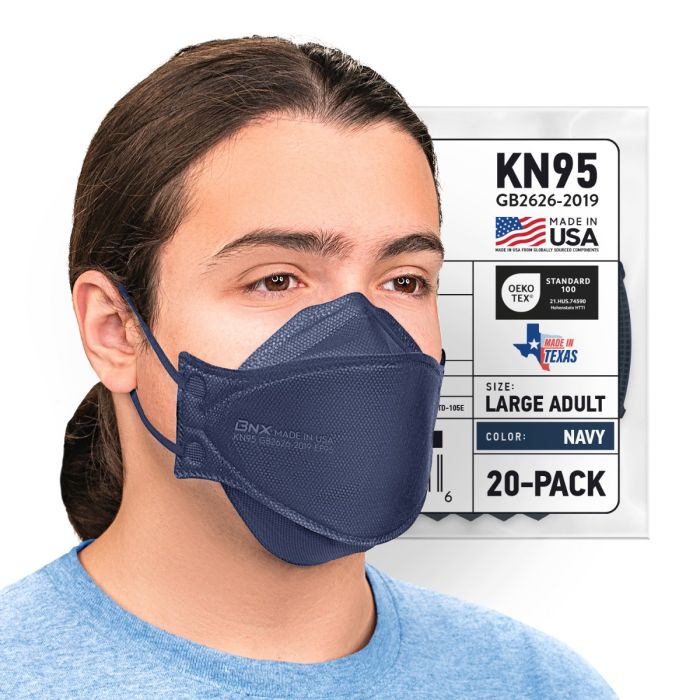
A stock image related to mask supplier.
What Nuances Should International Buyers Consider?
International buyers, especially those from regions like Africa, South America, the Middle East, and Europe, need to be aware of specific nuances when sourcing masks:
- Import Regulations: Different countries have varying import regulations regarding PPE. Understanding these regulations can help avoid legal issues and ensure compliance.
- Cultural Considerations: Preferences for mask types and designs may vary across regions. Buyers should research local market trends and consumer preferences to select suitable products.
- Supply Chain Reliability: Given the global nature of PPE supply chains, buyers should assess the reliability and stability of suppliers. This includes evaluating their capacity to meet demand spikes and manage logistics.
By focusing on the manufacturing processes and quality assurance practices of mask suppliers, B2B buyers can make informed decisions that ensure they are sourcing safe, effective, and compliant products.
Practical Sourcing Guide: A Step-by-Step Checklist for ‘mask supplier’
To successfully procure masks for your business needs, it’s essential to follow a structured approach. This guide outlines a step-by-step checklist designed specifically for B2B buyers, focusing on key actions that will help ensure you select a reliable mask supplier.
Step 1: Define Your Technical Specifications
Before initiating your search for mask suppliers, clearly outline your technical requirements. This includes determining the type of masks you need (e.g., surgical masks, KN95, N95) and their specifications, such as filtration efficiency, material, and compliance with local regulations.
- Consider the intended use: Are the masks for medical, industrial, or general use?
- Identify standards: Look for certifications like ASTM, FDA, or CE to ensure compliance with safety regulations.
Step 2: Research Potential Suppliers
Conduct thorough research to identify potential suppliers that align with your needs. Utilize online marketplaces, industry directories, and trade shows to compile a list of candidates.
- Check supplier reviews: Look for feedback from previous clients to gauge reliability and product quality.
- Examine their product range: Ensure they offer the specific types of masks you need and can meet your order volume.
Step 3: Verify Supplier Certifications
Supplier certifications are critical indicators of quality and compliance. Ensure that potential suppliers have the necessary certifications to manufacture masks in accordance with international safety standards.
- Request documentation: Ask for copies of certifications and testing results.
- Investigate their manufacturing process: Understand if they follow good manufacturing practices (GMP) and quality control measures.
Step 4: Assess Pricing and Payment Terms
Understanding the pricing structure and payment terms is vital for budgeting and financial planning. Gather quotes from multiple suppliers to compare costs.
- Evaluate total costs: Look beyond the unit price to consider shipping, duties, and taxes.
- Discuss payment options: Clarify payment terms such as deposits, credit terms, and payment methods to avoid future disputes.
