Unlock Savings: The Ultimate Power Station Manufacturer Guide (2025)
Introduction: Navigating the Global Market for power station manufacturer
As the demand for sustainable energy solutions surges globally, navigating the complexities of sourcing power station manufacturers has become a pivotal challenge for international B2B buyers. Whether you’re a buyer from Africa, South America, the Middle East, or Europe, understanding the diverse landscape of power station technologies—ranging from renewable energy systems to traditional fossil fuel plants—is crucial for making informed decisions. This comprehensive guide not only covers the various types of power stations available but also delves into their applications, supplier vetting processes, and cost considerations.
In an era where energy efficiency and sustainability are paramount, having access to reliable information can empower buyers to select the right manufacturer that aligns with their operational goals and budgetary constraints. This guide is designed to equip you with actionable insights that enhance your purchasing strategies, ensuring you partner with manufacturers who meet industry standards and regulatory requirements.
By exploring key factors such as technological advancements, regional supplier capabilities, and market trends, this resource aims to facilitate a smoother procurement process. With a focus on practical solutions tailored to your specific geographical context, you will be better positioned to navigate the global market for power station manufacturers effectively.
Understanding power station manufacturer Types and Variations
Type Name | Key Distinguishing Features | Primary B2B Applications | Brief Pros & Cons for Buyers |
---|---|---|---|
Thermal Power Station | Uses fossil fuels (coal, gas, oil); high energy output | Industrial power supply, urban energy grids | Pros: Established technology, high reliability. Cons: Environmental concerns, fuel dependency. |
Hydroelectric Power Station | Utilizes water flow; renewable energy source | Large-scale energy production, irrigation | Pros: Sustainable, low operating costs. Cons: High initial investment, geographical limitations. |
Solar Power Station | Converts sunlight into electricity; modular design | Commercial buildings, off-grid solutions | Pros: Renewable, decreasing costs. Cons: Intermittent energy, space requirements. |
Nuclear Power Station | Uses nuclear reactions; high energy density | Large metropolitan areas, industrial sectors | Pros: Low emissions, high output. Cons: Radioactive waste, regulatory hurdles. |
Wind Power Station | Harnesses wind energy; can be onshore or offshore | Rural electrification, large-scale projects | Pros: Clean energy, scalable. Cons: Variable output, impact on wildlife. |
What Are the Characteristics of Thermal Power Stations?
Thermal power stations are a cornerstone of traditional energy generation, primarily relying on fossil fuels such as coal, natural gas, or oil. They are characterized by their ability to produce large amounts of energy and are widely used in industrial applications and urban energy grids. For B2B buyers, considerations include the reliability of energy supply and the environmental impact associated with emissions. While these plants are often seen as reliable, the growing focus on sustainability may push buyers to explore cleaner alternatives.
How Do Hydroelectric Power Stations Work?
Hydroelectric power stations leverage the kinetic energy of flowing water to generate electricity. They are considered one of the most reliable forms of renewable energy and are ideal for large-scale energy production and irrigation. For B2B buyers, the primary considerations include the high initial investment and the geographical limitations of suitable sites. However, once operational, hydroelectric plants have low operating costs and minimal environmental impact, making them attractive for long-term energy solutions.
What Are the Benefits of Solar Power Stations?
Solar power stations convert sunlight into electricity, making them a popular choice for businesses looking to reduce their carbon footprint. These systems can be modular, allowing for customization based on energy needs and available space. B2B buyers should consider the decreasing costs of solar technology and the potential for energy independence. However, challenges include intermittent energy generation due to weather conditions and the need for substantial space for installation.
Why Choose Nuclear Power Stations?
Nuclear power stations generate energy through nuclear fission, offering a high energy density compared to other sources. They are particularly suited for supplying large metropolitan areas and industrial sectors. B2B buyers must weigh the benefits of low emissions and high output against the challenges of radioactive waste management and stringent regulatory requirements. The perception of nuclear energy also varies significantly, influencing purchasing decisions.
What Are the Key Features of Wind Power Stations?
Wind power stations capture wind energy through turbines, either onshore or offshore. They are praised for their scalability and clean energy production, making them suitable for rural electrification and large-scale projects. B2B buyers should consider the variability in energy output and potential impacts on local wildlife when evaluating wind projects. As technology advances, the costs associated with wind energy continue to decrease, making it an increasingly viable option for energy procurement.
Related Video: Understanding Switching Mode Power Supplies
Key Industrial Applications of power station manufacturer
Industry/Sector | Specific Application of power station manufacturer | Value/Benefit for the Business | Key Sourcing Considerations for this Application |
---|---|---|---|
Energy Generation | Renewable energy power stations | Reduces carbon footprint and reliance on fossil fuels | Compliance with local regulations and environmental standards |
Mining and Resource Extraction | On-site power generation for mining operations | Increases operational efficiency and reduces costs | Fuel availability and type of power generation technology |
Agriculture | Irrigation systems powered by energy solutions | Enhances crop yield and optimizes water usage | Reliability of power supply and maintenance support |
Manufacturing | Industrial power solutions for factories | Ensures continuous production and minimizes downtime | Scalability and integration with existing systems |
Transportation and Logistics | Power supply for electric vehicle charging stations | Supports transition to sustainable transport | Infrastructure compatibility and local energy policies |
How Are Renewable Energy Power Stations Beneficial for International B2B Buyers?
