Unlock Savings: The Ultimate Mini Truck Custom Guide (2025)
Introduction: Navigating the Global Market for mini truck custom
In the competitive landscape of international commerce, sourcing mini truck custom solutions presents a unique challenge for B2B buyers across diverse markets, including Africa, South America, the Middle East, and Europe. The demand for versatile, durable, and tailored mini trucks has surged, driven by their applications in logistics, agriculture, and urban transport. However, navigating the complexities of supplier selection, customization options, and cost structures can be daunting.
This guide offers a comprehensive overview of the mini truck custom market, addressing key aspects such as types of mini trucks available, their various applications, and essential criteria for supplier vetting. Additionally, we delve into pricing strategies and the latest trends shaping the industry. By equipping international B2B buyers with actionable insights and practical tools, this guide empowers them to make informed purchasing decisions that align with their operational needs and budget constraints.
For buyers from regions like Saudi Arabia and Poland, understanding regional market dynamics and compliance requirements is crucial. This guide not only streamlines the sourcing process but also enhances the buyer’s ability to identify reliable suppliers who can deliver high-quality, customized mini truck solutions tailored to their specific business requirements.
Understanding mini truck custom Types and Variations
Type Name | Key Distinguishing Features | Primary B2B Applications | Brief Pros & Cons for Buyers |
---|---|---|---|
Standard Mini Truck | Compact size, versatile cargo space | Delivery, small-scale logistics | Pros: Cost-effective, easy to maneuver. Cons: Limited payload capacity. |
Dump Mini Truck | Equipped with hydraulic lift for unloading | Construction, landscaping | Pros: Efficient for bulk materials. Cons: Higher maintenance costs. |
Refrigerated Mini Truck | Insulated cargo area for temperature-sensitive goods | Food transport, pharmaceuticals | Pros: Preserves product quality. Cons: Higher initial investment. |
Flatbed Mini Truck | Open cargo area, customizable attachments | Freight transport, equipment hauling | Pros: Flexible loading options. Cons: Exposed cargo may require securing. |
Electric Mini Truck | Battery-powered, eco-friendly design | Urban deliveries, eco-conscious businesses | Pros: Lower operating costs, sustainable. Cons: Limited range and charging infrastructure. |
What Are the Characteristics of Standard Mini Trucks?
Standard mini trucks are characterized by their compact size and versatile cargo space, making them ideal for urban environments. They often have a payload capacity ranging from 500 to 1,500 kg, which suits small-scale logistics and delivery services. For B2B buyers, the key consideration is balancing cost-effectiveness with operational needs, as these vehicles are generally more affordable and easier to maneuver than larger trucks.
How Do Dump Mini Trucks Function in B2B Applications?
Dump mini trucks are equipped with hydraulic lifts that facilitate the unloading of bulk materials, making them essential in construction and landscaping industries. Their ability to handle heavy loads efficiently allows businesses to streamline operations. However, buyers should be aware of the higher maintenance costs associated with hydraulic systems, which can impact long-term budgeting.
Why Choose Refrigerated Mini Trucks for Transporting Goods?
Refrigerated mini trucks feature insulated cargo areas designed to transport temperature-sensitive goods, such as food products and pharmaceuticals. These vehicles ensure that products remain at required temperatures during transit, which is crucial for quality assurance. B2B buyers must consider the higher initial investment and ongoing operational costs, but the benefits of product preservation often justify these expenses.
What Advantages Do Flatbed Mini Trucks Offer?
Flatbed mini trucks provide an open cargo area that allows for customizable attachments, making them versatile for various freight transport and equipment hauling needs. Their design facilitates easy loading and unloading of goods, which is particularly advantageous for businesses requiring flexibility in cargo management. Buyers should consider the need for securing exposed cargo, as this can add complexity to transport operations.
How Do Electric Mini Trucks Stand Out in the Market?
Electric mini trucks are gaining popularity due to their eco-friendly design and lower operating costs compared to traditional fuel-powered vehicles. They are particularly suitable for urban deliveries and companies looking to enhance their sustainability efforts. However, potential buyers should evaluate the limited range and charging infrastructure, as these factors can affect operational efficiency, especially in regions with less developed electric vehicle support.
Related Video: Custom Lowered Ford Maverick, Return Of The Mini Truck.
Key Industrial Applications of mini truck custom
Industry/Sector | Specific Application of mini truck custom | Value/Benefit for the Business | Key Sourcing Considerations for this Application |
---|---|---|---|
Agriculture | Transporting produce and equipment | Enhances efficiency in logistics and reduces spoilage | Durability, load capacity, and suitability for rough terrains |
Construction | On-site material transport and waste removal | Improves site operations and minimizes downtime | Customization options for cargo space and towing capabilities |
Retail and E-commerce | Last-mile delivery of goods | Increases customer satisfaction through timely deliveries | Fuel efficiency, vehicle size, and adaptability to urban areas |
Mining and Resources | Hauling materials and equipment | Streamlines operations and reduces transport costs | Off-road capability, payload capacity, and maintenance support |
Waste Management | Collection and transport of waste materials | Supports sustainability efforts and compliance with regulations | Customization for waste types, loading mechanisms, and vehicle size |
How Are Mini Truck Customs Used in Agriculture?