Step 5: Request Samples for Evaluation
Before placing a bulk order, request samples to evaluate the quality of the masks. Testing samples can help you ensure that the products meet your specifications and quality standards.
- Perform quality checks: Assess the fit, comfort, and filtration efficiency of the masks.
- Involve end-users: Get feedback from your team or intended users to ensure the masks are suitable for their needs.
Step 6: Establish Communication and Support Channels
Effective communication is essential throughout the sourcing process. Confirm that the supplier has established channels for support and feedback.
- Determine responsiveness: Evaluate how quickly they respond to inquiries and their willingness to provide additional information.
- Clarify support options: Ensure they offer after-sales support, including handling complaints or product issues.
Step 7: Finalize Contracts and Agreements
Once you have selected a supplier, it’s time to formalize the agreement. Draft a contract that outlines all terms, including delivery schedules, payment terms, and quality expectations.
- Include performance metrics: Specify quality benchmarks and delivery timelines to hold the supplier accountable.
- Consider legal protections: Ensure that the contract includes clauses for dispute resolution and liability.
By following this structured checklist, B2B buyers can enhance their sourcing process for masks, ensuring they partner with reliable suppliers that meet their specific needs while adhering to safety standards.
Comprehensive Cost and Pricing Analysis for mask supplier Sourcing
What Are the Key Cost Components in Mask Supplier Sourcing?
Understanding the cost structure of mask suppliers is vital for international B2B buyers aiming to make informed purchasing decisions. The primary cost components include:
-
Materials: The choice of raw materials significantly impacts the overall cost. For instance, 3-ply masks use non-woven fabric, which can vary in price based on quality and source. Higher-grade materials, like those used in KN95 and N95 masks, typically command a premium.
-
Labor: Labor costs vary by region and can influence pricing. Suppliers based in countries with higher labor costs may charge more, whereas suppliers in regions with lower labor costs may offer more competitive pricing.
-
Manufacturing Overhead: This includes expenses related to factory operations, utilities, and equipment maintenance. Efficient manufacturing processes can help keep these costs down.
-
Tooling: Initial setup costs for specialized machinery or molds to produce custom designs can be significant. These costs are often amortized over larger production runs.
-
Quality Control (QC): Ensuring compliance with international standards (like ASTM or ISO certifications) incurs additional costs. Rigorous QC processes are necessary to ensure product safety and effectiveness, especially for medical-grade masks.
-
Logistics: Shipping and handling can vary widely based on the delivery location, volume, and Incoterms. Bulk orders may benefit from economies of scale, reducing the per-unit cost.
-
Margin: Suppliers will include a profit margin in their pricing, which can vary based on market demand, competition, and perceived value of their products.
How Do Price Influencers Affect Mask Supplier Costs?
Several factors can influence the pricing strategy of mask suppliers:
-
Volume/MOQ (Minimum Order Quantity): Purchasing in bulk often leads to lower prices per unit. Suppliers typically offer discounts for larger orders, which can be a crucial consideration for businesses anticipating high demand.
-
Specifications and Customization: Custom designs or specific features (like breathable materials or additional layers) can increase costs. Buyers must balance their needs against budget constraints.
-
Material Quality and Certifications: Masks that meet higher safety standards or are made from premium materials will come at a higher price. Buyers should assess the necessity of certifications based on their market and regulatory requirements.
-
Supplier Factors: The reputation and reliability of the supplier can impact pricing. Established suppliers may charge more due to their proven track record, while newer entrants might offer lower prices to gain market share.
-
Incoterms: The agreed-upon shipping terms (e.g., FOB, CIF) will affect overall pricing. Understanding these terms is crucial for calculating total landed costs and avoiding unexpected expenses.
What Negotiation and Cost-Efficiency Tips Should Buyers Consider?
For international B2B buyers, especially from diverse regions like Africa, South America, the Middle East, and Europe, cost-efficiency is paramount. Here are some actionable tips:
-
Negotiate Terms: Always negotiate pricing, payment terms, and shipping conditions. Suppliers may have flexibility that can lead to better deals, especially for repeat orders.
-
Consider Total Cost of Ownership (TCO): Evaluate all associated costs, including shipping, tariffs, and potential delays. A lower upfront cost might not always result in the best overall value.
-
Understand Pricing Nuances: Be aware of how local market conditions, currency fluctuations, and geopolitical factors may affect pricing. This knowledge can aid in making strategic purchasing decisions.
