Unlock Savings: The Ultimate Spare Parts Supplier Guide (2025)
Introduction: Navigating the Global Market for spare parts supplier
In today’s fast-paced global economy, sourcing spare parts from reliable suppliers can be a daunting challenge for international B2B buyers, especially those operating in diverse markets such as Africa, South America, the Middle East, and Europe. The need for high-quality components that meet specific operational requirements is paramount, yet navigating the myriad options available can be overwhelming. This guide delves into the complexities of finding and selecting spare parts suppliers, providing insights into various types of spare parts, their applications across different industries, and effective supplier vetting processes.
From understanding the nuances of pricing and cost structures to evaluating supplier reliability and performance, this comprehensive resource equips B2B buyers with the necessary tools to make informed purchasing decisions. We will explore essential factors to consider when sourcing spare parts, such as certifications, delivery timelines, and after-sales support. Additionally, the guide addresses specific challenges faced by buyers in regions like Nigeria and Poland, ensuring that content is tailored to the unique needs of these markets.
By leveraging the information presented in this guide, international B2B buyers will be empowered to streamline their procurement processes, mitigate risks, and enhance operational efficiency. Ultimately, informed decision-making in selecting spare parts suppliers can lead to improved production quality and a competitive edge in the global marketplace.
Understanding spare parts supplier Types and Variations
Type Name | Key Distinguishing Features | Primary B2B Applications | Brief Pros & Cons for Buyers |
---|---|---|---|
OEM Suppliers | Manufacturer-certified parts, high quality | Automotive, machinery, electronics | Pros: Reliability, guaranteed compatibility. Cons: Higher costs, limited flexibility. |
Aftermarket Suppliers | Non-OEM parts, often lower cost, varied quality | Automotive, industrial equipment | Pros: Cost-effective, wider selection. Cons: Quality inconsistency, potential compatibility issues. |
Distributors | Broad range of brands, often carry stock | Various industries | Pros: Quick availability, diverse options. Cons: Higher prices due to middleman markup. |
Wholesalers | Bulk purchasing options, lower prices | Retail, manufacturing | Pros: Reduced costs for large orders. Cons: Minimum order quantities, less flexibility. |
Specialty Suppliers | Niche market focus, specialized products | Aerospace, medical devices | Pros: Expertise in specific parts, tailored solutions. Cons: Limited product range, often higher prices. |
What are the Characteristics of OEM Suppliers?
OEM (Original Equipment Manufacturer) suppliers provide parts that are specifically designed for use in their own products. These parts are often certified by the manufacturer, ensuring that they meet stringent quality standards and compatibility requirements. B2B buyers in industries such as automotive and machinery often prefer OEM parts for their reliability and performance. However, they come at a premium price, which can be a significant consideration for budget-conscious businesses.
How Do Aftermarket Suppliers Operate?
Aftermarket suppliers focus on providing non-OEM parts that are typically less expensive than their OEM counterparts. These suppliers offer a wide variety of options, catering to various industries including automotive and industrial equipment. While they can provide substantial cost savings, buyers must exercise caution regarding the quality and compatibility of these parts, as they may not always meet the same standards as OEM products.
What Role Do Distributors Play in Spare Parts Supply?
Distributors serve as intermediaries that stock a broad range of spare parts from multiple manufacturers. They are advantageous for B2B buyers who require quick access to various components across different industries. While distributors can provide a diverse selection and faster delivery times, their prices may be higher due to the added markup for their services. Buyers should weigh the convenience of quick availability against potential cost implications.
Why Choose Wholesalers for Bulk Purchasing?
Wholesalers specialize in selling spare parts in bulk, making them a preferred choice for businesses looking to lower their costs through larger orders. They typically offer lower prices per unit, which can be appealing for manufacturers and retailers. However, wholesalers often impose minimum order quantities, which may not suit all buyers, especially those with fluctuating needs or smaller operations.
What Are the Benefits of Specialty Suppliers?
Specialty suppliers focus on niche markets, providing specific spare parts that may not be widely available through general suppliers. They are particularly valuable in industries like aerospace and medical devices, where precision and expertise are critical. While these suppliers can offer tailored solutions and specialized knowledge, their limited product range and higher price points can be drawbacks for some buyers. It’s essential for businesses to assess their specific needs when considering specialty suppliers.
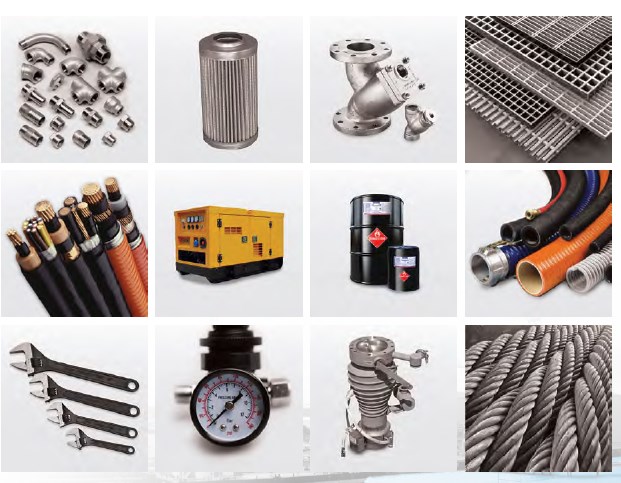
A stock image related to spare parts supplier.