In the agricultural sector, mini truck customs are primarily used for transporting produce from farms to markets, as well as moving equipment and supplies. These vehicles help mitigate spoilage by enabling quick and efficient logistics, essential for perishable goods. International buyers from regions like Africa and South America should consider durability and load capacity, as many farms operate in rough terrains. Customization for temperature control or specialized cargo areas can further enhance their functionality.
What Role Do Mini Truck Customs Play in Construction?
In construction, mini truck customs serve a vital role in transporting materials and removing waste from job sites. Their compact size allows them to navigate tight spaces, making them ideal for urban construction projects. This efficiency reduces downtime and improves overall productivity. Buyers, especially from Europe and the Middle East, should focus on customization options that enhance cargo space and towing capabilities to meet specific site requirements.
How Are Mini Truck Customs Transforming Retail and E-commerce?
For retail and e-commerce businesses, mini truck customs are crucial for last-mile delivery. They enable businesses to provide timely deliveries, enhancing customer satisfaction and loyalty. The compact design is particularly beneficial in urban areas where larger vehicles may struggle. B2B buyers should prioritize fuel efficiency and adaptability to urban settings when sourcing these vehicles, ensuring they can meet the demands of their delivery schedules.
What Advantages Do Mini Truck Customs Offer in Mining and Resources?
In the mining and resources sector, mini truck customs are utilized for hauling materials and transporting equipment to and from sites. Their ability to operate in challenging environments can significantly streamline operations and reduce transport costs. Buyers from regions with active mining industries, such as South America and parts of Africa, should consider off-road capabilities and payload capacity to ensure these vehicles meet operational demands.
How Do Mini Truck Customs Contribute to Waste Management?
Mini truck customs are increasingly used in waste management for the collection and transport of various waste materials. Their adaptability allows for specialized configurations that cater to different waste types, supporting sustainability efforts and compliance with local regulations. B2B buyers should evaluate customization options for loading mechanisms and vehicle sizes, particularly in densely populated areas where waste collection efficiency is crucial.
Related Video: Sci6 Q3 – Characteristics and Uses of Simple Machines
3 Common User Pain Points for ‘mini truck custom’ & Their Solutions
Scenario 1: Difficulty in Sourcing Reliable Mini Truck Custom Suppliers
The Problem: Many B2B buyers from regions such as Africa and South America often struggle to find trustworthy suppliers for mini truck custom services. Issues such as language barriers, lack of transparent communication, and differing regulatory standards can create significant challenges. Buyers may receive inconsistent quality, delayed deliveries, or inadequate customer support, leading to frustration and potential financial losses.
The Solution: To effectively source reliable suppliers, buyers should leverage B2B marketplaces that cater specifically to their regions, such as Alibaba or TradeIndia, which feature verified suppliers with customer reviews. It’s crucial to conduct thorough due diligence, including requesting samples, engaging in detailed discussions about specifications, and verifying business licenses. Establishing clear communication channels and setting expectations around timelines and quality standards can mitigate risks. Additionally, consider forming partnerships with local agents who understand the market landscape and can facilitate smoother transactions.
Scenario 2: Customization Challenges Leading to Operational Inefficiencies
The Problem: Customizing mini trucks to meet specific operational needs can become a daunting task for B2B buyers. For instance, buyers may require unique configurations for cargo space or specialized equipment that isn’t readily available. This can lead to operational inefficiencies, as trucks may not perform optimally for their intended purposes, resulting in higher costs and reduced productivity.
The Solution: To tackle customization challenges, buyers should engage with suppliers who offer comprehensive customization options and have experience in the industry. Providing detailed specifications upfront—such as load capacities, dimensions, and required features—ensures that the customization aligns with operational needs. Collaborating closely with the supplier during the design phase can help identify potential issues early on. Consider implementing a pilot program with a limited number of customized trucks to evaluate their performance before committing to larger orders.
Scenario 3: Navigating Import Regulations and Compliance for Mini Trucks
The Problem: International buyers, especially from the Middle East and Europe, often face complex import regulations and compliance issues when bringing mini trucks into their countries. Misunderstanding these regulations can lead to costly delays, fines, or even the rejection of shipments at customs. This administrative burden can deter businesses from pursuing necessary upgrades to their fleets.
The Solution: To navigate import regulations effectively, B2B buyers should invest in understanding the specific legal requirements of their target markets. This can include consulting with import/export specialists or local legal experts who can provide guidance on tariffs, safety standards, and documentation. Utilizing resources such as government trade websites or chambers of commerce can also offer valuable insights into compliance. Establishing strong relationships with logistics partners who are experienced in handling customs can streamline the import process, ensuring that all paperwork is in order and minimizing the risk of delays.
Strategic Material Selection Guide for mini truck custom
What Are the Key Properties of Steel for Mini Truck Custom Applications?
Steel is a predominant choice for mini truck custom applications due to its excellent strength-to-weight ratio and versatility. It typically offers high tensile strength, making it suitable for load-bearing components. Steel exhibits good temperature resistance, withstanding high pressures and impacts, which is crucial for the durability of mini trucks in various operating conditions.
Pros and Cons of Using Steel
The primary advantage of steel is its durability and ability to be easily welded, which simplifies manufacturing processes. However, steel is susceptible to corrosion if not properly treated, necessitating additional coatings or treatments that can increase costs. For international buyers, compliance with standards such as ASTM A36 or EN 10025 is essential, particularly in regions like Europe and the Middle East, where quality assurance is critical.