-
Build Relationships: Establishing long-term relationships with suppliers can lead to better pricing, priority service, and access to exclusive offers.
-
Stay Informed: Keep abreast of market trends and regulatory changes that may impact pricing. Being well-informed can enhance negotiation leverage.
Disclaimer on Indicative Prices
Prices for masks can vary significantly based on the factors outlined above. Buyers should seek quotes from multiple suppliers and conduct due diligence to ensure they are receiving competitive pricing reflective of their specific requirements.
Alternatives Analysis: Comparing mask supplier With Other Solutions
Understanding Alternatives to Mask Suppliers
In today’s global marketplace, businesses often face the challenge of selecting the most effective solutions for their safety and health needs. For companies looking to procure protective face masks, it’s essential to consider various alternatives that may offer similar or even superior benefits. This analysis compares traditional mask suppliers with innovative alternatives, helping B2B buyers from Africa, South America, the Middle East, and Europe make informed decisions.
Comparison Table
Comparison Aspect | Mask Supplier | Alternative 1: Reusable Masks | Alternative 2: Automated Disinfection Systems |
---|---|---|---|
Performance | High filtration efficiency | Moderate filtration efficiency | N/A |
Cost | Varies, typically bulk pricing | Lower long-term cost, higher upfront | High initial investment, low ongoing cost |
Ease of Implementation | Simple, requires no training | Requires user education | Requires installation and training |
Maintenance | Low, single-use | Moderate, requires washing and care | High, requires regular servicing |
Best Use Case | High-risk environments | General use, less critical situations | High-risk environments needing continuous protection |
What Are the Pros and Cons of Reusable Masks?
Pros: Reusable masks offer significant long-term cost savings as they can be washed and reused multiple times. They are often made from breathable materials, making them comfortable for extended wear. Additionally, they contribute to sustainability efforts by reducing waste.
Cons: The primary downside is their filtration efficiency, which may not match that of disposable masks, particularly in high-risk settings. They also require proper cleaning and maintenance, which can be a burden for some organizations, especially in regions with limited resources.
How Do Automated Disinfection Systems Compare?
Pros: Automated disinfection systems provide an innovative solution for maintaining a safe environment, especially in healthcare and high-traffic areas. They help in reducing the microbial load on surfaces and can complement mask usage by ensuring the overall safety of the environment.
Cons: The initial investment in automated systems can be substantial, which may deter smaller businesses or those with limited budgets. Additionally, these systems require regular maintenance and skilled personnel for operation, increasing the complexity of implementation.
Making the Right Choice for Your Business Needs
When considering mask suppliers and their alternatives, B2B buyers should assess their specific operational needs, budget constraints, and the level of risk associated with their industry. For organizations in high-risk environments, traditional mask suppliers may offer the best immediate protection. However, for businesses looking to balance cost-effectiveness with sustainability, reusable masks can be an appealing option. Alternatively, companies aiming for a comprehensive safety solution might find automated disinfection systems to be a worthwhile investment.
Ultimately, the decision should align with the organization’s health and safety protocols, workforce training capabilities, and budgetary considerations, ensuring a safe and effective environment for all employees and clients.
Essential Technical Properties and Trade Terminology for mask supplier
What Are the Key Technical Properties of Masks That B2B Buyers Should Understand?
When sourcing masks from suppliers, understanding the technical properties is crucial for ensuring product quality and compliance with safety standards. Here are some essential specifications to consider:
1. Material Grade
The material used in mask production significantly impacts its effectiveness. Common materials include polypropylene, which is widely used for its filtration efficiency and breathability. Buyers should ensure that the material meets relevant standards, such as ASTM for disposable masks, which indicates its suitability for medical use. This helps in assessing the mask’s durability and safety for end-users.
2. Filtration Efficiency
This specification indicates how well a mask can filter out particles. For instance, N95 masks filter at least 95% of airborne particles, while surgical masks have varying levels of filtration efficiency (ASTM Levels 1, 2, and 3). Understanding filtration efficiency is vital for buyers to ensure that the masks provide adequate protection for their intended use, especially in healthcare or industrial settings.
