Unlock Savings: The Ultimate Guide to Shackle Manufacturers (2025)
Introduction: Navigating the Global Market for shackle manufacturer
In today’s competitive landscape, sourcing the right shackles from a reputable manufacturer can be a daunting challenge for international B2B buyers. With a multitude of options available, ensuring the safety, reliability, and compliance of shackles used in lifting and rigging applications is paramount. This comprehensive guide delves into the intricate world of shackle manufacturing, addressing key aspects such as types, applications, supplier vetting, and cost considerations. By providing detailed insights into various shackle configurations—like anchor and chain shackles—and their specific uses, this guide equips buyers from Africa, South America, the Middle East, and Europe with the knowledge necessary to make informed purchasing decisions.
Understanding the global market dynamics and regional variations is critical for buyers looking to optimize their supply chains. Whether you’re based in South Africa, Brazil, or Germany, our guide will navigate you through the complexities of selecting the right manufacturer, ensuring compliance with industry standards, and evaluating cost-effectiveness. With actionable strategies and expert advice, this resource empowers you to confidently engage with suppliers, ultimately enhancing operational efficiency and safety in your projects. Embrace the opportunity to elevate your procurement process and secure the best shackles for your specific needs with our well-rounded insights.
What Types of Shackles Are Available for Purchase?
How Can You Vet Shackle Manufacturers Effectively?
What Cost Factors Should You Consider When Sourcing Shackles?
How Do Regional Standards Affect Shackle Selection?
These questions and more will be explored, providing a thorough understanding of the shackle manufacturing landscape.
Understanding shackle manufacturer Types and Variations
Type Name | Key Distinguishing Features | Primary B2B Applications | Brief Pros & Cons for Buyers |
---|---|---|---|
Anchor Shackles | Larger, round “O” shaped bow; side-load capable | Marine applications, lifting, and towing | Pros: Versatile; can handle multiple sling legs. Cons: Reduced WLL when side-loaded. |
Chain Shackles | Narrower D-shaped bow; designed for in-line tension | Rigging, hoisting, and construction | Pros: High strength; compact design. Cons: Not suitable for side loading. |
Screw Pin Shackles | Pin secured by threading; offers extra security | Heavy lifting, construction, and mining | Pros: Enhanced safety; prevents accidental opening. Cons: Slower to connect/disconnect. |
Safety Shackles | Features a locking mechanism; prevents unintentional release | Industrial lifting and rigging | Pros: Improved safety; reduces risk of accidents. Cons: May be more expensive. |
Bow Shackles | Broad range of sizes; adaptable for various applications | General rigging, towing, and lifting | Pros: Versatile; suitable for various angles. Cons: Can be bulkier than other types. |
What Are the Characteristics of Anchor Shackles?
Anchor shackles, also known as bow shackles, are characterized by their larger, round “O” shaped bows, which allow for side loading and multiple sling connections. This versatility makes them ideal for marine applications, lifting, and towing. When purchasing anchor shackles, buyers should consider the working load limit (WLL) and ensure that the shackle can accommodate the angles of loading they expect to encounter, as side loading can reduce the WLL significantly.
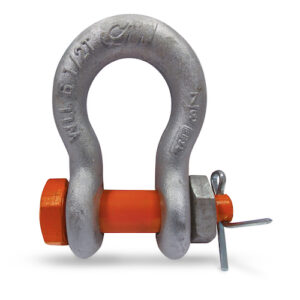
A stock image related to shackle manufacturer.
How Do Chain Shackles Differ from Other Types?
Chain shackles, or D shackles, feature a narrower, D-shaped bow specifically designed for in-line tension applications. They are commonly used in rigging, hoisting, and construction due to their high strength and compact design. However, buyers must be cautious not to side load these shackles, as doing so can compromise their structural integrity. When selecting chain shackles, it’s essential to choose the right size and WLL for the intended application.
What Are the Benefits of Screw Pin Shackles?
Screw pin shackles are distinguished by their pin, which is secured by threading, offering an added layer of security against accidental opening. This makes them particularly suitable for heavy lifting, construction, and mining applications where safety is paramount. While they provide enhanced safety, buyers should be aware that they may take longer to connect and disconnect compared to other types. Ensuring the right WLL is also crucial for effective use.
Why Consider Safety Shackles for Industrial Applications?
Safety shackles are designed with a locking mechanism that prevents unintentional release, making them a vital choice for industrial lifting and rigging. Their enhanced safety features reduce the risk of accidents, which is particularly important in environments with heavy equipment and loads. However, buyers should be prepared for a potentially higher cost compared to standard shackles. It’s advisable to evaluate the specific safety needs and regulations of your industry when considering safety shackles.
How Versatile Are Bow Shackles?
Bow shackles are versatile and come in a broad range of sizes, making them adaptable for various applications, including general rigging, towing, and lifting. Their design allows them to accommodate different angles, making them suitable for many lifting scenarios. However, buyers should consider their size and weight, as bow shackles can be bulkier than other types. Selecting the appropriate size and WLL is critical to ensure safety and effectiveness in the intended application.