Related Video: Functions and Classification of Spare Parts Management
Key Industrial Applications of spare parts supplier
Industry/Sector | Specific Application of spare parts supplier | Value/Benefit for the Business | Key Sourcing Considerations for this Application |
---|---|---|---|
Manufacturing | Replacement parts for machinery | Minimizes downtime, enhances operational efficiency | Quality assurance, lead times, compatibility with existing systems |
Automotive | Spare parts for vehicle maintenance | Ensures safety and reliability of vehicles | OEM vs. aftermarket parts, certification standards, pricing |
Oil and Gas | Components for drilling equipment | Improves safety and operational reliability | Supply chain stability, material specifications, local regulations |
Construction | Parts for heavy machinery | Reduces repair costs and prolongs equipment life | Availability of parts, supplier reputation, warranty terms |
Agriculture | Spare parts for agricultural equipment | Increases productivity and reduces crop loss | Seasonality of demand, durability of parts, local sourcing options |
How is Spare Parts Supplier Used in Manufacturing?
In the manufacturing sector, spare parts suppliers play a crucial role by providing replacement parts for machinery. This application is essential for minimizing downtime, which can significantly impact productivity and profitability. International B2B buyers, particularly from regions like Africa and South America, must ensure that the parts they source are compatible with existing machinery and meet quality standards. Moreover, lead times are critical; suppliers must be able to deliver parts promptly to avoid production halts.
What are the Applications of Spare Parts Suppliers in the Automotive Industry?
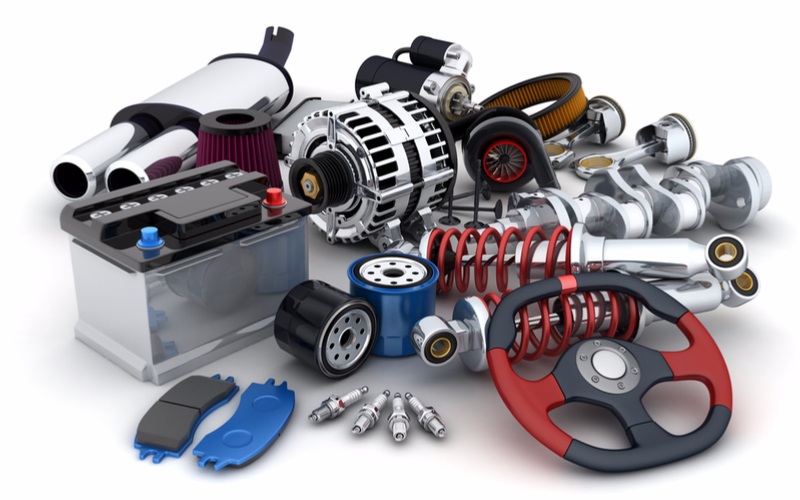
A stock image related to spare parts supplier.
In the automotive sector, spare parts suppliers provide essential components for vehicle maintenance and repair. This ensures the safety and reliability of vehicles, particularly in regions like the Middle East and Europe, where vehicle performance is paramount due to varying climates and road conditions. Buyers should consider whether to source OEM (Original Equipment Manufacturer) parts or aftermarket alternatives, as this choice can affect vehicle longevity and warranty. Additionally, understanding certification standards is vital to ensure compliance with local regulations.
How Do Spare Parts Suppliers Impact the Oil and Gas Sector?
In the oil and gas industry, spare parts suppliers provide critical components for drilling equipment, which are essential for safe and efficient operations. The reliability of these parts directly affects operational safety and productivity. Buyers in this sector, especially those in Africa and the Middle East, should focus on supply chain stability and material specifications, as these factors can influence the durability and performance of the equipment. Awareness of local regulations is also crucial for ensuring compliance and avoiding costly fines.
What Role Do Spare Parts Suppliers Play in Construction?
For the construction industry, spare parts suppliers are vital for providing parts for heavy machinery. This application helps reduce repair costs and prolongs the life of expensive equipment. Buyers must consider the availability of parts and the supplier’s reputation, as delays can lead to project overruns and increased costs. Warranty terms are another important factor, as they can protect against defects and ensure long-term performance, which is particularly important for international buyers in regions like Europe and South America.
How are Spare Parts Suppliers Beneficial for Agriculture?
In agriculture, spare parts suppliers provide components for various types of agricultural equipment, which is essential for maintaining productivity and reducing crop loss. This application is particularly crucial during peak seasons when equipment failure can lead to significant financial losses. Buyers should be aware of the seasonality of demand and consider sourcing durable parts that can withstand harsh environmental conditions. Additionally, local sourcing options may provide advantages in terms of cost and delivery times, which are essential for maximizing efficiency in agricultural operations.
Related Video: Centrifugal Pump Parts – Learn about Nine Parts
3 Common User Pain Points for ‘spare parts supplier’ & Their Solutions
Scenario 1: Difficulty in Finding Quality Spare Parts at Competitive Prices
The Problem:
B2B buyers often face the challenge of sourcing high-quality spare parts that meet their specific needs while also remaining within budget constraints. For example, a manufacturer in Nigeria may require specialized components for machinery that are not readily available in local markets. This scarcity can lead to reliance on overseas suppliers, which brings complications such as lengthy shipping times, customs delays, and the risk of receiving substandard parts. The pressure to minimize downtime while managing costs can make this situation particularly stressful.