3. Breathability (Delta P)
Breathability is measured by the pressure differential (Delta P), which assesses the airflow resistance of the mask. A lower Delta P value indicates better breathability, making it more comfortable for prolonged use. B2B buyers should consider this property to enhance user comfort, especially for frontline workers who wear masks for extended periods.
4. Fluid Resistance
This property is particularly important for masks used in medical environments. Fluid resistance is measured in terms of how well a mask can prevent the penetration of liquids, which is crucial during procedures that may generate splashes. Buyers should look for masks that meet the ASTM F1862 standard for fluid resistance to ensure safety in healthcare settings.
5. Fit and Seal
A proper fit is essential for the mask to be effective. Masks should have adjustable features (like nose clips) to ensure a snug fit around the face. This is particularly relevant for N95 and KN95 masks, which require a tight seal to function effectively. Buyers should prioritize suppliers that offer masks with customizable fit options to cater to different facial shapes and sizes.
6. Shelf Life
The shelf life of masks indicates how long they can be stored without compromising their effectiveness. Buyers should check for expiration dates and storage conditions to ensure product reliability. Understanding shelf life helps businesses manage inventory better, avoiding the costs associated with expired products.
What Common Trade Terms Should B2B Buyers Be Familiar With When Sourcing Masks?
Familiarity with industry jargon can streamline communication and negotiations with suppliers. Here are some key terms:
1. OEM (Original Equipment Manufacturer)
OEM refers to a company that produces parts or products that are then marketed by another company. In the mask industry, an OEM may manufacture masks that are branded by a different company. Understanding OEM relationships can help buyers find suitable suppliers and negotiate better terms.
2. MOQ (Minimum Order Quantity)
MOQ is the smallest quantity of a product that a supplier is willing to sell. This term is crucial for B2B buyers as it affects inventory and cash flow. Understanding the MOQ helps buyers plan their purchases effectively, especially when sourcing in bulk.
3. RFQ (Request for Quotation)
An RFQ is a document sent to suppliers to request pricing and terms for specific products. B2B buyers often use RFQs to compare offers and negotiate better deals. Familiarity with this process can lead to significant cost savings.
4. Incoterms (International Commercial Terms)
Incoterms are a set of rules that define the responsibilities of buyers and sellers in international transactions. Terms like FOB (Free On Board) and CIF (Cost, Insurance, and Freight) dictate who pays for shipping and insurance. Understanding Incoterms is essential for B2B buyers to manage logistics and costs effectively.
5. Lead Time
Lead time refers to the time taken from placing an order to receiving the product. This is a critical factor for businesses that rely on timely delivery to meet customer demands. Buyers should inquire about lead times to ensure they can manage their inventory and supply chain effectively.
6. Certification
Certification indicates that a product meets specific standards set by regulatory bodies. For masks, certifications like FDA approval or CE marking signify compliance with safety and quality regulations. Buyers should prioritize certified products to ensure they meet local and international health standards.
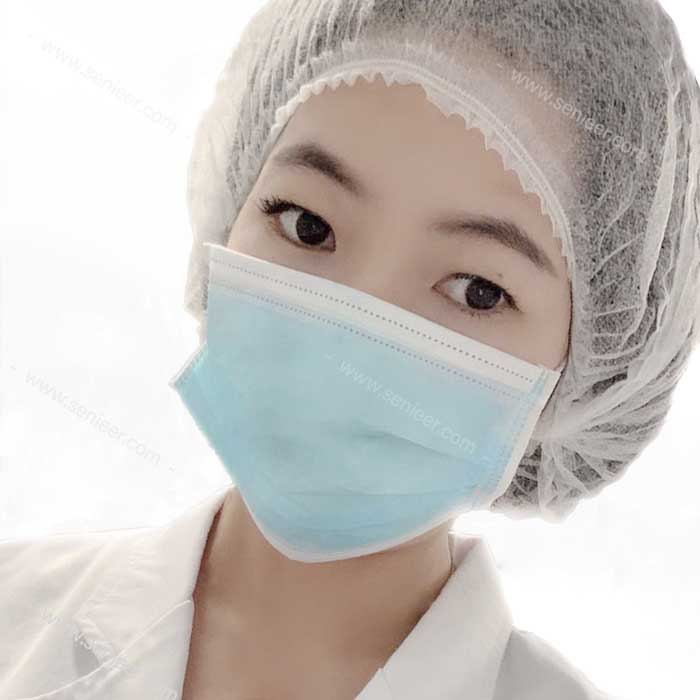
A stock image related to mask supplier.