Power station manufacturers are pivotal in the energy generation sector, particularly in renewable energy. These manufacturers provide solar, wind, and hydroelectric power stations that significantly reduce carbon footprints. For international B2B buyers in regions like Africa and South America, investing in renewable energy solutions can lead to energy independence and sustainability. Buyers should consider compliance with local regulations and environmental standards to ensure the feasibility of projects.
What Role Does On-Site Power Generation Play in Mining Operations?
In the mining industry, on-site power generation from power station manufacturers is vital for operational efficiency. These power stations can provide a stable energy source for machinery and processing plants, reducing reliance on external power grids. This is particularly advantageous in remote locations where energy supply is inconsistent. Buyers should focus on fuel availability and the type of power generation technology that aligns with their operational needs.
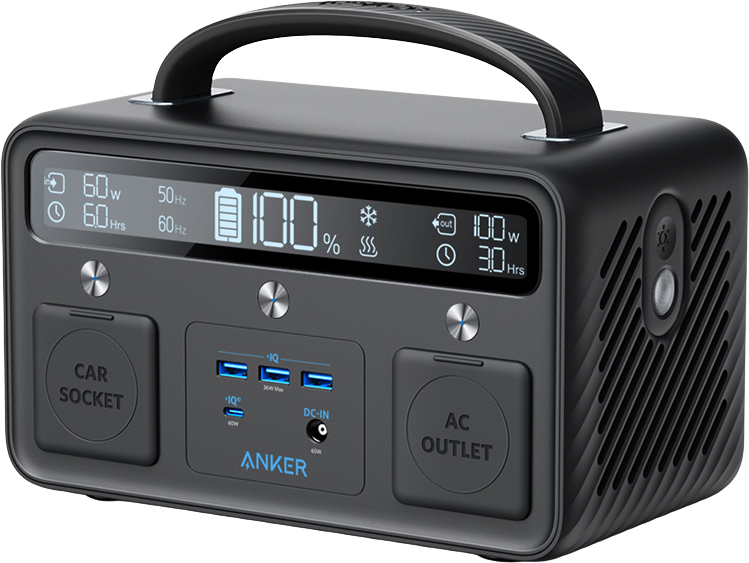
A stock image related to power station manufacturer.
How Can Power Solutions Enhance Agricultural Productivity?
Agriculture benefits significantly from power station manufacturers through the integration of energy solutions for irrigation systems. Reliable power sources enable farmers to enhance crop yields and optimize water usage, especially in regions prone to drought. International buyers must prioritize the reliability of the power supply and the availability of maintenance support to ensure the longevity of their systems.
Why Are Industrial Power Solutions Essential for Manufacturing?
In the manufacturing sector, power station manufacturers provide critical industrial power solutions that ensure continuous production. A reliable energy supply minimizes downtime, which is essential for maintaining productivity and profitability. B2B buyers must consider scalability and how well the power solutions integrate with existing manufacturing systems to maximize efficiency.
How Do Power Stations Support Sustainable Transportation?
Power station manufacturers are integral to the transportation and logistics sector, particularly with the rise of electric vehicles (EVs). By supplying power for EV charging stations, these manufacturers support the transition to sustainable transport solutions. Buyers should evaluate the compatibility of charging infrastructure with local energy policies and the existing grid to ensure successful implementation.
Related Video: Power Plant Explained | Working Principles
3 Common User Pain Points for ‘power station manufacturer’ & Their Solutions
Scenario 1: Navigating Regulatory Compliance in Power Station Projects
The Problem:
B2B buyers in regions such as Africa and South America often face complex regulatory landscapes when investing in power stations. Different countries have varying laws regarding environmental impact, safety standards, and energy production. These regulations can be cumbersome and may lead to project delays or increased costs if not adequately addressed. Buyers may feel overwhelmed by the need to understand and comply with these regulations, especially when sourcing equipment from international manufacturers.
The Solution:
To navigate these regulatory challenges effectively, buyers should conduct thorough research into the specific legal requirements of their target country. Engaging with local legal experts or consultants who specialize in energy regulations can provide invaluable insights. Furthermore, when sourcing power station equipment, buyers should prioritize manufacturers that are well-versed in local compliance issues and can provide documentation demonstrating their adherence to safety and environmental standards. By establishing a strong relationship with a manufacturer that understands local regulations, buyers can ensure smoother project execution and avoid potential legal pitfalls.
Scenario 2: Managing Quality Assurance and Reliability in Equipment Sourcing
The Problem:
In the power station sector, the reliability of equipment is paramount. Buyers often encounter issues with varying quality standards among manufacturers, leading to concerns over the durability and efficiency of the equipment. For example, a buyer may face significant downtime and repair costs if they invest in subpar machinery, impacting operational efficiency and profitability. This is particularly critical for buyers in the Middle East, where extreme weather conditions can further challenge equipment performance.
The Solution:
To mitigate quality assurance issues, buyers should implement a rigorous vetting process when selecting a power station manufacturer. This includes requesting detailed specifications, performance data, and third-party certifications for the equipment. Additionally, buyers should seek out manufacturers with a proven track record in similar environmental conditions. Conducting site visits to existing installations and obtaining references from other clients can also help gauge the reliability of the manufacturer’s products. Furthermore, establishing clear terms regarding warranties and maintenance support can enhance long-term equipment performance and reliability.
Scenario 3: Understanding Technological Advancements and Integration Challenges
The Problem:
As the energy sector evolves, staying abreast of technological advancements becomes crucial for B2B buyers. Many power station manufacturers now offer innovative solutions such as smart grid technology and renewable energy integration. However, buyers may struggle to understand how to effectively implement these technologies within their existing infrastructure. This lack of knowledge can lead to poor investment decisions and underutilization of advanced features, particularly in Europe, where energy efficiency is increasingly prioritized.