The Solution:
To effectively address this issue, B2B buyers should establish relationships with multiple suppliers, both local and international. Start by conducting thorough research to identify reputable spare parts suppliers known for their quality and reliability. Utilize platforms like Alibaba or TradeKey to connect with suppliers that specialize in your required components. When sourcing, request samples or small test orders to evaluate quality before committing to larger purchases. Additionally, consider negotiating bulk purchase agreements with suppliers to secure better pricing and terms. This strategy not only fosters better relationships with suppliers but also ensures access to high-quality parts, ultimately minimizing operational disruptions.
Scenario 2: Inconsistent Supply Chain and Delivery Issues
The Problem:
Another significant challenge for international B2B buyers is the inconsistency in supply chains, particularly when dealing with spare parts suppliers across different regions. A company in South America might experience delays due to unforeseen shipping issues, customs regulations, or even political instability affecting transport routes. Such unpredictability can lead to production halts, affecting business continuity and customer satisfaction.
The Solution:
To mitigate these risks, buyers should implement a dual-sourcing strategy. This involves identifying multiple suppliers for the same parts, ideally from different geographical locations. By diversifying your supply base, you can create a buffer against disruptions. Additionally, work closely with logistics partners to monitor shipping routes and customs processes. Consider using software solutions that provide real-time tracking and updates on shipments, which can help in anticipating delays. Building strong communication channels with suppliers is also crucial; regular check-ins can help you stay informed about potential issues before they impact your operations.
Scenario 3: Lack of Technical Support and Product Knowledge
The Problem:
Many B2B buyers encounter difficulties due to insufficient technical support or product knowledge from spare parts suppliers. For instance, a buyer in Europe may purchase a complex component that requires specific installation techniques or integration with existing systems. Without adequate guidance, there is a risk of improper installation, leading to equipment failure and additional costs.
The Solution:
To overcome this challenge, it is essential to choose suppliers that provide comprehensive technical support and resources. Look for suppliers who offer detailed product documentation, installation guides, and access to technical support teams. Before finalizing a purchase, inquire about the availability of training or consultation services. Additionally, consider attending industry trade shows or webinars where suppliers showcase their products and provide educational content. This proactive approach not only enhances your understanding of the products but also builds a collaborative relationship with suppliers, ensuring you have the necessary support when integrating new spare parts into your operations.
Strategic Material Selection Guide for spare parts supplier
When selecting materials for spare parts, international B2B buyers must consider various factors that affect performance, cost, and compliance with regional standards. This guide analyzes common materials used in spare parts manufacturing, focusing on their properties, advantages, disadvantages, and implications for buyers in Africa, South America, the Middle East, and Europe.
What Are the Key Properties of Aluminum in Spare Parts?
Aluminum is a lightweight metal known for its excellent corrosion resistance and good thermal conductivity. It typically has a temperature rating of up to 600°C and can withstand moderate pressure levels. Its low density makes it ideal for applications where weight reduction is crucial.
Pros and Cons: The primary advantage of aluminum is its durability and resistance to oxidation, which extends the lifespan of spare parts. However, it can be more expensive than steel, and its manufacturing process is relatively complex, requiring specialized equipment. This complexity can lead to longer lead times for production.
Impact on Application: Aluminum is compatible with various media, including water and air, but it may not be suitable for highly corrosive environments without protective coatings. Buyers should ensure that aluminum parts meet specific industry standards, such as ASTM B211 for aluminum alloys.
How Does Steel Compare as a Material for Spare Parts?
Steel is a widely used material known for its strength and versatility. It can handle high temperature and pressure ratings, making it suitable for heavy-duty applications. Steel is often treated to enhance its corrosion resistance, particularly in harsh environments.
Pros and Cons: The key advantage of steel is its robustness and relatively low cost compared to other materials like titanium or aluminum. However, steel’s susceptibility to rust and corrosion can be a significant drawback, especially in humid or saline environments. Additionally, the manufacturing complexity can vary depending on the type of steel being used.
Impact on Application: Steel is compatible with various media, including oil and gas, but buyers must consider the specific type of steel (e.g., stainless or carbon) based on the application. Compliance with standards such as ASTM A36 or DIN 17100 is critical for international buyers.
What Are the Benefits of Using Plastics in Spare Parts Manufacturing?
Plastics, particularly engineering plastics like polycarbonate and nylon, are increasingly popular due to their lightweight nature and resistance to chemicals. They can operate effectively at temperatures up to 120°C, making them suitable for various applications.
Pros and Cons: The main advantage of plastics is their low weight and cost-effectiveness, making them ideal for mass production. However, they may not offer the same mechanical strength as metals and can be less durable under extreme conditions. Additionally, the manufacturing process for high-quality plastics can be complex.
Impact on Application: Plastics are highly resistant to corrosion and are compatible with a wide range of chemicals, making them suitable for applications in the automotive and chemical industries. Buyers should verify that the plastics used comply with relevant standards, such as ISO 9001 for quality management.
What Role Does Titanium Play in Spare Parts Applications?
Titanium is known for its exceptional strength-to-weight ratio and outstanding corrosion resistance, particularly in aggressive environments. It can withstand high temperatures and pressures, making it suitable for aerospace and medical applications.
Pros and Cons: The primary advantage of titanium is its durability and resistance to wear and tear. However, it is one of the more expensive materials, and its manufacturing process is complex, often requiring specialized techniques such as titanium machining.
Impact on Application: Titanium is compatible with various media, including seawater, making it ideal for marine applications. Buyers should ensure compliance with standards like ASTM B348 for titanium products, particularly when sourcing from international suppliers.