Related Video: Variations In Construction Projects Explained
Key Industrial Applications of shackle manufacturer
Industry/Sector | Specific Application of shackle manufacturer | Value/Benefit for the Business | Key Sourcing Considerations for this Application |
---|---|---|---|
Construction | Lifting and hoisting heavy materials | Enhances safety and efficiency in material handling | Ensure compliance with local safety regulations and load ratings |
Marine & Offshore | Securing loads on vessels and offshore platforms | Provides reliable connections in harsh environments | Select corrosion-resistant materials suitable for marine applications |
Transportation & Logistics | Towing and securing cargo during transport | Minimizes risk of cargo loss and damage | Consider the weight capacity and compatibility with existing equipment |
Mining | Rigging and lifting heavy mining equipment | Increases operational efficiency and worker safety | Prioritize shackles with high tensile strength and durability |
Renewable Energy | Securing components in wind and solar installations | Supports the growing demand for sustainable energy solutions | Look for shackles with specialized designs for unique installation needs |
How Are Shackles Used in Construction Applications?
In the construction industry, shackles are essential for lifting and hoisting heavy materials such as steel beams and concrete slabs. They connect lifting slings and cranes, allowing for safe and efficient movement of loads. For international buyers, particularly from regions like Africa and South America, it is crucial to source shackles that comply with local safety standards and load ratings to prevent accidents and ensure project timelines are met.
What Role Do Shackles Play in Marine and Offshore Industries?
Marine and offshore operations rely heavily on shackles to secure loads on vessels and platforms. Shackles must withstand harsh environmental conditions, including saltwater exposure, which necessitates the use of corrosion-resistant materials. Buyers from the Middle East and Europe should prioritize sourcing shackles designed for marine applications to ensure reliability and safety during operations in challenging conditions.
How Are Shackles Important in Transportation and Logistics?
In transportation and logistics, shackles are vital for towing and securing cargo, ensuring that loads remain stable during transit. This minimizes the risk of cargo loss or damage, which can lead to significant financial repercussions. Buyers should consider the weight capacity of shackles and their compatibility with existing equipment, especially when sourcing for diverse transport conditions across different regions.
Why Are Shackles Critical in Mining Operations?
Shackles are extensively used in mining to rig and lift heavy equipment, such as drills and excavators. Their strength and durability are essential to maintain operational efficiency and ensure worker safety in demanding environments. International buyers must focus on shackles that offer high tensile strength and are suitable for the specific conditions of mining operations in their region.
How Do Shackles Support Renewable Energy Projects?
In the renewable energy sector, shackles are used to secure components in wind and solar installations, facilitating efficient assembly and maintenance. As the demand for sustainable energy solutions grows, sourcing shackles that meet specific design requirements for these applications is crucial. Buyers should look for shackles that provide the necessary strength and reliability to support innovative energy projects.
Related Video: Which Shackle Should You Be Using?
3 Common User Pain Points for ‘shackle manufacturer’ & Their Solutions
Scenario 1: Confusion Over Shackle Types and Specifications
The Problem: International B2B buyers often face challenges when selecting the appropriate type of shackle for specific applications. The diverse range of shackles—including bow shackles, D shackles, and specialty shackles—can be overwhelming. Misunderstanding the specifications can lead to using the wrong type, which not only compromises safety but may also result in costly operational delays and equipment damage. For example, a buyer might choose a D shackle for a side-loading application, which is inappropriate and dangerous.
The Solution: To effectively navigate the selection process, buyers should invest time in understanding the specific requirements of their applications. Start by clearly defining the load requirements, including the working load limit (WLL) and the nature of the load (static vs. dynamic). Utilize reputable resources, such as manufacturer catalogs and industry standards, to compare shackle types and their suitability for different tasks. Engaging with knowledgeable suppliers who can provide technical support and guidance is crucial. Conducting a thorough risk assessment and consulting with engineers or rigging specialists can ensure that the selected shackles meet the operational demands without compromising safety.
Scenario 2: Inconsistent Quality and Compliance Issues
The Problem: Many buyers encounter issues with inconsistent quality and compliance of shackles, especially when sourcing from multiple manufacturers or regions. This inconsistency can lead to safety hazards, as subpar shackles may not meet industry standards or regulations. For instance, a buyer in South America may receive shackles that do not comply with European safety certifications, which can result in legal liabilities and increased operational risks.
The Solution: To mitigate quality and compliance issues, it’s essential to establish a reliable supply chain with manufacturers that adhere to international standards such as ISO 9001 or specific lifting equipment regulations. Buyers should perform due diligence by requesting certifications and conducting audits of potential suppliers before making a purchase. Building long-term relationships with trusted manufacturers can lead to better product consistency and reliability. Additionally, consider implementing a robust quality assurance process that includes regular inspections and testing of shackles upon receipt. This proactive approach can help ensure that all shackles used in operations meet the necessary safety and compliance standards.
Scenario 3: Lack of Product Knowledge and Training Resources
The Problem: A significant pain point for B2B buyers is the lack of product knowledge and insufficient training resources for their teams. Employees responsible for selecting and using shackles may not have comprehensive training, leading to improper usage and increased risk of accidents. For example, a team in the Middle East may not be aware of the correct way to inspect shackles for wear and damage, resulting in unsafe practices.