The Solution:
To overcome integration challenges, buyers should prioritize engaging with manufacturers that provide comprehensive training and support services. During the procurement process, inquire about the availability of training programs for staff on new technologies and how these innovations can be integrated into current systems. Additionally, buyers should consider collaborating with technology consultants who specialize in energy systems to create a roadmap for seamless integration. This proactive approach not only ensures that the latest technologies are effectively utilized but also maximizes the return on investment by enhancing operational efficiency and sustainability.
Strategic Material Selection Guide for power station manufacturer
What Are the Key Materials Used in Power Station Manufacturing?
When selecting materials for power station manufacturing, it is essential to consider the properties, advantages, and limitations of various materials. This guide analyzes four common materials used in the industry: Carbon Steel, Stainless Steel, Aluminum, and Composite Materials. Each material has unique characteristics that affect performance, durability, and cost, making them suitable for different applications within power stations.
How Does Carbon Steel Perform in Power Station Applications?
Key Properties: Carbon steel is known for its high strength and excellent mechanical properties, making it suitable for high-pressure applications. It typically withstands temperatures up to 600°C and offers good weldability.
Pros & Cons: The primary advantage of carbon steel is its cost-effectiveness and durability. However, it is susceptible to corrosion, especially in humid environments, which can lead to maintenance challenges. Additionally, its weight may pose logistical concerns during transportation and installation.
Impact on Application: Carbon steel is commonly used in structural components, piping, and pressure vessels. Its compatibility with various media, including water and steam, makes it a versatile choice.
Considerations for International Buyers: Buyers from regions like Africa and South America should ensure compliance with international standards such as ASTM A106 for seamless carbon steel pipes. Understanding local environmental conditions is crucial for selecting appropriate grades to mitigate corrosion risks.
What Are the Advantages of Using Stainless Steel?
Key Properties: Stainless steel offers exceptional corrosion resistance due to its chromium content, making it suitable for harsh environments. It can withstand temperatures up to 800°C and has good mechanical properties.
Pros & Cons: The primary advantage of stainless steel is its longevity and reduced maintenance costs over time. However, it is significantly more expensive than carbon steel, which may impact budget considerations. The manufacturing complexity can also be higher due to its work-hardening properties.
Impact on Application: Stainless steel is ideal for applications involving corrosive substances, such as in cooling systems and chemical processing. Its compatibility with a wide range of media enhances its appeal in power generation.
Considerations for International Buyers: European buyers, particularly in the UK, should consider compliance with EN 10088 standards for stainless steel. Understanding the specific grades required for different applications is vital for ensuring optimal performance.
How Does Aluminum Compare in Power Station Manufacturing?
Key Properties: Aluminum is lightweight and has excellent corrosion resistance. It typically operates effectively at temperatures up to 400°C and has a high strength-to-weight ratio.
Pros & Cons: The main advantage of aluminum is its lightweight nature, which simplifies installation and reduces transportation costs. However, it has lower strength compared to steel and is not suitable for high-pressure applications, limiting its use in certain components.
Impact on Application: Aluminum is often used in electrical enclosures and heat exchangers where weight savings are critical. Its corrosion resistance makes it suitable for outdoor applications.
Considerations for International Buyers: Buyers in the Middle East should be aware of the impact of high temperatures on aluminum performance. Compliance with ASTM B221 for aluminum extrusions is essential for ensuring quality.
What Role Do Composite Materials Play in Power Stations?
Key Properties: Composite materials, such as fiberglass and carbon fiber, offer high strength and low weight. They can withstand a range of temperatures depending on the resin used, often exceeding 200°C.
Pros & Cons: The primary advantage of composites is their resistance to corrosion and low maintenance requirements. However, they can be more expensive than traditional materials and may require specialized manufacturing techniques.
Impact on Application: Composites are increasingly used in turbine blades and other components where weight reduction is crucial. Their compatibility with various media makes them versatile.
Considerations for International Buyers: Buyers should check for compliance with international standards such as ASTM D3039 for tensile properties of composites. Understanding the specific applications and limitations of composite materials is essential for effective selection.
Summary Table of Material Selection for Power Station Manufacturing
Material | Typical Use Case for Power Station Manufacturer | Key Advantage | Key Disadvantage/Limitation | Relative Cost (Low/Med/High) |
---|---|---|---|---|
Carbon Steel | Structural components, piping, pressure vessels | Cost-effective and durable | Susceptible to corrosion | Low |
Stainless Steel | Cooling systems, chemical processing | Exceptional corrosion resistance | Higher cost and manufacturing complexity | High |
Aluminum | Electrical enclosures, heat exchangers | Lightweight and corrosion-resistant | Lower strength compared to steel | Medium |
Composite Materials | Turbine blades, lightweight components | Low maintenance and high strength-to-weight ratio | Higher cost and specialized manufacturing | High |
This guide provides a comprehensive overview of the strategic material selection process for power station manufacturers, ensuring that international B2B buyers are equipped with the necessary insights to make informed decisions.
In-depth Look: Manufacturing Processes and Quality Assurance for power station manufacturer
What Are the Main Stages of Manufacturing for Power Station Equipment?
The manufacturing process for power station equipment involves several critical stages, each designed to ensure that the final product meets stringent performance and safety standards. Understanding these stages can help international B2B buyers from regions like Africa, South America, the Middle East, and Europe make informed procurement decisions.