How Does Aluminum Compare as a Material for Mini Truck Customization?
Aluminum is increasingly favored for mini truck customization due to its lightweight nature and resistance to corrosion. It has a lower density than steel, which can enhance fuel efficiency and payload capacity. Aluminum also has good thermal conductivity, which can be beneficial in applications requiring heat dissipation.
Pros and Cons of Using Aluminum
The main advantage of aluminum is its resistance to rust, making it ideal for trucks operating in humid or coastal environments. However, it is generally less strong than steel, which may limit its use in high-stress applications. International buyers should consider compliance with standards such as ASTM B221 for extruded aluminum products, particularly in regions like South America and Africa, where local regulations may vary.
What Are the Benefits of Using Composite Materials in Mini Truck Customization?
Composite materials, such as fiberglass and carbon fiber, offer unique advantages for mini truck customization. These materials are known for their high strength-to-weight ratios and excellent corrosion resistance, making them suitable for various truck components, including body panels and interior fittings.
Pros and Cons of Using Composites
The primary benefit of composites is their lightweight nature, which can significantly reduce the overall weight of the truck, improving fuel efficiency. However, composites can be more expensive than traditional materials and may require specialized manufacturing processes, which could complicate production. For international buyers, understanding the specific standards for composites, such as ISO 9001 for quality management, is crucial, especially in regions like Europe where compliance is strictly monitored.
What Role Does Plastic Play in Mini Truck Custom Applications?
Plastics are often used in mini truck customization for non-structural components such as dashboards, interior fittings, and exterior trim. They are lightweight and can be molded into complex shapes, allowing for innovative designs and features.
Pros and Cons of Using Plastics
The key advantage of plastics is their versatility and low cost, making them an attractive option for various applications. However, plastics may not offer the same level of durability or heat resistance as metals, which could limit their use in high-stress environments. International buyers should be aware of the specific plastic grades and their compliance with standards such as ASTM D638 for tensile properties, particularly in markets like Africa and the Middle East where quality can vary.
Summary Table of Material Selection for Mini Truck Custom
Material | Typical Use Case for mini truck custom | Key Advantage | Key Disadvantage/Limitation | Relative Cost (Low/Med/High) |
---|---|---|---|---|
Steel | Frame and structural components | High strength and durability | Susceptible to corrosion | Medium |
Aluminum | Body panels and structural elements | Lightweight and corrosion-resistant | Lower strength compared to steel | High |
Composite | Body panels and interior fittings | High strength-to-weight ratio | Higher cost and complex manufacturing | High |
Plastic | Interior fittings and trim | Versatile and low cost | Limited durability and heat resistance | Low |
This comprehensive analysis of materials provides international B2B buyers with actionable insights into the advantages and limitations of each option, helping them make informed decisions tailored to their specific market needs.
In-depth Look: Manufacturing Processes and Quality Assurance for mini truck custom
What Are the Key Manufacturing Processes for Mini Truck Customization?
The manufacturing process for mini truck customization involves several critical stages that ensure the vehicle meets specific requirements tailored to the needs of B2B buyers. Understanding these stages not only helps in assessing potential suppliers but also ensures that the final product aligns with quality and performance expectations.
1. Material Preparation: What Materials Are Commonly Used?
The first step in the manufacturing process is material preparation. This phase includes selecting high-quality raw materials such as steel, aluminum, and composites that are vital for the structural integrity and performance of the mini truck.
- Steel and Aluminum: Often used for the chassis and body, these materials provide strength while keeping the overall weight low.
- Composites: Increasingly used in body panels for their lightweight and durability properties.
- Quality Assurance: Suppliers should provide material certifications to validate the quality and compliance with international standards.
How Are Mini Trucks Formed During Manufacturing?
The forming process is where raw materials are shaped into components that will make up the mini truck. This stage typically involves:
- Stamping: Used to create body panels from sheets of metal.
- Bending and Welding: Essential for creating the truck’s frame and structural components.
- CNC Machining: Provides precision for critical components, enhancing the overall fit and finish of the vehicle.
Each of these techniques must adhere to strict tolerances to ensure that all parts fit together seamlessly during assembly.
What Steps Are Involved in the Assembly of Mini Trucks?
Assembly is a crucial stage where all the pre-formed components come together. This process usually includes:
- Sub-Assembly: Components such as the engine, transmission, and suspension are assembled separately before being integrated into the main chassis.
- Final Assembly: All sub-assemblies are brought together, and systems like electrical, hydraulic, and braking are installed.
- Quality Checks: Each assembly stage should have its own quality checkpoints to catch any defects early.
How Is Finishing Done in Mini Truck Manufacturing?
Finishing processes enhance both aesthetics and durability. Common finishing techniques include:
- Painting and Coating: Protects against rust and enhances appearance. Suppliers should use environmentally friendly paints to comply with international regulations.
- Quality Inspection: Post-finishing, a thorough inspection is conducted to ensure that the finish is uniform and free of defects.
What International Standards Should B2B Buyers Be Aware Of for Quality Assurance?
Quality assurance is paramount in manufacturing, especially for international buyers. Here are some relevant standards:
- ISO 9001: This standard outlines requirements for a quality management system (QMS) that organizations must meet to consistently provide products that meet customer and regulatory requirements.
- CE Marking: Common in Europe, this certification indicates compliance with health, safety, and environmental protection standards.