Summary Table of Material Selection for Spare Parts
Material | Typical Use Case for spare parts supplier | Key Advantage | Key Disadvantage/Limitation | Relative Cost (Low/Med/High) |
---|---|---|---|---|
Aluminum | Automotive components, heat exchangers | Lightweight, corrosion-resistant | Higher cost, complex manufacturing | Medium |
Steel | Structural components, machinery parts | Strong and cost-effective | Susceptible to rust and corrosion | Low |
Plastics | Electrical housings, consumer goods | Lightweight, cost-effective | Lower mechanical strength | Low |
Titanium | Aerospace, medical implants | Exceptional strength and durability | High cost, complex manufacturing | High |
This comprehensive analysis of materials for spare parts suppliers provides international B2B buyers with actionable insights to make informed decisions based on performance, cost, and compliance with industry standards.
In-depth Look: Manufacturing Processes and Quality Assurance for spare parts supplier
What Are the Main Stages in the Manufacturing Process of Spare Parts?
The manufacturing process for spare parts involves several critical stages that ensure high-quality outputs. Understanding these stages is essential for B2B buyers who wish to source reliable components.
Material Preparation: How Is Raw Material Sourced and Processed?
The first stage in the manufacturing process is material preparation. This involves selecting the right raw materials based on the specifications required for the spare parts. Common materials include metals, plastics, and composites, each chosen for their specific properties like strength, durability, and resistance to wear.
Once the materials are selected, they undergo various treatments such as cutting, casting, or machining to prepare them for forming. Buyers should inquire about the source of these materials and any certifications they hold, as this directly impacts the quality and reliability of the spare parts produced.
What Techniques Are Used in Forming Spare Parts?
The forming stage involves shaping the prepared materials into the desired components. Common techniques include:
- Casting: Pouring molten material into molds to create complex shapes.
- Forging: Using compressive forces to shape metal into desired forms, enhancing strength.
- Machining: Removing material from a workpiece using tools to achieve precise dimensions and finishes.
Understanding these techniques can help buyers assess whether a supplier has the capability to meet specific design requirements and tolerances.
How Is the Assembly Process Managed for Spare Parts?
After forming, the assembly process combines various components into a final product. This stage may involve welding, fastening, or adhesive bonding, depending on the design of the spare part.
Effective assembly requires skilled labor and adherence to precise specifications to ensure functionality. B2B buyers should seek suppliers who utilize automated assembly lines where possible, as this can improve consistency and reduce human error.
What Finishing Techniques Are Commonly Used in Spare Parts Manufacturing?
Finishing processes enhance the appearance and performance of spare parts. Techniques such as painting, plating, and surface treatments (like anodizing) are commonly employed. These processes not only improve aesthetics but also provide additional protection against corrosion and wear.
B2B buyers should inquire about the finishing options available and the environmental regulations adhered to during these processes, particularly in regions like Europe where compliance is critical.
How Is Quality Assurance Implemented Throughout the Manufacturing Process?
Quality assurance (QA) is a cornerstone of the manufacturing process, ensuring that spare parts meet international standards and customer expectations.
Which International Standards Should B2B Buyers Be Aware Of?
For spare parts suppliers, adherence to international standards such as ISO 9001 (Quality Management Systems) is crucial. This certification demonstrates a supplier’s commitment to quality and continuous improvement. Additionally, industry-specific certifications like CE (for products sold in the European Economic Area) or API (for oil and gas equipment) may be relevant depending on the spare parts being sourced.
B2B buyers from diverse regions, including Africa, South America, the Middle East, and Europe, should ensure that their suppliers possess these certifications to mitigate risks associated with non-compliance.
What Are the Key Quality Control Checkpoints in Manufacturing?
Quality control (QC) checkpoints are vital in maintaining product integrity. Key stages include:
- Incoming Quality Control (IQC): Inspection of raw materials upon arrival to ensure they meet specifications.
- In-Process Quality Control (IPQC): Ongoing checks during the manufacturing process to catch defects early.
- Final Quality Control (FQC): Comprehensive inspection of finished products before shipment.
These checkpoints enable suppliers to identify and rectify issues at various stages, enhancing the overall quality of the spare parts produced.
How Can B2B Buyers Verify Supplier Quality Control Procedures?
For international B2B buyers, verifying a supplier’s quality control processes is essential. Here are several strategies to consider:
- Conduct Audits: Regular on-site audits can provide insights into a supplier’s manufacturing and QC practices.
- Request Quality Reports: Suppliers should be willing to share detailed reports on their QC processes, including test results and inspection outcomes.
- Engage Third-Party Inspectors: Utilizing independent inspectors to assess the quality of spare parts before shipment can add an additional layer of security.
What Testing Methods Are Commonly Used in Quality Assurance?
Testing methods play a crucial role in quality assurance for spare parts. Common methods include:
- Dimensional Inspection: Ensuring that parts meet specified dimensions and tolerances.
- Non-Destructive Testing (NDT): Techniques like ultrasonic or radiographic testing to detect internal flaws without damaging the part.
- Performance Testing: Assessing how parts perform under simulated operational conditions.
Understanding these testing methods enables B2B buyers to inquire about specific tests performed on the spare parts they intend to procure.
What Nuances Should International B2B Buyers Consider Regarding Quality Control?
When sourcing from international suppliers, B2B buyers must navigate various nuances in quality control. These include:
- Cultural Differences: Approaches to quality management may differ significantly across regions, impacting expectations and outcomes.
- Regulatory Compliance: Buyers must ensure that suppliers adhere to local and international regulations, which can vary greatly.