1. Material Preparation
Material preparation is the first stage and involves selecting high-quality raw materials that meet specific industry standards. Manufacturers often source materials like steel, aluminum, and specialized alloys based on their durability and resistance to environmental factors. Key techniques in this stage include:
- Material Inspection: Before processing, materials undergo rigorous inspections to ensure they meet mechanical and chemical specifications.
- Cutting and Shaping: Advanced technologies like laser cutting and water jet cutting are used to shape materials into required dimensions, minimizing waste and enhancing precision.
2. Forming Techniques in Power Station Manufacturing
After material preparation, the next step is forming. This stage transforms raw materials into components through various techniques:
- Casting: Molten metal is poured into molds to create complex shapes. This technique is commonly used for components like turbine casings.
- Forging: This method involves shaping metal using compressive forces, which enhances strength and durability. It’s often used for critical components such as shafts and gears.
- Welding and Fabrication: Welding techniques (TIG, MIG, and arc welding) are employed to join components together, followed by fabrication processes to finalize shapes.
3. Assembly Processes for Power Station Equipment
Assembly is a crucial stage where individual components are integrated into the final product. Key considerations include:
- Modular Assembly: Many manufacturers use modular assembly techniques, allowing for easier upgrades and maintenance.
- Robotic Automation: Automation in assembly lines enhances precision and reduces human error, significantly improving efficiency.
4. Finishing Touches
The finishing stage is essential for ensuring that the equipment can withstand operational conditions. Techniques here include:
- Surface Treatment: Processes such as galvanizing, painting, and coating provide corrosion resistance and enhance aesthetic appeal.
- Quality Control (QC) Measures: Before products leave the facility, they undergo extensive QC checks to ensure they meet performance specifications.
How Is Quality Assurance Implemented in Power Station Manufacturing?
Quality assurance (QA) is integral to the manufacturing process, ensuring that products not only meet regulatory standards but also fulfill customer expectations. For international B2B buyers, understanding QA practices is crucial for mitigating risks.
1. What Are the Relevant International Standards for Power Station Manufacturing?
Manufacturers often adhere to various international standards, including:
- ISO 9001: This standard focuses on quality management systems and is vital for demonstrating consistent product quality.
- CE Marking: For products marketed in Europe, CE marking indicates compliance with health, safety, and environmental protection standards.
- API Standards: The American Petroleum Institute (API) sets standards for products used in the oil and gas industry, which may also apply to power station manufacturing.
2. What Are the Key Quality Control Checkpoints?
Quality control is typically segmented into several checkpoints:
- Incoming Quality Control (IQC): This involves inspecting raw materials upon arrival to ensure they meet specified standards.
- In-Process Quality Control (IPQC): During manufacturing, continuous monitoring is performed to identify defects early in the process.
- Final Quality Control (FQC): Before shipment, products undergo rigorous testing and inspection to confirm they meet all specifications.
What Testing Methods Are Commonly Used in Power Station Manufacturing?
Testing methods are essential for validating the performance and safety of power station equipment. Common methods include:
- Non-Destructive Testing (NDT): Techniques such as ultrasonic testing and magnetic particle inspection help detect internal flaws without damaging the components.
- Pressure Testing: This method is used to assess the integrity of pressure vessels and piping systems.
- Performance Testing: Equipment is subjected to operational conditions to ensure it meets performance specifications.
How Can B2B Buyers Verify Supplier Quality Control?
For international B2B buyers, particularly those from diverse regions like Africa, South America, the Middle East, and Europe, verifying supplier quality control is crucial. Here are effective strategies:
1. Conducting Supplier Audits
Buyers should perform regular audits of potential suppliers to assess their manufacturing processes and quality control systems. This includes:
- On-Site Inspections: Visiting manufacturing facilities allows buyers to observe processes firsthand and ask relevant questions.
- Reviewing Quality Management Systems: Understanding how a supplier implements ISO 9001 or other relevant standards can provide insights into their commitment to quality.
2. Requesting Quality Reports and Certifications
Buyers can ask suppliers for documentation that demonstrates compliance with international standards. Key documents to request include:
- Certificates of Compliance: These documents indicate that products meet specific regulatory requirements.
- Quality Control Reports: Regular QC reports provide transparency into the supplier’s manufacturing processes and any issues encountered.
3. Utilizing Third-Party Inspection Services
Engaging third-party inspection services can provide an unbiased assessment of a supplier’s quality control practices. These services can conduct:
- Pre-Shipment Inspections: Ensuring products meet specifications before they leave the manufacturing facility.
- Random Sampling: Inspecting a sample of goods during production to verify quality.
Conclusion: Navigating the Quality Assurance Landscape in Power Station Manufacturing
Understanding the intricacies of manufacturing processes and quality assurance in power station manufacturing is essential for international B2B buyers. By knowing the main stages of manufacturing, relevant quality standards, testing methods, and verification strategies, buyers can make informed decisions that align with their operational needs and compliance requirements. This comprehensive approach not only enhances procurement efficiency but also fosters long-term partnerships with reliable suppliers.
Practical Sourcing Guide: A Step-by-Step Checklist for ‘power station manufacturer’
In today’s competitive energy market, sourcing a power station manufacturer requires careful planning and execution. This checklist provides international B2B buyers, particularly from Africa, South America, the Middle East, and Europe, with actionable steps to ensure a successful procurement process.
Step 1: Define Your Technical Specifications
Clearly outline the technical requirements for the power station you need. This includes the type of power generation (e.g., renewable, fossil fuels), capacity (in MW), and operational parameters.
– Why it’s important: Specific technical specifications help narrow down potential suppliers who can meet your unique needs.