- API Standards: Particularly relevant for mini trucks designed for oil and gas applications, ensuring that the products meet industry-specific requirements.
What Are the Key Quality Control Checkpoints in Mini Truck Manufacturing?
Quality control (QC) involves several checkpoints throughout the manufacturing process to ensure compliance and performance:
- Incoming Quality Control (IQC): Materials are inspected upon arrival at the manufacturing facility to ensure they meet specifications.
- In-Process Quality Control (IPQC): During the manufacturing process, random inspections are performed to catch defects early.
- Final Quality Control (FQC): A comprehensive inspection occurs before the mini truck is shipped to verify that it meets all specifications and quality standards.
What Common Testing Methods Are Used in Mini Truck Manufacturing?
Testing is critical to ensure that the mini trucks perform as expected under various conditions. Common methods include:
- Dynamic Testing: Assessing the vehicle’s performance under simulated driving conditions.
- Load Testing: Ensuring that the truck can handle its specified load without structural failure.
- Safety Testing: Evaluating features such as braking systems and crashworthiness to meet regulatory requirements.
How Can B2B Buyers Verify Supplier Quality Control?
B2B buyers should take proactive steps to verify the quality control practices of potential suppliers. Here are some methods:
- Supplier Audits: Conducting on-site audits allows buyers to assess the manufacturing processes and quality control measures in place.
- Requesting Quality Reports: Suppliers should provide detailed quality assurance reports, including results from IQC, IPQC, and FQC.
- Third-Party Inspections: Engaging independent inspection agencies can provide an unbiased assessment of the supplier’s manufacturing capabilities and adherence to standards.
What Are the Nuances of Quality Control for International B2B Buyers?
For international buyers, understanding the nuances of quality control is essential:
- Cultural Differences: Different regions may have varying standards for quality and testing. It’s crucial to align expectations early in negotiations.
- Regulatory Compliance: Ensure that suppliers are familiar with the regulatory requirements of the buyer’s country, especially when importing vehicles.
- Documentation: Maintain comprehensive documentation of all quality standards, certifications, and testing results to facilitate smooth customs clearance and compliance checks.
Conclusion: How Can B2B Buyers Ensure Quality in Mini Truck Custom Manufacturing?
By understanding the manufacturing processes and quality assurance measures in place, international B2B buyers can make informed decisions when selecting suppliers for mini truck customization. Emphasizing quality standards, conducting regular audits, and verifying testing methods will ensure that the final product meets both performance and compliance expectations, ultimately leading to a successful partnership.
Practical Sourcing Guide: A Step-by-Step Checklist for ‘mini truck custom’
To effectively source custom mini trucks for your business, it’s essential to follow a structured approach. This checklist will guide you through the critical steps necessary to ensure you make informed decisions and secure the best suppliers for your specific needs.
Step 1: Define Your Technical Specifications
Start by clearly outlining the specifications required for your mini trucks. This includes factors such as size, load capacity, engine type, and any custom features you might need. Having detailed specifications helps suppliers understand your requirements, ensuring that you receive accurate quotes and suitable options.
- Consider local regulations: Make sure your specifications align with the legal requirements in your region, such as emissions standards or safety features.
- Anticipate future needs: Think about potential growth or changes in your operations that might require different specifications.
Step 2: Conduct Market Research for Suppliers
Research potential suppliers who specialize in custom mini trucks. Look for manufacturers that have a solid reputation in the market and can cater to your specific geographical needs, especially if you are sourcing from Africa, South America, the Middle East, or Europe.
- Utilize B2B platforms: Websites like Alibaba or local trade directories can help you identify reputable suppliers.
- Check reviews and testimonials: Look for feedback from other businesses to gauge supplier reliability and product quality.
Step 3: Evaluate Potential Suppliers
Before committing, it’s crucial to vet suppliers thoroughly. Request company profiles, case studies, and references from buyers in a similar industry or region. Don’t just rely on their website.
- Assess their production capabilities: Understand their manufacturing processes and capacity to meet your order volume.
- Verify their quality control measures: Ensure they have robust systems in place to maintain product quality.
Step 4: Request Quotes and Compare Pricing
Once you have shortlisted potential suppliers, request detailed quotes. Ensure that you ask for breakdowns of costs, including shipping, taxes, and any potential additional fees.
- Compare not just prices: Look at the value offered, including warranty, after-sales service, and delivery times.
- Negotiate terms: Don’t hesitate to discuss pricing or terms of service to find a mutually beneficial arrangement.
Step 5: Check Certifications and Compliance
Ensure that the suppliers you are considering have the necessary certifications and comply with international standards relevant to mini trucks. This is particularly important for ensuring safety and environmental compliance.
- Look for ISO certifications: These can indicate a commitment to quality management standards.
- Verify local compliance: Ensure they meet the regulations specific to your country or region, which can affect the import and use of the vehicles.
Step 6: Request Samples or Prototypes
Before making a large order, request samples or prototypes of the mini trucks. This allows you to assess the quality, functionality, and suitability of the trucks for your operations.
- Conduct tests: Evaluate the trucks under real operating conditions to ensure they meet your expectations.
- Gather feedback: Involve your team in the evaluation process to get insights from various perspectives.
Step 7: Finalize the Contract and Payment Terms
Once you have chosen a supplier, finalize the contract detailing all agreed terms, including delivery schedules, payment terms, and conditions for warranties or returns.