The Solution: To address this gap, manufacturers should provide extensive training resources, including workshops, online courses, and instructional materials that cover the proper use, inspection, and maintenance of shackles. Buyers should actively seek out suppliers that offer these educational resources as part of their service. Implementing a training program for employees that includes hands-on sessions can significantly enhance their understanding and competency in using shackles safely. Additionally, companies can create a culture of safety by encouraging open discussions about rigging best practices and establishing a protocol for regular safety meetings. This investment in training not only promotes safer operations but can also lead to improved productivity and morale among team members.
Strategic Material Selection Guide for shackle manufacturer
What Are the Key Materials Used in Shackle Manufacturing?
When selecting shackles for various applications, the choice of material is crucial. Different materials offer distinct properties that can significantly influence performance, durability, and suitability for specific tasks. Below, we analyze four common materials used in shackle manufacturing, focusing on their key properties, advantages, disadvantages, and considerations for international B2B buyers.
How Does Steel Perform as a Material for Shackles?
Key Properties:
Steel is the most widely used material for shackles due to its high tensile strength and durability. It typically has excellent temperature and pressure ratings, making it suitable for heavy lifting and rigging applications. Steel shackles can be treated with coatings to enhance corrosion resistance.
Pros & Cons:
The primary advantage of steel shackles is their strength, which allows them to handle heavy loads with ease. However, they can be prone to rust and corrosion if not properly coated or maintained, particularly in humid or marine environments. The manufacturing process can be complex, involving forging and heat treatment, which may increase costs.
Impact on Application:
Steel shackles are compatible with a wide range of lifting and rigging applications, including construction and shipping. However, buyers must ensure that the shackles meet relevant standards such as ASTM or DIN to guarantee safety and performance.
What Are the Benefits of Using Stainless Steel for Shackles?
Key Properties:
Stainless steel offers excellent corrosion resistance, making it ideal for applications in harsh environments, such as marine or chemical settings. It maintains its strength at elevated temperatures and does not rust, which is a significant advantage over regular steel.
Pros & Cons:
The key advantage of stainless steel shackles is their longevity and reduced maintenance requirements. However, they are typically more expensive than carbon steel options, which may be a consideration for budget-conscious buyers. The manufacturing process can also be more complex, potentially leading to longer lead times.
Impact on Application:
Stainless steel shackles are particularly suited for industries such as oil and gas, where exposure to corrosive substances is common. International buyers should verify compliance with industry standards and certifications to ensure quality.
Why Choose Alloy Steel for Shackles?
Key Properties:
Alloy steel shackles are engineered for enhanced strength and toughness. They are often treated to improve their resistance to wear and fatigue, making them suitable for high-load applications.
Pros & Cons:
The primary advantage of alloy steel shackles is their high strength-to-weight ratio, allowing for lighter designs without compromising load capacity. However, they can be more expensive than standard steel options, and their manufacturing process may require specialized techniques.
Impact on Application:
These shackles are commonly used in heavy lifting and construction applications. Buyers must consider the specific alloy composition and its compliance with international standards, as different alloys may have varying properties.
What Role Does Plastic Play in Shackle Manufacturing?
Key Properties:
Plastic shackles, often made from high-density polyethylene (HDPE) or nylon, are lightweight and resistant to corrosion. They can operate effectively in a wide range of temperatures and are non-conductive, making them suitable for electrical applications.
Pros & Cons:
The advantage of plastic shackles is their lightweight nature and resistance to chemicals, making them ideal for specific applications like water sports or temporary rigging. However, they lack the load-bearing capacity of metal shackles and are typically not suitable for heavy lifting tasks.
Impact on Application:
Plastic shackles are often used in recreational or low-stress applications. International buyers should ensure that these products meet safety standards for their intended use, as the lack of strength may limit their application scope.
Summary Table of Materials for Shackle Manufacturing
Material | Typical Use Case for shackle manufacturer | Key Advantage | Key Disadvantage/Limitation | Relative Cost (Low/Med/High) |
---|---|---|---|---|
Steel | Heavy lifting, construction | High strength and durability | Prone to rust without coating | Medium |
Stainless Steel | Marine, chemical applications | Excellent corrosion resistance | Higher cost compared to steel | High |
Alloy Steel | Heavy lifting, construction | High strength-to-weight ratio | More expensive and complex to manufacture | High |
Plastic | Recreational, low-stress applications | Lightweight and corrosion-resistant | Limited load capacity | Low |
This strategic material selection guide provides international B2B buyers with essential insights into the various materials used in shackle manufacturing, helping them make informed decisions based on their specific application needs and regional compliance requirements.
In-depth Look: Manufacturing Processes and Quality Assurance for shackle manufacturer
What Are the Key Stages in the Manufacturing Process of Shackles?
The manufacturing process for shackles involves several critical stages, each designed to ensure that the final product meets safety and performance standards. Understanding these stages is vital for B2B buyers, particularly those in regions like Africa, South America, the Middle East, and Europe.