– What to look for: Consider local regulations, grid compatibility, and environmental impact assessments.
Step 2: Research and Shortlist Manufacturers
Conduct thorough market research to identify potential manufacturers. Utilize industry reports, trade shows, and online directories to create a shortlist.
– Why it’s important: A well-researched list helps you focus on manufacturers with a proven track record in your required technology.
– What to look for: Evaluate their experience, project portfolio, and market presence, especially in your region.
Step 3: Evaluate Supplier Certifications
Verify that shortlisted manufacturers possess relevant certifications and standards, such as ISO 9001 for quality management and ISO 14001 for environmental management.
– Why it’s important: Certifications indicate a manufacturer’s commitment to quality and regulatory compliance, which can minimize risks.
– What to look for: Ensure certifications are current and applicable to your project’s specifications.
Step 4: Request Proposals and Quotes
Reach out to your shortlisted manufacturers to request detailed proposals and quotes. Provide them with your technical specifications to receive tailored responses.
– Why it’s important: This step allows you to compare not just prices but also the scope of services, delivery timelines, and warranty terms.
– What to look for: Ensure clarity in their proposals regarding inclusions, exclusions, and the terms of service.
Step 5: Assess Financial Stability
Investigate the financial health of the manufacturers you are considering. Request financial statements or credit ratings to ensure they can fulfill large contracts.
– Why it’s important: A financially stable manufacturer is more likely to deliver on time and sustain operations during the project lifecycle.
– What to look for: Look for consistent revenue growth, profitability, and positive cash flow indicators.
Step 6: Conduct Site Visits and Factory Audits
If possible, conduct site visits to the manufacturers’ facilities to assess their capabilities and quality control processes firsthand.
– Why it’s important: On-site evaluations provide insights into manufacturing practices and the overall production environment.
– What to look for: Check for adherence to safety protocols, equipment quality, and production capacity.
Step 7: Review Contracts and Terms of Service
Before finalizing any agreement, carefully review the contract terms, including payment schedules, delivery timelines, and after-sales support.
– Why it’s important: A clear contract protects both parties and ensures that expectations are aligned.
– What to look for: Pay attention to clauses related to penalties for delays, warranty conditions, and dispute resolution mechanisms.
By following this comprehensive checklist, international B2B buyers can navigate the complexities of sourcing a power station manufacturer effectively, ensuring a successful procurement process that meets their specific needs.
Comprehensive Cost and Pricing Analysis for power station manufacturer Sourcing
What Are the Key Cost Components in Sourcing Power Stations?
When sourcing power stations, understanding the cost structure is vital for international B2B buyers, especially in regions like Africa, South America, the Middle East, and Europe. The primary cost components include:
-
Materials: The choice of materials—such as steel, copper, and specialized alloys—greatly affects the total cost. High-quality materials may increase upfront costs but can enhance durability and performance, which is crucial for long-term investments.
-
Labor: Labor costs vary significantly by region. Countries with lower labor costs may reduce manufacturing expenses, but this can impact the quality of work. It’s important to assess the skill level and experience of the workforce involved in the manufacturing process.
-
Manufacturing Overhead: This encompasses indirect costs associated with production, such as utilities, rent, and administrative expenses. Efficient management of overhead can lead to significant savings.
-
Tooling: Custom tooling for specific designs can be a substantial upfront investment. However, it can lead to increased efficiency and reduced production times in the long run.
-
Quality Control (QC): Implementing rigorous QC processes ensures that the power stations meet necessary standards and certifications, which may incur additional costs but ultimately safeguards against failures and recalls.
-
Logistics: Transportation and handling costs can vary based on the distance from the manufacturing facility to the buyer’s location. Incoterms play a crucial role in determining who bears these costs.
-
Margin: The profit margin set by the manufacturer can differ based on market dynamics, competition, and the perceived value of the product. Understanding these margins can provide insight into pricing flexibility during negotiations.
How Do Price Influencers Affect Power Station Sourcing?
Several factors influence the pricing of power stations, and being aware of these can empower buyers to make informed decisions:
-
Volume and Minimum Order Quantity (MOQ): Purchasing larger volumes often leads to reduced per-unit costs. Buyers should negotiate MOQs that align with their project needs to optimize their investment.
-
Specifications and Customization: Custom specifications may lead to higher costs due to the need for specialized materials or processes. Clear communication of requirements can help mitigate unexpected price increases.
-
Materials and Quality Certifications: Manufacturers that provide certified quality standards (ISO, CE, etc.) may charge a premium. However, these certifications can ensure reliability and compliance with regulatory standards, offering long-term cost savings.
-
Supplier Factors: The supplier’s reputation, experience, and financial stability can influence pricing. Established suppliers may offer better warranties and support, justifying a higher price point.
-
Incoterms: Understanding Incoterms is crucial for determining the responsibilities of buyers and sellers in terms of shipping, insurance, and tariffs, which can affect overall costs.
What Tips Can Help Buyers Negotiate Better Prices?
International B2B buyers can leverage several strategies to enhance their procurement process:
-
Effective Negotiation: Approach negotiations with a clear understanding of your budget and the value you expect. Be prepared to discuss terms such as payment schedules, delivery timelines, and after-sales service.
-
Focus on Cost-Efficiency: Analyze the Total Cost of Ownership (TCO), which includes initial costs, operating expenses, maintenance, and potential downtime. This holistic view can help justify higher upfront costs if they lead to lower long-term expenses.
-
Be Aware of Pricing Nuances: Understand that pricing can be affected by geopolitical factors, currency fluctuations, and local economic conditions, particularly in emerging markets. Stay informed about these trends to better time your purchases.