- Ensure clarity: Make sure all terms are clearly defined to avoid misunderstandings later.
- Consider using escrow services: This can help protect both parties during the payment process, ensuring funds are released only when the agreed conditions are met.
By following this checklist, you can streamline your sourcing process for custom mini trucks, ensuring you choose the best suppliers that meet your specific business needs.
Comprehensive Cost and Pricing Analysis for mini truck custom Sourcing
What Are the Key Cost Components for Mini Truck Custom Sourcing?
When sourcing mini trucks, understanding the cost structure is crucial for B2B buyers. The primary cost components include:
-
Materials: This encompasses the raw materials used in the manufacturing of mini trucks, such as steel, plastic, and electronic components. The quality and source of these materials can significantly impact the overall cost.
-
Labor: Labor costs vary by region and can affect the pricing structure. Skilled labor in regions like Europe may command higher wages compared to labor in Africa or South America, influencing the final price.
-
Manufacturing Overhead: This includes indirect costs related to production, such as utilities, rent, and equipment maintenance. Efficient manufacturing processes can lower overhead costs, benefiting buyers.
-
Tooling: Custom tooling is often necessary for specific modifications or designs in mini trucks. The initial investment in tooling can be substantial but is essential for high-quality customization.
-
Quality Control (QC): Implementing rigorous QC processes ensures that the mini trucks meet safety and performance standards. Investing in quality control can lead to higher upfront costs but ultimately saves money by reducing defects and warranty claims.
-
Logistics: Transportation costs must be factored in when sourcing internationally. Shipping methods, distance, and tariffs can significantly influence the total cost.
-
Margin: Suppliers typically add a profit margin on top of their costs. Understanding the typical margins in the industry can help buyers negotiate better deals.
How Do Price Influencers Affect Mini Truck Customization Costs?
Several factors influence the pricing of custom mini trucks:
-
Volume and Minimum Order Quantity (MOQ): Bulk orders often lead to lower per-unit costs. Buyers should evaluate their needs and consider negotiating for better pricing based on order size.
-
Specifications and Customization: The level of customization required affects the cost. More complex specifications often result in higher prices due to increased labor and material requirements.
-
Materials Quality and Certifications: Higher quality materials and compliance with international standards (e.g., ISO certifications) can increase costs but are essential for ensuring product reliability and market acceptance.
-
Supplier Factors: Reputation, reliability, and the financial stability of suppliers can influence pricing. Established suppliers may charge more due to their proven track record.
-
Incoterms: The choice of Incoterms affects logistics costs and responsibilities. Understanding the implications of terms like FOB (Free On Board) or CIF (Cost, Insurance, and Freight) is vital for accurate cost projections.
What Are Effective Buyer Tips for Mini Truck Custom Sourcing?
For international B2B buyers, especially from Africa, South America, the Middle East, and Europe, the following tips can enhance sourcing efficiency:
-
Negotiate Wisely: Approach negotiations with a clear understanding of costs and market rates. Leverage volume discounts and long-term partnerships to secure favorable terms.
-
Consider Total Cost of Ownership (TCO): Look beyond the initial purchase price. Evaluate maintenance, operational costs, and resale value to determine the true cost of ownership.
-
Understand Pricing Nuances: Be aware of regional pricing variations. For example, buyers in Saudi Arabia may encounter different pricing structures compared to those in Poland due to local market dynamics.
-
Build Relationships with Suppliers: Developing strong relationships can lead to better pricing and more favorable terms. Trust and reliability are key in long-term partnerships.
-
Stay Informed on Market Trends: Keeping abreast of industry trends, material costs, and supplier capabilities can provide leverage in negotiations and sourcing decisions.
Disclaimer on Indicative Prices
Prices for custom mini trucks can vary widely based on specifications, order size, and supplier agreements. Buyers should consider these factors and conduct thorough research to obtain accurate pricing. Always request detailed quotes to understand the breakdown of costs involved.
Alternatives Analysis: Comparing mini truck custom With Other Solutions
Understanding the Alternatives to Mini Truck Custom Solutions
In the international B2B landscape, particularly among buyers from Africa, South America, the Middle East, and Europe, selecting the right transportation solution is crucial. While mini truck customs have gained popularity for their versatility and cost-effectiveness, it’s essential to explore alternative options that may better suit specific business needs. This analysis will compare mini truck customs with two viable alternatives: electric cargo bikes and small delivery vans.
Comparison Table of Mini Truck Custom and Alternatives
Comparison Aspect | Mini Truck Custom | Electric Cargo Bike | Small Delivery Van |
---|---|---|---|
Performance | High load capacity, versatile for urban and rural use | Moderate load capacity, ideal for short distances | High load capacity, suitable for longer distances |
Cost | Moderate initial investment; low operational costs | Low initial investment; minimal operating costs | High initial investment; higher fuel/maintenance costs |
Ease of Implementation | Requires adaptation for specific use cases | Quick setup; minimal training needed | Longer setup; requires fleet management |
Maintenance | Moderate; parts can be sourced locally | Low; fewer mechanical parts | Moderate; regular maintenance required |
Best Use Case | Diverse applications including delivery and construction | Urban deliveries, eco-friendly businesses | Long-distance transport, larger cargo needs |
Analyzing Electric Cargo Bikes: Are They a Sustainable Alternative?