1. Material Preparation: What Raw Materials Are Used for Shackles?
The journey begins with the selection of high-quality raw materials, typically alloy steels or stainless steel, which are essential for ensuring strength and durability. The chosen material undergoes thorough inspection before processing. This step includes checking for impurities, ensuring the appropriate chemical composition, and confirming that the material meets the required mechanical properties.
2. Forming: How Are Shackles Shaped and Molded?
The forming stage involves shaping the raw material into the desired shackle configuration using techniques such as forging and casting.
-
Forging: This is the most common method for producing shackles. The steel is heated and then shaped under high pressure to achieve the final form. Forged shackles often exhibit superior strength and resistance to fatigue.
-
Casting: In some cases, shackles can be produced through casting, where molten metal is poured into a mold. While this method can be cost-effective, it typically results in a product that is less durable than forged options.
Precision in this stage is critical, as any deviations can lead to failures in load-bearing applications.
3. Assembly: How Are Shackles Assembled and Secured?
After forming, the individual components of the shackle, such as the bow and pin, are assembled. During assembly, attention must be paid to ensure that each part fits perfectly and that the pin can be easily inserted and removed. The assembly process also includes any additional features, such as safety mechanisms, that enhance the shackle’s functionality.
What Quality Assurance Processes Are Essential for Shackles?
Quality assurance is paramount in the manufacturing of shackles, particularly given the safety implications associated with their use in lifting and rigging applications.
1. What International Standards Should B2B Buyers Be Aware Of?
B2B buyers should be familiar with several international quality standards that apply to shackle manufacturing:
-
ISO 9001: This is a globally recognized standard that outlines the criteria for a quality management system. Companies that are ISO 9001 certified demonstrate a commitment to quality and continual improvement.
-
CE Marking: In Europe, shackles used in lifting operations must comply with the EU Machinery Directive, which requires CE marking to indicate conformity with safety standards.
-
API Standards: For industries such as oil and gas, shackles may also need to meet American Petroleum Institute (API) standards, which are specific to equipment used in these sectors.
2. What Are the Quality Control Checkpoints During Manufacturing?
To maintain high-quality standards, manufacturers implement multiple quality control checkpoints throughout the production process:
-
Incoming Quality Control (IQC): This initial check ensures that all incoming materials meet specified requirements before they enter the production line.
-
In-Process Quality Control (IPQC): During manufacturing, periodic inspections are conducted to ensure that processes are being followed correctly and that products are being made according to specifications.
-
Final Quality Control (FQC): After assembly, each shackle undergoes a final inspection to confirm that it meets all quality and safety standards before being shipped.
What Testing Methods Are Commonly Used for Shackles?
To ensure the reliability of shackles, manufacturers employ various testing methods:
-
Load Testing: Shackles are subjected to load tests to verify their working load limits (WLL). This involves applying a specific load to the shackle and observing its performance.
-
Non-Destructive Testing (NDT): Techniques such as ultrasonic testing or magnetic particle inspection are used to detect internal and surface defects without damaging the product.
-
Visual Inspection: A thorough visual inspection is performed to check for any obvious defects, including cracks, misalignment, or surface imperfections.
How Can B2B Buyers Verify Supplier Quality Assurance?
When sourcing shackles from manufacturers, B2B buyers should adopt a proactive approach to verify quality assurance practices:
-
Conduct Supplier Audits: Regular audits of potential suppliers can help assess their quality management systems and adherence to international standards.
-
Request Quality Reports: Suppliers should be willing to provide detailed quality control reports, including results from testing and inspections.
-
Third-Party Inspections: Engaging third-party inspection services can provide an unbiased assessment of the manufacturing processes and quality assurance measures in place.
What Are the Quality Control Nuances for International Buyers?
For international B2B buyers, especially those from Africa, South America, the Middle East, and Europe, understanding the nuances of quality control is essential. Different regions may have varying regulatory requirements and standards. Buyers should familiarize themselves with local regulations and ensure that their suppliers are compliant.
Additionally, language barriers and logistical challenges may complicate quality assurance processes. Therefore, establishing clear communication channels and setting explicit quality expectations is crucial for successful international sourcing.
Conclusion: How to Ensure Quality in Shackles for Your Business?
In summary, a comprehensive understanding of the manufacturing processes and quality assurance measures for shackles is vital for international B2B buyers. By focusing on material selection, manufacturing techniques, and rigorous quality control, businesses can ensure they procure shackles that meet safety and performance standards. Engaging in thorough supplier evaluations, requesting quality documentation, and understanding local regulations will further empower buyers to make informed decisions in their sourcing efforts.
Practical Sourcing Guide: A Step-by-Step Checklist for ‘shackle manufacturer’
Introduction
Navigating the procurement of shackles for lifting and rigging applications requires careful consideration and strategic planning. This guide provides a practical checklist for B2B buyers, particularly those from Africa, South America, the Middle East, and Europe, to ensure you source the right shackle manufacturer effectively. By following these steps, you can mitigate risks, enhance safety, and ensure compliance with industry standards.