Disclaimer on Pricing
It’s important to note that the prices associated with power station manufacturing can vary widely based on the aforementioned factors. Prices are indicative and may fluctuate based on market conditions, supplier negotiations, and specific project requirements. Always seek quotes from multiple suppliers to ensure competitive pricing.
Alternatives Analysis: Comparing power station manufacturer With Other Solutions
In today’s rapidly evolving energy landscape, businesses need to explore various solutions for power generation to meet their operational needs efficiently. This section compares traditional power station manufacturers with two viable alternatives: renewable energy systems (solar and wind) and energy storage solutions (battery systems). Understanding these alternatives is crucial for international B2B buyers, particularly those in Africa, South America, the Middle East, and Europe, where energy demands and resource availability vary significantly.
Comparison Table of Power Generation Solutions
Comparison Aspect | Power Station Manufacturer | Renewable Energy Systems (Solar/Wind) | Energy Storage Solutions (Battery Systems) |
---|---|---|---|
Performance | High capacity, continuous supply | Variable output based on weather conditions | Steady output, but dependent on charge levels |
Cost | High initial investment; long-term savings | Moderate to high initial cost; decreasing with technology | Moderate upfront costs; ongoing operational costs |
Ease of Implementation | Complex; requires extensive infrastructure | Site-dependent; requires planning and permits | Generally easier; can be integrated into existing systems |
Maintenance | High maintenance needs; specialized staff required | Low maintenance; occasional inspections needed | Low maintenance; regular checks for efficiency |
Best Use Case | Large industrial applications needing constant power | Remote areas with high solar/wind potential | Backup power for critical operations or load leveling |
What Are the Pros and Cons of Renewable Energy Systems?
Renewable energy systems, such as solar and wind, present a sustainable alternative to traditional power generation. The primary advantage lies in their environmental benefits and the decreasing costs of technology. In regions with abundant sunlight or wind, these systems can provide a reliable energy source with low ongoing costs. However, the variability in energy production due to changing weather conditions can pose challenges, making them less suitable for applications requiring constant energy supply.
How Do Energy Storage Solutions Work as an Alternative?
Energy storage solutions, particularly battery systems, have gained traction as a viable alternative to traditional power stations. They offer the advantage of providing steady power output, regardless of generation source variability. This makes them particularly useful for applications requiring backup power or load leveling during peak demands. However, the initial costs can be significant, and ongoing operational expenses are associated with battery management and replacement.
Conclusion: How Can B2B Buyers Choose the Right Power Solution?
Choosing the right power generation solution depends on various factors, including operational needs, budget constraints, and environmental considerations. For B2B buyers, it’s essential to evaluate the specific energy requirements of their operations, the reliability of the energy sources available, and the long-term cost implications of each solution. By conducting a thorough analysis of these alternatives, businesses can make informed decisions that align with their sustainability goals and operational efficiency.
Essential Technical Properties and Trade Terminology for power station manufacturer
What are the Essential Technical Properties for Power Station Manufacturers?
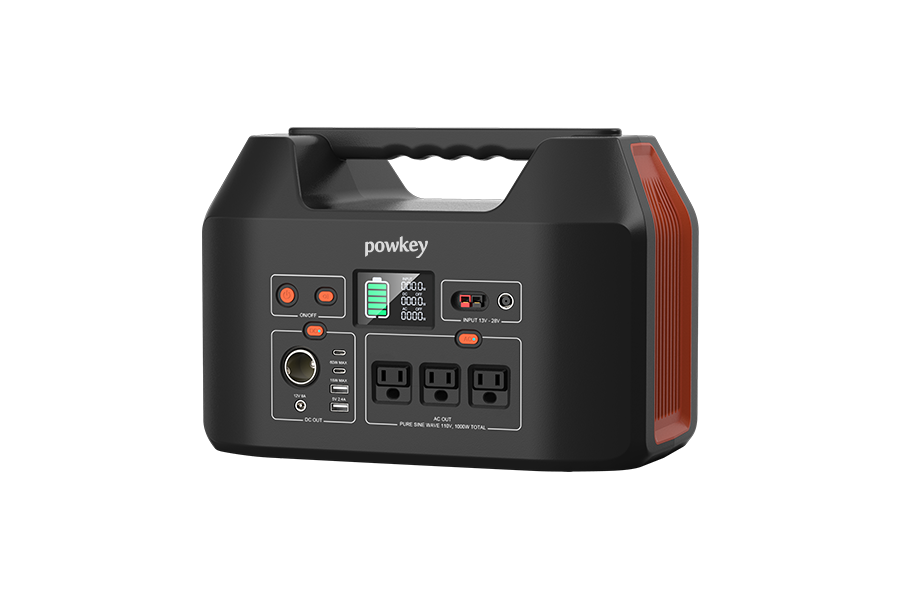
A stock image related to power station manufacturer.
When selecting a power station manufacturer, understanding the technical properties of the products is crucial. Here are some key specifications that every B2B buyer should be aware of:
1. Material Grade
Material grade refers to the type and quality of materials used in manufacturing power stations, such as steel or aluminum. The grade affects durability, corrosion resistance, and overall performance. For instance, higher-grade steel can withstand extreme temperatures and pressures, making it ideal for energy production.
2. Tolerance Levels
Tolerance levels indicate the permissible limits of variation in a physical dimension. In power stations, precise tolerances are essential for components like turbines and generators. Tight tolerances ensure optimal performance and energy efficiency, which directly impacts operational costs.