Electric cargo bikes present a compelling alternative for businesses focused on sustainable practices. These bikes are designed for urban environments and can easily navigate through traffic, reducing delivery times. Their lower initial investment and minimal operating costs make them financially attractive, especially for small to medium-sized businesses. However, their load capacity limits may restrict their use in larger deliveries, making them less suitable for industries requiring heavy lifting.
Evaluating Small Delivery Vans: When to Choose This Option?
Small delivery vans are another alternative that offers high load capacity and the ability to transport goods over longer distances. They are ideal for businesses that require consistent deliveries across urban and suburban areas. While the initial investment is significantly higher, the versatility and reliability of vans can justify the cost for larger businesses or those with extensive logistics needs. However, businesses must consider higher fuel and maintenance costs, which can impact long-term profitability.
Conclusion: How to Choose the Right Transportation Solution?
When selecting a transportation solution, B2B buyers must consider their specific operational needs, budget constraints, and sustainability goals. Mini truck customs offer a balance of performance and cost-effectiveness, making them suitable for diverse applications. However, for businesses prioritizing eco-friendliness or requiring higher load capacities for long-distance transport, electric cargo bikes or small delivery vans may be more appropriate. Conducting a thorough analysis of the operational requirements and potential return on investment will help buyers make informed decisions tailored to their unique circumstances.

A stock image related to mini truck custom.
Essential Technical Properties and Trade Terminology for mini truck custom
What Are the Essential Technical Properties of Mini Truck Custom?
Understanding the technical properties of mini trucks is crucial for international B2B buyers, especially those sourcing from diverse regions such as Africa, South America, the Middle East, and Europe. Here are some critical specifications to consider:
-
Material Grade
The material grade of the mini truck components—such as steel, aluminum, or composites—affects durability, weight, and cost. Higher-grade materials often enhance the truck’s lifespan and performance, which is vital for buyers looking to invest in reliable transportation solutions. -
Weight Capacity
Each mini truck has a specified weight capacity, indicating how much load it can carry without compromising safety or performance. Understanding this specification helps buyers ensure that the vehicle meets their logistics needs, especially in industries like construction and delivery. -
Engine Power and Efficiency
The engine specifications, including horsepower and fuel efficiency, are essential for operational costs and performance. Buyers should evaluate engine types, such as diesel or electric, based on their intended use and environmental regulations in their region. -
Dimensions and Maneuverability
The overall dimensions of the mini truck, including length, width, and height, impact its ability to navigate urban environments or tight spaces. This is particularly important for buyers in densely populated areas where maneuverability is critical. -
Tolerance Levels
Tolerance refers to the allowable variation in dimensions and materials during manufacturing. Understanding tolerance levels is essential for ensuring that components fit together correctly and function as intended, thus minimizing maintenance costs over time. -
Safety Features
Modern mini trucks often include safety features such as anti-lock braking systems (ABS), traction control, and stability management. Buyers should prioritize these features to enhance driver and cargo safety, complying with local regulations.
Which Trade Terms Should B2B Buyers Understand When Sourcing Mini Truck Customs?
Navigating the terminology associated with mini truck customs can significantly streamline the procurement process. Here are some common terms:
-
OEM (Original Equipment Manufacturer)
This term refers to companies that produce parts or equipment that may be marketed by another manufacturer. Understanding OEM relationships can help buyers identify quality sources for replacement parts or custom modifications. -
MOQ (Minimum Order Quantity)
MOQ indicates the smallest number of units a supplier is willing to sell. Buyers need to be aware of MOQs to assess their purchasing power and ensure they can meet the supplier’s requirements without overcommitting resources. -
RFQ (Request for Quotation)
An RFQ is a document sent to suppliers to solicit price quotes for specific products or services. This is a critical step in the procurement process, allowing buyers to compare costs and make informed decisions. -
Incoterms (International Commercial Terms)
Incoterms are internationally recognized rules that define the responsibilities of buyers and sellers in the shipping process. Familiarity with these terms helps buyers understand shipping costs, liability, and delivery timelines. -
Lead Time
Lead time refers to the period from placing an order to its delivery. Knowing the lead time is essential for buyers to plan their operations and inventory management effectively. -
Customization
This term refers to modifying a mini truck according to specific buyer requirements, such as adding features or changing specifications. Understanding customization options can help buyers tailor vehicles to their operational needs.
By familiarizing themselves with these technical properties and trade terms, B2B buyers can make informed decisions that align with their business objectives and operational requirements in sourcing mini truck customs.
Navigating Market Dynamics and Sourcing Trends in the mini truck custom Sector
What Are the Current Market Dynamics and Key Trends in the Mini Truck Custom Sector?
The mini truck custom sector is experiencing notable growth driven by urbanization, rising logistics demands, and a shift towards more sustainable transport solutions. International B2B buyers from Africa, South America, the Middle East, and Europe are increasingly looking for customized mini trucks that offer flexibility in urban environments where space is limited. In regions such as Saudi Arabia and Poland, the demand for mini trucks is further fueled by government initiatives aimed at boosting local manufacturing and reducing reliance on imports.