Step 1: Define Your Technical Specifications
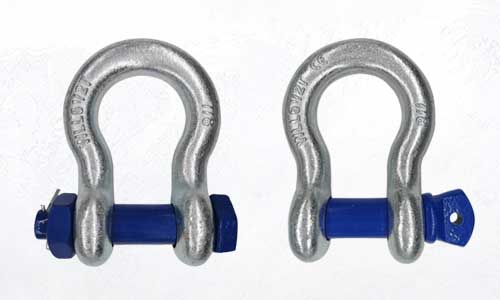
A stock image related to shackle manufacturer.
Establishing clear technical specifications is the foundation of your sourcing process. This includes determining the type of shackles required (e.g., anchor shackles vs. D shackles) based on your specific lifting or rigging needs.
- Consider factors such as:
- Working Load Limit (WLL)
- Material specifications (e.g., stainless steel, alloy)
- Environmental conditions (e.g., exposure to corrosion)
Step 2: Research Potential Manufacturers
Conduct thorough research on potential shackle manufacturers. Look for companies with a proven track record in producing high-quality shackles that meet international standards.
- Focus on:
- Customer reviews and testimonials
- Industry certifications (e.g., ISO, CE marking)
- Years of experience in the industry
Step 3: Verify Supplier Certifications
Confirm that the manufacturers have the necessary certifications to produce shackles compliant with safety and quality standards. This step ensures that the products you receive will be safe and reliable.
- Look for:
- Certification from recognized bodies (e.g., ANSI, ASME)
- Documentation of quality control processes
- Evidence of product testing and validation
Step 4: Request Samples for Testing
Before making a bulk purchase, request samples of the shackles you intend to buy. Testing these samples allows you to evaluate their quality and suitability for your applications.
- Pay attention to:
- Physical characteristics (dimensions, weight)
- Load-bearing capacity
- Finish and corrosion resistance
Step 5: Evaluate Pricing and Terms of Sale
Understanding the pricing structure and terms of sale is crucial for budget management. Request detailed quotations from multiple suppliers to compare costs effectively.
- Consider:
- Bulk purchase discounts
- Payment terms and conditions
- Shipping and handling fees
Step 6: Assess Customer Support and After-Sales Service
Effective customer support can significantly impact your procurement experience. Assess the level of support provided by the manufacturer throughout the purchasing process and beyond.
- Inquire about:
- Availability of technical support
- Warranty and return policies
- Training or resources for product usage
Step 7: Finalize the Contract and Place Your Order
Once you have evaluated all aspects and are satisfied with your chosen supplier, proceed to finalize the contract. Ensure that all agreed terms, specifications, and delivery timelines are clearly outlined.
- Key elements to include:
- Payment schedules
- Delivery dates
- Conditions for order modifications or cancellations
Following these steps will help you make informed decisions when sourcing shackles from manufacturers, ensuring that you choose a supplier that aligns with your operational needs and safety standards.
Comprehensive Cost and Pricing Analysis for shackle manufacturer Sourcing
What Are the Key Cost Components in Shackle Manufacturing?
When sourcing shackles, understanding the cost structure is essential for B2B buyers. The main cost components typically include:
-
Materials: The primary materials used in shackles are steel alloys, which can vary in cost depending on the grade and quality. High-strength materials may incur a premium but are critical for safety and reliability.
-
Labor: This encompasses the wages paid to skilled workers involved in the manufacturing process. Regions with higher labor costs, such as parts of Europe, may affect overall pricing.
-
Manufacturing Overhead: This includes costs associated with running the manufacturing facility, such as utilities, maintenance, and administrative expenses. Efficient operations can help minimize these costs.
-
Tooling: The initial investment in molds and dies necessary for producing shackles can be significant. Custom tooling may be required for specialized designs, impacting upfront costs.
-
Quality Control (QC): Stringent quality assurance processes are necessary to meet safety standards, which can add to the overall cost of production.
-
Logistics: Transportation costs from the manufacturer to the buyer’s location can fluctuate based on distance, shipping method, and any tariffs or duties that may apply.
-
Margin: Manufacturers typically add a profit margin to cover their costs and ensure sustainability. This can vary significantly depending on the supplier’s positioning in the market.
How Do Price Influencers Affect Shackle Sourcing Costs?
Several factors can influence the pricing of shackles in international B2B sourcing:
-
Volume and Minimum Order Quantity (MOQ): Larger orders often lead to lower per-unit costs due to economies of scale. Understanding the MOQ is crucial for negotiating better prices.
-
Specifications and Customization: Customized shackles designed for specific applications will generally cost more than standard products. Buyers should clearly communicate their requirements to avoid unexpected costs.
-
Materials and Quality Certifications: Higher quality materials and certifications (e.g., ISO, CE) can increase costs but are essential for compliance with safety regulations, especially in industries like construction and shipping.
-
Supplier Factors: The reputation and reliability of the supplier can significantly impact pricing. Established suppliers may charge more due to their proven quality and service.
-
Incoterms: The choice of Incoterms affects shipping costs and responsibilities. Understanding terms like FOB (Free on Board) or CIF (Cost, Insurance, and Freight) is vital for accurate budgeting.
What Are the Best Negotiation Tips for B2B Buyers in Shackles Procurement?