3. Energy Efficiency Rating
This rating measures how effectively a power station converts fuel into energy. Higher energy efficiency translates to lower operational costs and reduced environmental impact. B2B buyers should prioritize manufacturers that provide transparent energy efficiency ratings to align with sustainability goals.
4. Capacity and Output
Capacity refers to the maximum power output a power station can generate, typically measured in megawatts (MW). Understanding the capacity is vital for buyers to ensure that the power station meets the energy demands of their projects or regions.
5. Compliance Standards
Manufacturers must comply with local and international standards (e.g., ISO, IEC) related to safety, environmental impact, and quality. Ensuring compliance helps mitigate risks associated with regulatory fines and enhances the credibility of your procurement.
6. Maintenance Intervals
Maintenance intervals refer to the recommended periods between servicing and repairs. Longer intervals can lead to reduced downtime and lower operational costs. Buyers should inquire about maintenance schedules to assess the long-term viability of a power station.
What Trade Terminology Should International Buyers Understand?
Familiarizing yourself with industry jargon can significantly enhance your negotiation and procurement process. Here are several essential terms:
1. OEM (Original Equipment Manufacturer)
An OEM is a company that produces parts or equipment that may be marketed by another manufacturer. Understanding OEM relationships is crucial for buyers seeking reliable components and ensuring compatibility with existing systems.
2. MOQ (Minimum Order Quantity)
MOQ refers to the smallest quantity of a product that a supplier is willing to sell. Knowing the MOQ is essential for budget planning and inventory management, especially for large-scale projects.
3. RFQ (Request for Quotation)
An RFQ is a document that a buyer sends to suppliers requesting a price quote for specific products or services. Crafting a detailed RFQ can lead to better pricing and terms, making it a vital tool for cost-effective procurement.
4. Incoterms (International Commercial Terms)
Incoterms are a set of international rules that define the responsibilities of buyers and sellers in international transactions. Familiarity with Incoterms can help buyers understand shipping, insurance, and tariff responsibilities, ultimately reducing risks associated with cross-border procurement.
5. Lead Time
Lead time refers to the duration between placing an order and receiving the goods. Understanding lead times is crucial for project scheduling and resource allocation, especially in industries where time is of the essence.
6. Warranty and Support Terms
These terms define the guarantees provided by manufacturers regarding product performance and the support available for maintenance or issues. Buyers should carefully review these terms to ensure they receive adequate support throughout the product lifecycle.
By understanding these essential technical properties and trade terminologies, international B2B buyers can make informed decisions when selecting a power station manufacturer, ensuring alignment with their operational and financial goals.
Navigating Market Dynamics and Sourcing Trends in the power station manufacturer Sector
What Are the Key Trends Influencing the Power Station Manufacturer Market?
The power station manufacturing sector is undergoing significant transformation driven by several global factors. One of the primary drivers is the urgent need for sustainable energy solutions. As nations across Africa, South America, the Middle East, and Europe prioritize renewable energy sources, power station manufacturers are increasingly investing in technologies such as solar, wind, and hydropower. This shift is not only in response to climate change but also to meet the growing demand for reliable energy supply, particularly in emerging markets.
Additionally, advancements in digital technologies, such as IoT and AI, are reshaping how power stations operate. These technologies enhance operational efficiency through predictive maintenance and real-time monitoring, which can significantly reduce downtime and operational costs. B2B buyers should look for manufacturers that leverage these technologies to provide smart energy solutions that align with industry 4.0.
Furthermore, the global supply chain landscape is evolving. Post-pandemic, there has been a noticeable shift towards local sourcing to mitigate risks associated with international supply chains. Buyers are encouraged to explore partnerships with local manufacturers or those who have established robust logistics networks to ensure timely delivery and service continuity.
How Can Sustainability and Ethical Sourcing Impact Your Supply Chain Decisions?
In today’s market, sustainability and ethical sourcing are not just trends but essential components of a responsible business strategy. The environmental impact of power generation is significant, and manufacturers are increasingly held accountable for their carbon footprints. International B2B buyers from diverse regions must prioritize suppliers that demonstrate a commitment to sustainability through the use of eco-friendly materials and processes.
Certifications such as ISO 14001 (Environmental Management) and adherence to international sustainability standards can serve as indicators of a manufacturer’s dedication to ethical practices. Buyers should actively seek manufacturers who utilize renewable materials, minimize waste, and adopt energy-efficient practices in their production processes.
Moreover, a transparent supply chain that prioritizes ethical sourcing can enhance brand reputation and customer loyalty. As consumers become more environmentally conscious, businesses that prioritize sustainability can differentiate themselves in the marketplace, ultimately leading to increased competitiveness.
What is the Historical Context of the Power Station Manufacturing Sector?
The evolution of the power station manufacturing sector dates back to the Industrial Revolution when coal-fired plants became the primary source of energy. Over the decades, technological advancements led to the diversification of power generation methods, including hydroelectric, nuclear, and natural gas. The late 20th century marked a pivotal shift toward renewable energy sources, as environmental concerns and the depletion of fossil fuels became more pronounced.
Today, the industry is characterized by a blend of traditional and innovative energy solutions, catering to the diverse needs of global markets. The historical context of the sector highlights the importance of adaptability and foresight for manufacturers and buyers alike, as they navigate the complexities of an ever-evolving energy landscape. Understanding this evolution is crucial for B2B buyers as they make informed sourcing decisions that align with both current demands and future market dynamics.
Frequently Asked Questions (FAQs) for B2B Buyers of power station manufacturer
-
How do I choose the right power station manufacturer for my business needs?