- Communication Barriers: Effective communication is vital for understanding quality expectations and resolving issues promptly.
By being aware of these factors, B2B buyers can foster stronger relationships with suppliers and ensure the procurement of high-quality spare parts.
In conclusion, a comprehensive understanding of manufacturing processes and quality assurance mechanisms is crucial for B2B buyers looking to source spare parts effectively. By focusing on these areas, buyers can make informed decisions that align with their quality expectations and operational needs.
Practical Sourcing Guide: A Step-by-Step Checklist for ‘spare parts supplier’
To successfully source spare parts from suppliers, especially for international B2B buyers from regions like Africa, South America, the Middle East, and Europe, it’s essential to follow a structured approach. This checklist will help you navigate the complexities of procurement while ensuring quality and reliability in your sourcing decisions.
Step 1: Define Your Technical Specifications
Before reaching out to suppliers, clearly outline the technical specifications of the spare parts you need. This includes dimensions, materials, and any compliance standards relevant to your industry. A well-defined specification helps prevent miscommunication and ensures that suppliers understand your exact requirements.
- Considerations:
- Identify the specific model numbers or part numbers.
- Include tolerances and quality standards that must be met.
Step 2: Research Potential Suppliers
Conduct thorough research to identify potential suppliers who specialize in the spare parts you require. Look for companies with a strong reputation in the industry, positive reviews, and a history of reliability.
- Where to Look:
- Industry trade shows and exhibitions.
- Online marketplaces and directories specific to your sector.
Step 3: Evaluate Supplier Certifications and Compliance
Verify that potential suppliers hold necessary certifications and comply with international quality standards such as ISO 9001. This step is crucial to ensure that the parts supplied meet your quality expectations and regulatory requirements.
- Key Certifications to Check:
- ISO certifications relevant to your industry.
- Compliance with local and international trade regulations.
Step 4: Request Samples and Prototypes
Before placing a bulk order, request samples or prototypes of the spare parts. This allows you to assess the quality and compatibility of the parts with your existing systems.
- What to Assess:
- Material quality and durability.
- Fit and performance during testing.
Step 5: Negotiate Pricing and Terms
Once you have a shortlist of suppliers, initiate negotiations on pricing, payment terms, and delivery schedules. This is a critical step to ensure that you receive competitive pricing while establishing a mutually beneficial relationship.
- Negotiation Tips:
- Be clear about your budget and expectations.
- Consider long-term partnerships for better pricing and terms.
Step 6: Check References and Past Performance
Before finalizing your choice, check references from other clients who have sourced from the supplier. This will give you insights into their reliability, customer service, and delivery timelines.
- What to Ask:
- Inquire about the supplier’s ability to meet deadlines.
- Ask about any issues encountered during the procurement process.
Step 7: Establish Clear Communication Channels
Finally, establish clear communication channels with your selected supplier. Effective communication is vital for resolving issues quickly and ensuring a smooth procurement process.
- Recommended Practices:
- Set regular check-ins for updates on order status.
- Use project management tools to track progress and timelines.
Following this practical sourcing guide will help international B2B buyers confidently procure spare parts, reducing risks and ensuring quality in their supply chain.
Comprehensive Cost and Pricing Analysis for spare parts supplier Sourcing
What Are the Key Cost Components in Spare Parts Supplier Sourcing?
Understanding the cost structure of spare parts suppliers is essential for international B2B buyers aiming for effective procurement strategies. The primary cost components include:
-
Materials: This is often the most significant expense. The choice of raw materials can vary greatly in price depending on quality and availability. Buyers should consider sourcing materials locally to mitigate costs, especially in regions like Africa and South America where logistics can inflate prices.
-
Labor: Labor costs vary by region and can influence the overall pricing of spare parts. In countries with lower labor costs, such as certain parts of Africa, suppliers may offer competitive pricing. However, consider the potential trade-offs in quality and reliability.
-
Manufacturing Overhead: This encompasses expenses related to the production facility, utilities, and administrative costs. Efficient manufacturing processes can help reduce overhead, thereby lowering prices for buyers.
-
Tooling: The initial investment in tooling can be substantial, particularly for custom parts. Buyers should inquire about tooling costs if they require unique specifications, as these can significantly affect the unit price.
-
Quality Control (QC): Ensuring high-quality standards often involves additional costs. Suppliers who adhere to international certifications (like ISO) may charge more but can provide assurance of quality, which is crucial for critical applications.
-
Logistics: Shipping and handling costs can vary significantly based on the distance and mode of transport. International buyers should factor in potential tariffs and customs duties, especially when importing from regions like Europe or the Middle East.
-
Margin: Finally, suppliers need to maintain a profit margin. Understanding the supplier’s pricing strategy can aid in negotiations, particularly if the buyer can commit to larger order volumes.
How Do Price Influencers Affect Spare Parts Procurement?
Several factors can influence the pricing of spare parts, including:
-
Volume/MOQ: Minimum order quantities (MOQ) often dictate pricing. Buyers who can purchase in bulk may negotiate better rates, effectively lowering their per-unit cost.
-
Specifications and Customization: Customized parts usually come at a premium. Buyers should evaluate whether custom specifications are essential or if standard parts would suffice, potentially saving costs.
-
Materials and Quality Certifications: High-quality materials and certifications can increase costs but may lead to long-term savings through enhanced durability and lower failure rates.
-
Supplier Factors: The supplier’s reputation, reliability, and location can all impact pricing. Suppliers in regions with stable economies may offer more consistent pricing than those in volatile markets.