When engaging in negotiations for shackles, consider the following strategies to enhance cost-efficiency:
-
Understand Total Cost of Ownership (TCO): Look beyond the initial purchase price. Consider maintenance, operational efficiency, and potential downtime costs associated with lower-quality shackles.
-
Leverage Competitive Quotes: Gather multiple quotes from different suppliers. This provides leverage in negotiations and helps identify a fair market price.
-
Build Long-Term Relationships: Establishing a good rapport with suppliers can lead to more favorable terms and pricing in the long run. Loyalty can sometimes yield discounts or priority service.
-
Be Transparent About Needs: Clearly articulate your requirements and expected volumes. This helps suppliers tailor their offers and may lead to better pricing.
-
Stay Informed About Market Trends: Keeping abreast of material costs and industry trends can aid in timing your purchase effectively and negotiating from a position of knowledge.
What Should International Buyers Consider Regarding Pricing Nuances?
For international B2B buyers, especially from Africa, South America, the Middle East, and Europe, understanding pricing nuances is critical:
-
Currency Fluctuations: Be mindful of exchange rates that can affect costs significantly. Consider negotiating prices in a stable currency.
-
Tariffs and Trade Regulations: Import duties can add unexpected costs. Understanding these regulations in your country can help in accurate pricing assessments.
-
Cultural Sensitivities: Different regions may have varying expectations regarding negotiations and pricing discussions. Being aware of these can facilitate smoother transactions.
Disclaimer on Indicative Prices
Prices for shackles can vary widely based on the factors discussed above. It is recommended to conduct thorough research and obtain up-to-date quotes from multiple suppliers to ensure accurate budgeting and procurement strategies.
Alternatives Analysis: Comparing shackle manufacturer With Other Solutions
Exploring Alternatives to Shackle Manufacturers in Rigging Solutions
In the world of rigging and load securement, shackles serve as critical components for connecting lifting slings and other hardware. However, various alternatives exist that can provide similar benefits depending on specific applications and operational needs. This analysis will compare traditional shackle manufacturers with other viable solutions, helping international B2B buyers from Africa, South America, the Middle East, and Europe make informed decisions.
Comparison Aspect | Shackle Manufacturer | Synthetic Slings | Quick Links |
---|---|---|---|
Performance | High strength, versatile for various loads | Lower strength than metal, but flexible and lightweight | Ideal for lifting and towing |
Cost | Moderate to high | Generally lower | Cost-effective for repetitive use |
Ease of Implementation | Simple and straightforward | Requires training for proper use | Easy to transport and store |
Maintenance | Requires regular inspection | Minimal maintenance needed | Less wear and tear |
Best Use Case | Heavy lifting and industrial applications | Situations where weight and flexibility are critical | Ideal for construction and outdoor activities |
What Are the Advantages and Disadvantages of Synthetic Slings?
Synthetic Slings: These lifting devices, made from materials such as nylon or polyester, offer unique advantages in specific scenarios. They are lightweight, flexible, and reduce the risk of damage to the load due to their soft surfaces. However, their working load limits (WLL) are typically lower than those of metal shackles, which may limit their use in heavy lifting applications. Synthetic slings also require proper training for safe handling and deployment, as improper use can lead to accidents. Overall, they are best suited for scenarios where weight and flexibility are more critical than maximum load capacity.
How Do Quick Links Compare as an Alternative?
Quick Links: These are connectors that offer a quick and easy way to attach and detach lifting equipment. While quick links can be convenient, they generally do not provide the same level of load-bearing capacity as traditional shackles. They are best used for lighter loads or applications where frequent connections and disconnections are necessary. The ease of use is a significant advantage, making them popular in certain industries. However, quick links may not be suitable for heavy-duty applications where safety and high strength are paramount.
Conclusion: How to Choose the Right Rigging Solution for Your Needs
When selecting a rigging solution, B2B buyers should carefully evaluate their specific requirements, including load capacity, operational conditions, and budget constraints. Traditional shackles provide robustness and reliability for heavy lifting, while synthetic slings offer flexibility and cost-effectiveness for lighter applications. Quick links serve their purpose in situations where speed and convenience are prioritized. Ultimately, the right choice will depend on a thorough assessment of the application needs, safety standards, and the operational environment.
Essential Technical Properties and Trade Terminology for shackle manufacturer
What Are the Essential Technical Properties of Shackles for B2B Buyers?
When selecting shackles for lifting and rigging applications, it is crucial for international B2B buyers to understand the technical specifications that ensure safety and performance. Here are some key properties to consider:
1. Material Grade: What Should You Look For?
Shackles are commonly made from various materials, including carbon steel, alloy steel, and stainless steel. The material grade determines the shackle’s strength and resistance to corrosion. For instance, Grade 80 and Grade 100 shackles are made from high-strength alloy steel and are suitable for heavy lifting tasks. Buyers must ensure that the material grade meets the requirements of their specific applications, especially in demanding environments like construction or maritime operations.
2. Working Load Limit (WLL): How Is It Calculated?
The Working Load Limit is a critical specification that indicates the maximum load a shackle can safely handle. It is essential for B2B buyers to understand that the WLL must be greater than the actual load to prevent rigging failures. Buyers should also consider the angle of loading, as side loading can reduce the effective WLL. Always verify that the selected shackle has a WLL suitable for the application at hand.