When selecting a power station manufacturer, consider factors such as their experience in the industry, product certifications, and client testimonials. Evaluate their ability to customize solutions based on your specific requirements, such as capacity, technology, and efficiency. Additionally, assess their after-sales support and maintenance services, as these can significantly impact the longevity and performance of your investment. Conducting site visits or virtual tours can also provide insight into their manufacturing processes and quality control measures. -
What are the key certifications to look for in a power station manufacturer?
Key certifications to consider include ISO 9001 for quality management systems, ISO 14001 for environmental management, and OHSAS 18001 for occupational health and safety. Additionally, check for specific product certifications like CE (Conformité Européenne) for Europe, UL (Underwriters Laboratories) for North America, and IEC (International Electrotechnical Commission) standards. These certifications not only ensure compliance with safety and quality regulations but also enhance the manufacturer’s credibility in the global market. -
What is the minimum order quantity (MOQ) when sourcing from power station manufacturers?
The minimum order quantity (MOQ) can vary significantly between manufacturers. Typically, larger manufacturers may have higher MOQs due to their production capabilities, while smaller or niche manufacturers might offer lower MOQs to accommodate smaller projects. It’s essential to communicate your specific needs with potential suppliers to negotiate favorable terms. Consider leveraging group purchasing or forming alliances with other buyers to meet MOQ requirements if necessary. -
What are common payment terms when dealing with international power station manufacturers?
Common payment terms in international trade often include a 30% deposit upon order confirmation and the remaining 70% before shipment. Some manufacturers may offer letters of credit (LC) or payment via escrow services to provide additional security. It’s crucial to discuss and agree on payment terms upfront to avoid misunderstandings. Also, ensure that you understand any currency exchange implications and the potential impact of tariffs or duties on your overall costs. -
How can I ensure quality assurance in my power station order?
To ensure quality assurance, request detailed product specifications and quality control processes from the manufacturer. Consider implementing a pre-shipment inspection, where a third-party inspection service evaluates the products before they leave the factory. Establishing clear communication regarding your quality expectations and standards will also help in mitigating risks. Additionally, reviewing the manufacturer’s track record in handling quality issues can provide insight into their commitment to excellence. -
What logistics considerations should I keep in mind when importing power stations?
Logistics considerations include selecting a reliable freight forwarder, understanding shipping timelines, and being aware of import regulations in your country. Determine the most cost-effective shipping method—whether air or sea—based on urgency and budget. Additionally, consider warehousing options if you require storage before distribution. Lastly, ensure all necessary documentation, such as bills of lading and customs clearance paperwork, is in order to facilitate smooth transit. -
How do I vet international suppliers for reliability?
Vetting international suppliers involves researching their reputation through online reviews, industry forums, and trade associations. Request references from previous clients and conduct background checks on their financial stability. Additionally, if possible, visit their manufacturing facility to assess operational capabilities and quality control practices. Engaging with local trade offices or chambers of commerce can also provide valuable insights into the supplier’s reliability and standing in the industry. -
What customization options are typically available from power station manufacturers?
Customization options can vary widely among manufacturers but often include adjustments in capacity, design, and technology integration to meet specific project requirements. Many manufacturers offer tailored solutions, such as hybrid systems combining renewable energy sources with conventional power generation. Discuss your project’s unique needs during initial consultations to explore available options. Be sure to inquire about the lead times and additional costs associated with custom orders to plan your procurement strategy effectively.
Important Disclaimer & Terms of Use
⚠️ Important Disclaimer
The information provided in this guide, including content regarding manufacturers, technical specifications, and market analysis, is for informational and educational purposes only. It does not constitute professional procurement advice, financial advice, or legal advice.
While we have made every effort to ensure the accuracy and timeliness of the information, we are not responsible for any errors, omissions, or outdated information. Market conditions, company details, and technical standards are subject to change.
B2B buyers must conduct their own independent and thorough due diligence before making any purchasing decisions. This includes contacting suppliers directly, verifying certifications, requesting samples, and seeking professional consultation. The risk of relying on any information in this guide is borne solely by the reader.
Strategic Sourcing Conclusion and Outlook for power station manufacturer
What Are the Key Takeaways for B2B Buyers in the Power Station Manufacturing Sector?
In the dynamic landscape of power station manufacturing, international B2B buyers must prioritize strategic sourcing to optimize their procurement processes. Understanding regional energy demands, especially in Africa, South America, the Middle East, and Europe, is crucial for making informed purchasing decisions. Buyers should leverage local partnerships to navigate regulatory environments and cultural nuances, enhancing supply chain resilience and sustainability.
How Can Strategic Sourcing Drive Value in Power Station Procurement?
By adopting a strategic sourcing approach, businesses can achieve significant cost savings, improve supplier relationships, and ensure compliance with evolving industry standards. This proactive strategy allows companies to align their procurement goals with broader organizational objectives, such as reducing carbon footprints and enhancing operational efficiency.
What Does the Future Hold for International B2B Buyers in Power Station Manufacturing?
Looking ahead, the power station manufacturing sector is poised for innovation, driven by advancements in renewable energy technologies and smart grid solutions. International buyers should stay informed about emerging trends and technologies to capitalize on new opportunities. Engage with manufacturers who demonstrate a commitment to sustainability and innovation to ensure that your energy solutions are future-proof.
In conclusion, strategic sourcing is not just a procurement tactic; it is a vital component of a successful energy strategy. As you navigate this complex landscape, embrace collaboration and innovation to secure your position as a leader in the evolving energy market.