-
Incoterms: Understanding Incoterms is crucial for international transactions. They define the responsibilities of buyers and sellers regarding shipping, insurance, and tariffs, which can affect overall costs.
What Are the Best Buyer Tips for Negotiating Spare Parts Prices?
-
Leverage Total Cost of Ownership (TCO): Instead of focusing solely on the purchase price, consider the TCO, which includes maintenance, logistics, and disposal costs. A higher upfront price may be justified if it leads to lower long-term costs.
-
Negotiate Effectively: Don’t hesitate to negotiate on price, especially if you can demonstrate your purchasing potential or commitment to a long-term partnership. Highlighting your position as a repeat buyer can strengthen your negotiating power.
-
Assess Cost-Efficiency: Regularly review supplier costs and performance. Benchmark against industry standards to ensure you are receiving competitive pricing. This is particularly important for buyers in emerging markets like Nigeria or Brazil, where pricing can fluctuate significantly.
-
Understand Pricing Nuances: Be aware of local market conditions, currency fluctuations, and geopolitical factors that can influence pricing. This knowledge can provide leverage in negotiations and help avoid unexpected price increases.
-
Engage Multiple Suppliers: Diversifying your supplier base can create competitive tension, leading to better pricing and service levels. Evaluate multiple suppliers across different regions to find the best fit for your needs.
Disclaimer on Indicative Prices
Prices in the spare parts industry can vary widely based on numerous factors, including market conditions, supplier capabilities, and specific buyer requirements. Always conduct thorough due diligence and seek multiple quotes to ensure the best pricing for your procurement needs.
Alternatives Analysis: Comparing spare parts supplier With Other Solutions
When considering spare parts suppliers, international B2B buyers should evaluate various alternative solutions that can fulfill their operational needs. These alternatives might offer different advantages and drawbacks depending on the business context, budget, and logistical capabilities. Below, we compare spare parts suppliers with two viable alternatives: in-house manufacturing and 3D printing.
Comparison Aspect | Spare Parts Supplier | In-house Manufacturing | 3D Printing |
---|---|---|---|
Performance | High quality and reliability | Variable, dependent on equipment and skill | High precision, but material limitations exist |
Cost | Moderate to high (varies by supplier) | High initial investment and ongoing operational costs | Lower initial investment, but material costs can add up |
Ease of Implementation | Generally straightforward with established suppliers | Complex setup and training required | Moderate, requires knowledge of CAD and printing processes |
Maintenance | Supplier handles maintenance | Requires in-house maintenance teams | Minimal maintenance, but requires skill updates |
Best Use Case | Large-scale operations needing consistent supply | Custom parts or high-volume production | Prototyping or low-volume, customized parts |
What Are the Advantages and Disadvantages of In-house Manufacturing?
In-house manufacturing allows companies to produce spare parts tailored to their specific needs. This can lead to better quality control and rapid prototyping capabilities. However, the initial investment is considerable, requiring advanced machinery and skilled labor. Over time, operating costs can also rise due to maintenance and staffing. For businesses with steady demand for specific parts, this may be a viable long-term solution, but it requires a significant commitment to infrastructure and training.
How Does 3D Printing Compare to Spare Parts Suppliers?
3D printing has revolutionized the production of spare parts by enabling rapid prototyping and customization. It allows businesses to produce complex geometries that traditional methods cannot easily achieve. The initial investment for a 3D printer can be lower than that of a full manufacturing setup, and it requires less space. However, material choices can be limited, and the strength of printed parts may not always meet industrial standards. Thus, while 3D printing is excellent for prototyping and low-volume production, it may not replace the reliability offered by traditional spare parts suppliers for high-demand applications.
Conclusion: How Can B2B Buyers Choose the Right Solution?
Choosing between a spare parts supplier, in-house manufacturing, or 3D printing depends on various factors such as budget, production volume, and the specific needs of the business. Buyers should assess their operational requirements, including the frequency of part replacement, customization needs, and budget constraints. For companies in regions such as Africa, South America, the Middle East, and Europe, where supply chain dynamics can vary, establishing relationships with reliable suppliers or investing in in-house capabilities may provide strategic advantages. Ultimately, the right choice will align with the company’s long-term goals and operational strategy.
Essential Technical Properties and Trade Terminology for spare parts supplier
What Are the Key Technical Properties for Spare Parts Suppliers?
When sourcing spare parts, understanding specific technical properties is crucial for ensuring compatibility, reliability, and performance. Here are some essential specifications to consider:
-
Material Grade
The material grade defines the quality and durability of the spare part. Common materials include metals (like steel or aluminum), plastics, and composites. Selecting the right material grade is vital for applications that require high strength, corrosion resistance, or thermal stability. For instance, in automotive applications, using high-grade steel can prevent failure under stress, enhancing the lifespan of the part. -
Tolerance
Tolerance refers to the permissible limit of variation in a physical dimension. It is crucial for ensuring that spare parts fit correctly within a system. Tight tolerances are often necessary in precision engineering applications, such as machinery parts. Understanding tolerance levels helps buyers ensure that the parts will function properly, reducing the risk of malfunction or damage. -
Surface Finish
The surface finish of a spare part affects its performance and durability. A smoother finish can reduce friction and wear, while a rougher finish may be beneficial for specific applications, such as enhancing adhesion or reducing glare. Knowledge of surface finish requirements can help buyers select parts that will perform optimally in their intended environments. -
Load Capacity
This specification indicates the maximum load a spare part can handle without failure. It is especially important in structural applications where parts must support weight or endure stress. Buyers must match the load capacity of spare parts with their operational demands to avoid catastrophic failures. -
Operating Temperature Range
This property defines the temperature limits within which a spare part can function effectively. It is particularly relevant in industries like automotive and aerospace, where parts are exposed to extreme temperatures. Ensuring that spare parts can operate within the required temperature range prevents premature wear and failure. -
Corrosion Resistance
Corrosion resistance is critical for parts used in harsh environments, such as marine or industrial applications. Understanding the corrosion resistance of materials helps buyers choose parts that will maintain their integrity over time, thereby reducing maintenance costs and downtime.