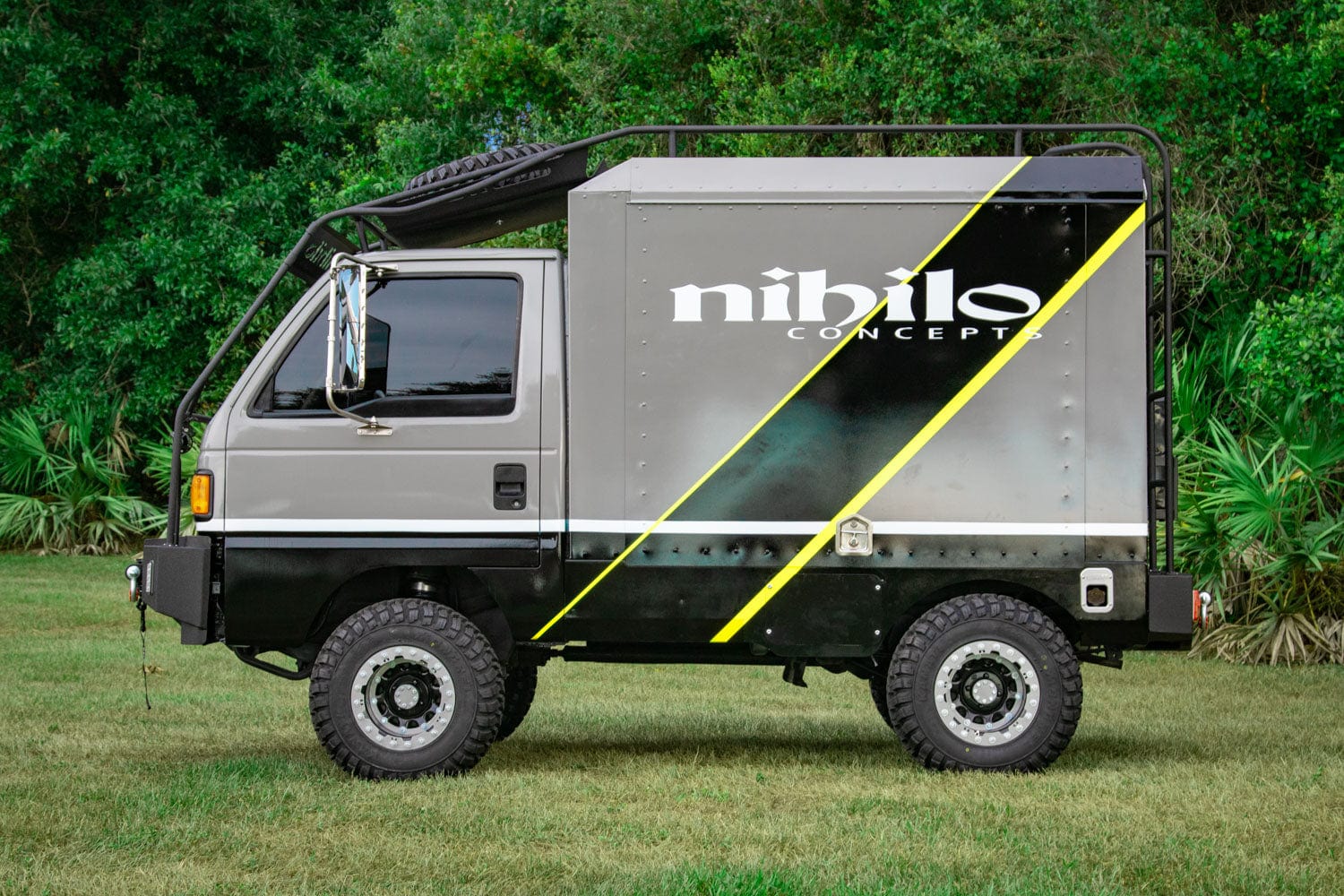
A stock image related to mini truck custom.
Emerging B2B technologies, such as telematics and IoT, are transforming how mini trucks are sourced and utilized. These innovations enable fleet management solutions that enhance operational efficiency, reduce costs, and improve route optimization. Buyers are also leveraging e-commerce platforms to access a wider array of suppliers, allowing for more competitive pricing and customization options. As a result, understanding local market dynamics and adapting sourcing strategies to meet specific regional needs is crucial for international buyers.
How Can Sustainability and Ethical Sourcing Impact the Mini Truck Custom Sector?
Sustainability is becoming a critical consideration in the mini truck custom sector, especially as global awareness of environmental impacts increases. International B2B buyers are prioritizing suppliers that adhere to ethical sourcing practices and utilize eco-friendly materials. This shift is not only driven by consumer demand but also by regulatory pressures in various regions, including Europe and parts of the Middle East.
Buyers should look for suppliers that possess ‘green’ certifications, such as ISO 14001 for environmental management or LEED certification for sustainable manufacturing practices. Using alternative materials, like recycled metals and bio-based composites, can significantly reduce the carbon footprint of mini truck customizations. Moreover, implementing sustainable practices in the supply chain enhances brand reputation and can lead to cost savings in the long run, making it an attractive proposition for B2B buyers.
What Is the Brief Evolution and History of the Mini Truck Custom Sector?
The mini truck custom sector has evolved significantly over the past few decades. Initially, mini trucks were primarily used for agricultural purposes and small-scale transportation. However, with the rise of urbanization and changing consumer needs, these vehicles have transitioned into versatile assets for businesses across various industries, including logistics, retail, and construction.