By understanding these technical properties and trade terms, B2B buyers can make informed decisions when sourcing masks, ensuring they select high-quality products that meet their specific needs.
Navigating Market Dynamics and Sourcing Trends in the mask supplier Sector
What Are the Key Market Dynamics and Sourcing Trends in the Mask Supplier Sector?
The global mask supplier market has experienced significant shifts due to health crises, regulatory changes, and evolving consumer preferences. One of the primary drivers is the ongoing demand for Personal Protective Equipment (PPE), particularly in regions like Africa, South America, the Middle East, and Europe. The COVID-19 pandemic highlighted the necessity for reliable and accessible face coverings, leading to a surge in both domestic and international sourcing of masks. International B2B buyers should note that suppliers are increasingly adopting advanced technologies in manufacturing and logistics. Automation, digital supply chain management, and AI-driven inventory systems are becoming standard practices, enhancing efficiency and responsiveness.
Moreover, the market is seeing a diversification in product offerings. Beyond basic surgical and cloth masks, suppliers are introducing specialized options like KN95 and N95 respirators, which cater to higher safety standards. This trend is particularly relevant for buyers in sectors like healthcare, education, and manufacturing, where compliance with strict safety regulations is critical. Buyers should also be aware of the growing preference for bulk purchasing to secure better pricing and ensure supply continuity, particularly in regions facing supply chain disruptions.
How Is Sustainability Shaping the Mask Supplier Industry?
Sustainability and ethical sourcing are increasingly crucial in the mask supplier sector, especially as global awareness of environmental issues grows. The production and disposal of masks have significant environmental impacts, leading to a push for sustainable practices. B2B buyers should prioritize suppliers that demonstrate a commitment to sustainability through the use of eco-friendly materials and responsible manufacturing processes. This includes sourcing biodegradable or recyclable materials for masks, which can help mitigate waste and pollution.
Moreover, certifications like Global Organic Textile Standard (GOTS) or OEKO-TEX can serve as indicators of a supplier’s commitment to ethical sourcing. Buyers should inquire about the supply chain transparency of their suppliers, ensuring that labor practices are ethical and that materials are sourced responsibly. By aligning purchasing decisions with sustainability goals, businesses not only contribute to environmental stewardship but can also enhance their brand image and appeal to eco-conscious consumers.
What Is the Historical Context of the Mask Supplier Sector?
The mask supplier sector has evolved significantly over the decades, largely influenced by health crises and changing regulatory landscapes. Initially, masks were primarily used in healthcare settings, but the rise of infectious diseases and public health campaigns has broadened their application. The SARS outbreak in the early 2000s marked a turning point, bringing attention to the importance of personal protective equipment.
However, it was the COVID-19 pandemic that propelled the sector into the mainstream. The urgent need for protective gear led to the rapid expansion of manufacturing capacities worldwide, particularly in Asia and North America. This evolution has resulted in a more competitive landscape, with suppliers now focusing on quality, compliance, and innovation to meet the diverse needs of international buyers. As the industry continues to adapt to new challenges, understanding its historical context can provide valuable insights for B2B buyers seeking reliable suppliers.
Frequently Asked Questions (FAQs) for B2B Buyers of mask supplier
-
How do I ensure the quality of masks from a supplier?
To guarantee the quality of masks, request samples from potential suppliers before placing a bulk order. Verify that the masks meet relevant certifications, such as ASTM or ISO standards, and inquire about their manufacturing processes. It’s also beneficial to check customer reviews and testimonials, and if possible, conduct factory audits or inspections. Establishing a clear quality assurance agreement with your supplier will further ensure that the products meet your specifications consistently. -
What types of masks are best for different industries?
The type of mask needed can vary by industry. For healthcare settings, N95 or surgical masks are recommended due to their high filtration efficiency. In industrial environments, disposable 3-ply masks may suffice for protection against dust and particulates. Retail and hospitality sectors often prefer cloth masks or lightweight disposable masks for customer interactions. Understanding your specific requirements will help you choose the most suitable product for your needs. -
What is the minimum order quantity (MOQ) for masks from suppliers?