Which Trade Terms Should B2B Buyers Understand When Sourcing Spare Parts?
Familiarity with industry jargon is essential for effective communication and negotiation in the spare parts supply chain. Here are some common terms:
-
OEM (Original Equipment Manufacturer)
OEM refers to companies that produce parts that are used in the manufacturing of a product. For buyers, sourcing OEM parts can ensure compatibility and quality, as these parts are designed to meet the original specifications. -
MOQ (Minimum Order Quantity)
MOQ is the smallest quantity of a product that a supplier is willing to sell. Understanding MOQ is crucial for buyers to manage inventory costs and ensure they are not overcommitting to a supplier. -
RFQ (Request for Quotation)
An RFQ is a formal document sent to suppliers requesting a price quote for specific spare parts. This process allows buyers to compare prices and terms, ensuring they secure the best deal. -
Incoterms (International Commercial Terms)
Incoterms are standardized trade terms that clarify the responsibilities of buyers and sellers in international transactions. Familiarity with these terms helps buyers understand shipping, insurance, and delivery responsibilities, which can impact overall costs. -
Lead Time
Lead time refers to the amount of time it takes from placing an order to receiving the goods. Understanding lead times is essential for planning and ensuring that operations are not disrupted due to delays in receiving spare parts. -
Warranty
A warranty is a guarantee provided by the supplier regarding the quality and performance of a spare part. Knowing the warranty terms can protect buyers against defects and provide assurance of product reliability.
Conclusion
For international B2B buyers, particularly those in regions like Africa, South America, the Middle East, and Europe, understanding these technical properties and trade terms is essential for making informed purchasing decisions. Proper knowledge not only facilitates better negotiation with suppliers but also ensures that the spare parts sourced meet operational requirements and standards.
Navigating Market Dynamics and Sourcing Trends in the spare parts supplier Sector
What Are the Current Market Dynamics and Key Trends in the Spare Parts Supplier Sector?
The spare parts supplier sector is undergoing significant transformation driven by globalization, technological advancements, and changing consumer expectations. For international B2B buyers from regions such as Africa, South America, the Middle East, and Europe, understanding these dynamics is crucial for effective sourcing.
Global Drivers: The demand for spare parts is being propelled by the increasing longevity of machinery and vehicles, as well as the rise of the circular economy. As manufacturers emphasize sustainability, the need for durable, repairable, and replaceable parts is growing. Additionally, geopolitical factors and trade agreements have led to shifts in sourcing strategies, where companies are looking for local suppliers to mitigate risks associated with global supply chains.
Emerging B2B Tech Trends: Digital transformation is at the forefront, with technologies such as Artificial Intelligence (AI) and the Internet of Things (IoT) enhancing inventory management and predictive maintenance. Buyers are increasingly leveraging data analytics to forecast demand and optimize procurement strategies. E-commerce platforms for B2B transactions are becoming more prevalent, allowing buyers from diverse regions to access a wider range of suppliers and parts.
Market Dynamics for Buyers: The competitive landscape is becoming more fragmented, with both established players and new entrants vying for market share. This has led to increased pricing pressure and a focus on value-added services. Buyers should prioritize suppliers who demonstrate flexibility, innovation, and strong after-sales support to navigate these dynamics successfully.
How Can Sustainability and Ethical Sourcing Impact Your Spare Parts Procurement?
The importance of sustainability and ethical sourcing in the spare parts supplier sector cannot be overstated. As environmental regulations tighten globally, buyers are increasingly held accountable for the environmental impact of their procurement choices.
Environmental Impact: The production and disposal of spare parts contribute significantly to waste and pollution. By choosing suppliers who prioritize sustainable practices—such as using recyclable materials and minimizing waste—buyers can reduce their carbon footprint. Additionally, adopting circular economy principles, like remanufacturing and refurbishing parts, can lead to substantial cost savings and waste reduction.
Importance of Ethical Supply Chains: Ethical sourcing ensures that suppliers adhere to fair labor practices and environmental standards. Buyers should conduct due diligence to verify the ethical credentials of their suppliers. This not only mitigates risks associated with reputational damage but also aligns with the growing consumer demand for transparency and corporate responsibility.
‘Green’ Certifications and Materials: Look for suppliers who offer eco-friendly certifications, such as ISO 14001 for environmental management or those that comply with RoHS (Restriction of Hazardous Substances) directives. Using certified ‘green’ materials can enhance a buyer’s brand reputation while also contributing to a more sustainable supply chain.
What Is the Evolution of the Spare Parts Supplier Sector?
The spare parts supplier sector has evolved significantly over the decades, shaped by technological advancements and changes in consumer behavior. Historically, the industry was characterized by a fragmented market with local suppliers dominating the landscape. However, globalization and advancements in logistics have enabled a shift towards a more interconnected marketplace.