3. Tolerance: Why Is Precision Important?
Tolerance refers to the permissible limit of variation in the dimensions of the shackle. High precision in manufacturing ensures that shackles fit well with other rigging equipment, minimizing the risk of failures due to improper fit. Buyers should inquire about tolerance standards to ensure compatibility with their existing lifting systems.
4. Finish and Coating: What Protection Do You Need?
The finish or coating of a shackle can significantly influence its durability and corrosion resistance. Common finishes include galvanized, powder-coated, or painted options. For industries operating in harsh environments, such as marine or industrial settings, selecting shackles with appropriate coatings can prolong service life and reduce maintenance costs.
5. Pin Type: What Are Your Options?
Shackles can have different types of pins, including screw pins, bolt-type pins, and safety pins. The choice of pin type affects both security and ease of use. For example, screw pins are easy to use and offer a reliable connection, while safety pins provide additional security against accidental disengagement. Understanding the advantages of each pin type helps buyers select the right shackle for their application.
What Are Common Trade Terms Used in the Shackle Manufacturing Industry?
Familiarity with industry terminology is essential for B2B buyers to navigate the purchasing process effectively. Here are some common terms:
1. OEM (Original Equipment Manufacturer): What Does It Mean?
OEM refers to companies that manufacture products that can be marketed under another company’s brand. In the context of shackles, buyers often look for OEMs to ensure they receive quality products that meet industry standards. Sourcing from reputable OEMs can lead to better reliability and performance.
2. MOQ (Minimum Order Quantity): How Does It Affect Your Purchase?
MOQ is the smallest quantity of products that a supplier is willing to sell. Understanding MOQ is critical for buyers, especially small and medium enterprises, as it can impact their cash flow and inventory management. Negotiate MOQs with suppliers to align with your purchasing needs without overcommitting.
3. RFQ (Request for Quotation): Why Is It Important?
An RFQ is a document sent to suppliers to request pricing and terms for specific products. Issuing an RFQ allows buyers to compare offers from different manufacturers, ensuring they get the best value for their investment. It is a vital step in the procurement process, particularly for large orders.
4. Incoterms: What Do They Dictate?
Incoterms are international commercial terms that define the responsibilities of buyers and sellers in international trade. Understanding Incoterms is crucial for B2B buyers as they outline who is responsible for shipping, insurance, and tariffs. Properly defining these terms can prevent disputes and ensure smooth transactions.
By grasping these essential technical properties and industry terms, international B2B buyers can make informed decisions when procuring shackles, ensuring safety and efficiency in their operations.
Navigating Market Dynamics and Sourcing Trends in the shackle manufacturer Sector
What Are the Current Trends Shaping the Shackle Manufacturing Market?
The shackle manufacturing sector is experiencing dynamic shifts influenced by global drivers such as increased industrial activity, infrastructure development, and a growing demand for safe lifting and rigging solutions. In regions like Africa and South America, rapid urbanization is fostering construction and mining activities, which in turn boosts the demand for robust rigging hardware. Meanwhile, the Middle East is seeing significant investment in oil and gas projects, further propelling the need for high-quality shackles.
Emerging technologies are reshaping sourcing strategies, with B2B buyers increasingly leveraging digital platforms for procurement. E-commerce solutions and online marketplaces are streamlining the buying process, enabling buyers from various regions to access a wider range of products and suppliers. Moreover, advancements in material science have led to the development of lighter and stronger shackles, improving efficiency in lifting operations. International buyers should stay attuned to these trends to optimize their sourcing strategies and enhance operational efficiency.
How Is Sustainability Influencing the Shackle Manufacturing Sector?
Sustainability is becoming a crucial focus in the shackle manufacturing industry, driven by both regulatory requirements and market demand for ethical sourcing. Environmental impact considerations are prompting manufacturers to adopt greener production methods, such as using recycled materials and reducing energy consumption. This shift is not only beneficial for the environment but also enhances brand reputation among increasingly eco-conscious consumers and businesses.
B2B buyers should prioritize suppliers with certifications that demonstrate a commitment to sustainability, such as ISO 14001 for environmental management and other green certifications. Additionally, sourcing shackles made from eco-friendly materials can significantly reduce the carbon footprint of supply chains. Engaging with manufacturers who adhere to ethical labor practices and transparent sourcing can further strengthen buyer credibility and compliance with international standards.
How Has the Shackle Manufacturing Sector Evolved Over Time?
The shackle manufacturing industry has a rich history, evolving from rudimentary designs used in ancient maritime applications to sophisticated, high-strength products integral to modern construction and logistics. Early shackles were crafted from wrought iron, primarily for ship rigging, while today’s shackles are engineered from advanced materials like alloy steel and even composites, offering enhanced strength-to-weight ratios.
This evolution reflects broader technological advancements within the manufacturing sector, including the adoption of computer-aided design (CAD) and precision engineering. As industries evolve, so do the demands placed on shackles, necessitating continuous innovation to meet safety standards and operational requirements. For B2B buyers, understanding this historical context can inform decisions on product selection and supplier partnerships, ensuring they align with cutting-edge practices and technologies.