Minimum order quantities can vary significantly among suppliers. Generally, MOQs range from 500 to several thousand units depending on the type of masks and the supplier’s policies. When negotiating, consider your projected demand and discuss potential flexibility in MOQs, especially if you are a new buyer. Some suppliers may offer lower MOQs for first-time orders or trial runs, which can be advantageous for testing market response. -
What payment terms should I expect when sourcing masks internationally?
Payment terms vary by supplier and region, but common practices include partial upfront payment (often 30-50%) and the balance upon delivery or before shipping. For international transactions, consider using secure payment methods such as letters of credit or escrow services to protect your investment. It’s also important to clarify the currency of payment and any additional fees that may apply, such as bank transfer fees or foreign exchange charges. -
How do I vet a mask supplier for reliability and compliance?
Begin by researching the supplier’s reputation through online reviews and industry references. Check their certifications and compliance with relevant health and safety regulations. Request documentation that proves their manufacturing standards, such as ISO certifications. Engaging with suppliers through trade shows or industry events can also provide insights into their reliability. Establishing a good communication channel can help gauge their responsiveness and willingness to address your concerns.
-
What are the logistics considerations for importing masks?
When importing masks, consider factors such as shipping methods, lead times, and customs regulations. Work with suppliers who can provide clarity on logistics, including shipping costs and delivery times. Familiarize yourself with import duties and taxes applicable in your country, as these can impact the total cost. Additionally, ensure that your supplier can provide all necessary documentation for customs clearance, such as invoices, packing lists, and compliance certificates. -
Can I customize masks with my branding?
Yes, many suppliers offer customization options for masks, including printing your logo or brand colors. Customization typically requires a minimum order quantity and may involve additional costs. Discuss your design requirements with the supplier to understand the available options, production timelines, and any extra fees. Custom masks can enhance brand visibility and provide a professional image in corporate settings. -
What should I know about mask storage and shelf life?
Proper storage is crucial for maintaining the effectiveness of masks. They should be stored in a cool, dry place away from direct sunlight and moisture. Most disposable masks have a shelf life of two to three years, but it’s essential to check the manufacturer’s guidelines. Regularly inspect your inventory for any signs of damage or degradation, and ensure that masks are rotated based on their expiration dates to avoid using expired products.
Important Disclaimer & Terms of Use
⚠️ Important Disclaimer
The information provided in this guide, including content regarding manufacturers, technical specifications, and market analysis, is for informational and educational purposes only. It does not constitute professional procurement advice, financial advice, or legal advice.
While we have made every effort to ensure the accuracy and timeliness of the information, we are not responsible for any errors, omissions, or outdated information. Market conditions, company details, and technical standards are subject to change.
B2B buyers must conduct their own independent and thorough due diligence before making any purchasing decisions. This includes contacting suppliers directly, verifying certifications, requesting samples, and seeking professional consultation. The risk of relying on any information in this guide is borne solely by the reader.
Strategic Sourcing Conclusion and Outlook for mask supplier
As international B2B buyers navigate the evolving landscape of PPE procurement, the importance of strategic sourcing for masks cannot be overstated. By prioritizing suppliers who offer high-quality, certified products, such as ASTM-rated masks and reliable KN95 respirators, businesses can ensure compliance with safety regulations while safeguarding their workforce. Sourcing from manufacturers who are committed to quality assurance and local production not only supports economic resilience but also mitigates supply chain disruptions.
What Are the Key Benefits of Strategic Sourcing for Masks?
Strategic sourcing enables companies to leverage bulk purchasing power, resulting in cost savings and improved supply chain efficiency. Moreover, it fosters relationships with trusted suppliers, enhancing reliability and product availability. Buyers from regions such as Africa, South America, the Middle East, and Europe should actively seek partnerships with suppliers that can meet their specific needs, including customization options and expedited shipping.
How Can Buyers Prepare for Future Mask Procurement?
Looking ahead, international buyers should remain proactive in assessing their mask supply chains. Establishing multi-supplier strategies will provide flexibility and ensure access to essential PPE, even amid market fluctuations. By taking these steps, businesses can not only protect their employees but also position themselves as responsible and forward-thinking entities in an increasingly health-conscious world. Engage with suppliers today to secure your mask needs and enhance your operational resilience for tomorrow.