In the late 20th century, the rise of digital technologies began to transform the sector, paving the way for e-commerce and online marketplaces. This evolution has enabled buyers to access a wider variety of spare parts from global suppliers, enhancing competition and driving innovation.
Today, the sector is on the cusp of a new era characterized by smart technologies and sustainable practices, fundamentally changing how spare parts are sourced and supplied. Buyers must stay informed about these changes to leverage opportunities and mitigate risks in their procurement strategies.
Frequently Asked Questions (FAQs) for B2B Buyers of spare parts supplier
-
How do I choose the right spare parts supplier for my business needs?
When selecting a spare parts supplier, prioritize their industry experience and reputation. Look for suppliers who specialize in your specific sector, whether it’s automotive, industrial machinery, or electronics. Request references and check online reviews to gauge their reliability. Additionally, consider their ability to provide customization options, lead times, and after-sales support. Building a relationship with a supplier that understands your unique requirements can lead to better service and pricing. -
What factors should I consider when evaluating the quality of spare parts?
Assess the quality of spare parts by checking for certifications and compliance with industry standards. Request product samples to evaluate materials and craftsmanship. A reputable supplier should provide detailed specifications and testing reports. Consider the supplier’s quality assurance processes, such as inspections and testing protocols, to ensure that the parts meet your operational requirements. Regular communication about quality issues can also help maintain standards. -
What are the common payment terms offered by spare parts suppliers?
Payment terms can vary significantly among suppliers. Common options include net 30, net 60, or payment upon delivery. Some suppliers may offer discounts for early payments or require deposits for large orders. It’s essential to negotiate terms that align with your cash flow and procurement strategy. Always clarify payment methods accepted, such as wire transfers or credit terms, to avoid any misunderstandings during the transaction process.
-
How can I negotiate better pricing with spare parts suppliers?
To negotiate better pricing, conduct market research to understand the going rates for the spare parts you need. Establish a long-term relationship with your supplier, which can lead to bulk discounts or loyalty rewards. Be transparent about your budget constraints and inquire about any available promotions or seasonal discounts. Additionally, consider consolidating your orders to achieve volume discounts, thereby reducing overall costs. -
What is the minimum order quantity (MOQ) for spare parts, and how does it affect my purchasing strategy?
The MOQ refers to the smallest quantity a supplier will sell. Understanding MOQs is crucial for managing your inventory effectively and ensuring cost-efficiency. Suppliers often set MOQs to cover production costs, so inquire if they can provide flexibility for smaller orders or if they offer a tiered pricing structure based on order size. Aligning your purchasing strategy with MOQs can help optimize cash flow and minimize excess inventory. -
How do I ensure timely delivery of spare parts from international suppliers?
To ensure timely delivery, establish clear timelines with your supplier and agree on delivery schedules upfront. Utilize reliable logistics partners and consider working with suppliers who have experience with international shipping regulations and customs procedures. Regular communication with your supplier about shipment status and potential delays can help manage expectations. Additionally, consider using Incoterms that clarify responsibilities for shipping and delivery. -
What should I know about customs and import regulations when sourcing spare parts internationally?
Familiarize yourself with customs regulations in your country, including tariffs, import duties, and necessary documentation such as invoices and certificates of origin. It’s advisable to work with a customs broker who can navigate the complexities of international trade and ensure compliance. Understanding the regulatory landscape can help avoid delays and additional costs during the import process, ensuring a smoother supply chain. -
Can I customize spare parts to meet specific operational needs?
Many suppliers offer customization options for spare parts, which can include modifications in design, materials, or specifications to suit your operational requirements. Discuss your specific needs with potential suppliers and inquire about their capabilities for custom manufacturing. Be prepared to provide detailed specifications and timelines for development. Customization can enhance the performance and compatibility of parts with your existing systems, leading to improved efficiency.
Important Disclaimer & Terms of Use
⚠️ Important Disclaimer
The information provided in this guide, including content regarding manufacturers, technical specifications, and market analysis, is for informational and educational purposes only. It does not constitute professional procurement advice, financial advice, or legal advice.
While we have made every effort to ensure the accuracy and timeliness of the information, we are not responsible for any errors, omissions, or outdated information. Market conditions, company details, and technical standards are subject to change.
B2B buyers must conduct their own independent and thorough due diligence before making any purchasing decisions. This includes contacting suppliers directly, verifying certifications, requesting samples, and seeking professional consultation. The risk of relying on any information in this guide is borne solely by the reader.
Strategic Sourcing Conclusion and Outlook for spare parts supplier
In today’s global market, strategic sourcing for spare parts is not just a necessity but a competitive advantage. B2B buyers from Africa, South America, the Middle East, and Europe must prioritize partnerships with reliable suppliers who understand local market dynamics and can deliver quality products on time. Key takeaways include the importance of evaluating suppliers based on their track record, technological capabilities, and adaptability to shifting market demands.
By embracing strategic sourcing, companies can reduce costs, enhance supply chain resilience, and improve product availability. This approach enables businesses to not only respond to immediate needs but also to anticipate future challenges, ensuring sustained operational efficiency.
As we look ahead, international buyers are encouraged to leverage digital platforms and tools that facilitate better communication and procurement processes. By fostering strong relationships with suppliers and continuously exploring innovative sourcing strategies, businesses can position themselves for growth and success in an increasingly interconnected world. Now is the time to take action—evaluate your sourcing strategy, engage with diverse suppliers, and invest in the future of your supply chain.