Frequently Asked Questions (FAQs) for B2B Buyers of shackle manufacturer
-
How do I select the right type of shackle for my lifting needs?
Selecting the appropriate shackle depends on several factors, including the type of load, lifting angle, and working load limit (WLL). For general lifting, consider using anchor (bow) shackles, which allow for multiple sling-leg connections and can handle side loading. If your application requires in-line tension, opt for chain (D) shackles, which are not suitable for side loading. Always ensure the selected shackle meets or exceeds the WLL of your rigging equipment to avoid failures. -
What is the best shackle for heavy-duty lifting applications?
For heavy-duty lifting, anchor shackles are typically the best choice due to their wider bows that accommodate multiple connections and side loads. Ensure that the shackles are made from high-strength materials like alloy steel to withstand demanding environments. Always verify that the shackles are certified to meet international safety standards, as this ensures reliability and safety during operation. -
How can I verify the quality of shackles from international manufacturers?
To ensure quality, request certifications such as ISO 9001 and relevant safety standards from your suppliers. It’s also beneficial to ask for test reports that demonstrate the shackles’ load capacity and durability. Additionally, consider conducting factory audits or utilizing third-party inspection services to evaluate the manufacturing processes and materials used. Engaging with suppliers who have a strong reputation and customer testimonials can further assure quality. -
What are the minimum order quantities (MOQs) for shackles from manufacturers?
Minimum order quantities can vary significantly between manufacturers and depend on factors such as the type of shackle and customization options. Typically, MOQs range from 50 to 500 units for standard shackles, while customized products may have higher MOQs. It’s advisable to discuss your specific needs with suppliers to negotiate favorable terms that align with your procurement strategy. -
What payment terms are commonly accepted by shackle manufacturers?
Payment terms vary among manufacturers but typically include options like a deposit upfront (commonly 30%) and the balance upon shipment or delivery. Some manufacturers may offer letters of credit or payment via escrow services for larger orders. It is crucial to clarify payment terms before committing to ensure they align with your budgeting and cash flow requirements. -
How do I handle logistics and shipping for shackles sourced internationally?
When sourcing shackles internationally, consider partnering with freight forwarders who specialize in industrial goods to streamline logistics. Discuss shipping options, including air freight for faster delivery or sea freight for cost savings. Ensure that you understand the incoterms (International Commercial Terms) involved, as they dictate the responsibilities of buyers and sellers regarding shipping, insurance, and tariffs.
-
What customization options are available for shackles?
Many manufacturers offer customization options, including size variations, materials, and finishing (e.g., galvanization for corrosion resistance). You can also request specific pin types, such as screw pins or safety pins, depending on your application needs. Discuss your requirements with manufacturers to explore available options and ensure the customized shackles meet your operational demands. -
What quality assurance measures should I expect from shackle manufacturers?
Reputable manufacturers should implement robust quality assurance measures, including material inspections, load testing, and regular audits of production processes. They should also provide detailed documentation, such as certificates of compliance and material safety data sheets. Requesting information about their quality management system will help ensure that the shackles you receive meet both safety and performance standards.
Important Disclaimer & Terms of Use
⚠️ Important Disclaimer
The information provided in this guide, including content regarding manufacturers, technical specifications, and market analysis, is for informational and educational purposes only. It does not constitute professional procurement advice, financial advice, or legal advice.
While we have made every effort to ensure the accuracy and timeliness of the information, we are not responsible for any errors, omissions, or outdated information. Market conditions, company details, and technical standards are subject to change.
B2B buyers must conduct their own independent and thorough due diligence before making any purchasing decisions. This includes contacting suppliers directly, verifying certifications, requesting samples, and seeking professional consultation. The risk of relying on any information in this guide is borne solely by the reader.
Strategic Sourcing Conclusion and Outlook for shackle manufacturer
How Can Strategic Sourcing Enhance Your Shackle Procurement?
In conclusion, strategic sourcing plays a pivotal role in optimizing the procurement process for shackles, ensuring that international B2B buyers benefit from quality, safety, and cost-effectiveness. By understanding the different types of shackles—such as anchor and chain shackles—and their specific applications, buyers can make informed decisions that align with their operational needs. Additionally, leveraging relationships with reputable manufacturers and distributors can provide access to innovative products and reliable supply chains, particularly crucial for industries in Africa, South America, the Middle East, and Europe.
What Should Buyers Consider for Future Sourcing?
As the demand for high-quality lifting and rigging solutions continues to grow, it is essential for buyers to stay ahead of market trends and technological advancements. Engaging with manufacturers that prioritize safety standards and offer comprehensive training and support will enhance operational efficiency and reduce risks associated with rigging failures.
How Can You Take Action Today?
Now is the time for B2B buyers to reassess their sourcing strategies and establish partnerships with leading shackle manufacturers. By doing so, you can ensure that your operations are not only efficient but also equipped with the best tools to drive success in your industry. Take the first step towards a more strategic sourcing approach and secure your supply chain for the future.