As customization options expanded, manufacturers began offering tailored solutions, allowing businesses to modify mini trucks for specific operational requirements. This evolution has been marked by technological advancements, enabling features such as fuel efficiency, enhanced payload capacities, and connectivity options. Today, the mini truck custom sector stands at the intersection of practicality and innovation, offering significant opportunities for B2B buyers seeking adaptable solutions for their transportation needs.
Frequently Asked Questions (FAQs) for B2B Buyers of mini truck custom
-
How do I solve issues with sourcing mini truck custom suppliers?
To effectively solve sourcing issues, start by conducting thorough market research to identify potential suppliers in regions known for mini truck manufacturing. Utilize platforms like Alibaba or industry-specific trade shows to connect with verified suppliers. Additionally, consider using trade organizations or chambers of commerce in your target regions to get recommendations. Ensure to check supplier credentials, certifications, and reviews from other businesses to mitigate risks. -
What is the best approach to customize mini trucks for different markets?
The best approach to customization involves understanding the specific needs of your target market. Conduct surveys or focus groups to gather insights on local preferences, regulations, and operational requirements. Collaborate with suppliers who offer flexible customization options, including size, engine type, and features tailored to regional demands. It’s also essential to comply with local regulations regarding vehicle modifications to ensure market acceptance. -
What are the minimum order quantities (MOQs) for custom mini trucks?
Minimum order quantities (MOQs) for custom mini trucks can vary significantly depending on the supplier and the complexity of the customization. Generally, MOQs range from 5 to 50 units. Discuss your specific needs with potential suppliers to negotiate favorable terms, especially if you’re entering a new market or testing a product line. Some suppliers may offer lower MOQs for initial orders or prototypes. -
What payment terms should I expect when sourcing mini trucks internationally?
Payment terms when sourcing mini trucks can vary, but common practices include a 30% upfront deposit and the remaining balance upon delivery or prior to shipping. Some suppliers may offer letters of credit for larger orders, providing added security for both parties. Always clarify payment methods accepted (e.g., bank transfer, PayPal) and consider escrow services for additional protection in international transactions. -
How can I ensure quality assurance (QA) for custom mini trucks?
To ensure quality assurance, establish clear specifications and standards with your supplier before production begins. Implement a multi-stage inspection process, including pre-production samples, in-process quality checks, and final inspections. Consider hiring third-party inspection services to conduct independent quality checks. Additionally, request certifications for materials used and compliance with international safety standards. -
What logistics challenges should I be aware of when importing mini trucks?
Logistics challenges when importing mini trucks may include customs clearance, shipping delays, and compliance with local regulations. Ensure you are familiar with the import duties and taxes applicable in your country. Partnering with a reliable freight forwarder can help navigate these complexities. Also, prepare all necessary documentation, including bills of lading, invoices, and certificates of origin, to facilitate smooth customs processing. -
How do I evaluate the reliability of a mini truck custom supplier?
To evaluate a supplier’s reliability, start by checking their business history, customer reviews, and industry reputation. Request references from previous clients and verify their experience with similar projects. Conduct site visits if possible, or utilize virtual tours to assess their facilities and production capabilities. Certifications from recognized industry bodies can also indicate a supplier’s commitment to quality and reliability. -
What are the key considerations for after-sales support in mini truck custom orders?
When sourcing custom mini trucks, consider the supplier’s after-sales support, including warranty terms, maintenance services, and parts availability. Establish clear communication channels for addressing any issues post-purchase. Inquire about training programs for your team on vehicle operation and maintenance. A supplier that offers robust after-sales support will enhance your business operations and customer satisfaction in the long run.
Important Disclaimer & Terms of Use
⚠️ Important Disclaimer
The information provided in this guide, including content regarding manufacturers, technical specifications, and market analysis, is for informational and educational purposes only. It does not constitute professional procurement advice, financial advice, or legal advice.
While we have made every effort to ensure the accuracy and timeliness of the information, we are not responsible for any errors, omissions, or outdated information. Market conditions, company details, and technical standards are subject to change.
B2B buyers must conduct their own independent and thorough due diligence before making any purchasing decisions. This includes contacting suppliers directly, verifying certifications, requesting samples, and seeking professional consultation. The risk of relying on any information in this guide is borne solely by the reader.
Strategic Sourcing Conclusion and Outlook for mini truck custom
In summary, effective strategic sourcing for mini truck customization is crucial for international B2B buyers aiming to optimize their operations and enhance profitability. By prioritizing supplier relationships, leveraging technology for efficient procurement processes, and understanding regional market dynamics, businesses can secure high-quality products that meet their specific needs.
How Can Strategic Sourcing Enhance Your Business Operations?
The value of strategic sourcing lies not only in cost savings but also in fostering innovation and quality improvements. Buyers from Africa, South America, the Middle East, and Europe should focus on aligning their sourcing strategies with local market requirements while maintaining flexibility to adapt to global trends. Engaging with reliable suppliers and utilizing data analytics can lead to informed decision-making, ultimately driving operational excellence.
What’s Next for International Buyers in the Mini Truck Market?
Looking ahead, the mini truck customization market presents significant opportunities. As demand for versatile and efficient transportation solutions continues to rise, now is the time to act. International B2B buyers should actively seek partnerships with manufacturers who can deliver tailored solutions that cater to specific operational needs. Embrace this moment to enhance your supply chain resilience and secure your competitive edge in the evolving global marketplace.