Unlock Savings: Your Guide to Accessories Supplier (2025)
Introduction: Navigating the Global Market for accessories supplier
In today’s interconnected world, sourcing high-quality accessories from reliable suppliers poses a significant challenge for international B2B buyers, especially those operating in diverse markets across Africa, South America, the Middle East, and Europe. Whether you are looking to procure smartphone cases, smart home devices, or specialized equipment, understanding the intricacies of the global market for accessories suppliers is essential. This guide aims to demystify the process by providing a comprehensive overview of the types of accessories available, their applications across various industries, and practical tips for supplier vetting.
Navigating the complexities of sourcing can be daunting, particularly when balancing cost considerations with quality and compliance. This guide empowers B2B buyers to make informed purchasing decisions by exploring critical factors such as market trends, supplier reliability, pricing structures, and logistics. Furthermore, it highlights the importance of cultural nuances and regional preferences that can influence buyer-supplier relationships.
By leveraging the insights provided in this guide, international buyers can streamline their sourcing processes, mitigate risks, and establish long-term partnerships with trustworthy suppliers. Whether you are based in Thailand, Colombia, or any other emerging market, understanding the global landscape of accessory suppliers will enable you to capitalize on opportunities and drive business growth effectively.
Understanding accessories supplier Types and Variations
Type Name | Key Distinguishing Features | Primary B2B Applications | Brief Pros & Cons for Buyers |
---|---|---|---|
OEM (Original Equipment Manufacturer) | Produces accessories that are specifically designed for original products. | Electronics, automotive, and consumer goods. | Pros: High compatibility; Cons: Typically higher costs. |
Aftermarket Suppliers | Provides accessories that are compatible but not made by the original brand. | Replacement parts, upgrades, and enhancements. | Pros: Cost-effective; Cons: Varying quality and compatibility. |
Custom Accessories Manufacturers | Specializes in tailored solutions for specific business needs. | Niche markets, promotional items, and corporate gifts. | Pros: Unique offerings; Cons: Longer lead times and potentially higher costs. |
Wholesale Distributors | Acts as a middleman, purchasing large quantities from manufacturers and selling to retailers. | Retail and e-commerce businesses. | Pros: Bulk pricing; Cons: Less control over product quality. |
E-commerce Platforms | Online marketplaces that connect buyers with various accessory suppliers. | Diverse industries, especially retail. | Pros: Wide selection; Cons: Quality assurance can be challenging. |
What are OEM Suppliers and How Do They Benefit B2B Buyers?
OEM suppliers are known for producing accessories specifically designed to fit original products. They are essential for industries such as electronics and automotive, where precise compatibility is paramount. B2B buyers often choose OEM products for their reliability and assurance of quality, although they may come at a premium price. When selecting an OEM supplier, businesses should consider the supplier’s reputation, warranty offerings, and support services.
How Do Aftermarket Suppliers Differ in the Accessories Market?
Aftermarket suppliers provide accessories that are compatible with original products but are not manufactured by the original brand. This option is particularly attractive for businesses looking for cost-effective alternatives for replacement parts or upgrades. However, buyers must be cautious about the varying quality and compatibility of these products. Conducting thorough research and requesting samples can help mitigate risks associated with aftermarket purchases.
Why Choose Custom Accessories Manufacturers?
Custom accessories manufacturers focus on creating tailored solutions that meet specific business requirements. These suppliers are ideal for niche markets or promotional items where uniqueness is key. While the benefits include distinctive offerings that can enhance brand identity, buyers should be prepared for longer lead times and potentially higher costs. It’s crucial for B2B buyers to communicate their needs clearly to ensure the final product aligns with their expectations.
What Role Do Wholesale Distributors Play in the Accessories Supply Chain?
Wholesale distributors act as intermediaries between manufacturers and retailers, purchasing large quantities of accessories and selling them to businesses. They are particularly beneficial for retail and e-commerce companies looking to stock a variety of products at bulk pricing. However, buyers may have less control over product quality and should establish strong relationships with distributors to ensure consistent standards.
How Do E-commerce Platforms Enhance Access to Accessories?
E-commerce platforms serve as online marketplaces that connect buyers with a wide range of accessory suppliers. This model offers B2B buyers access to a diverse selection of products across various industries, making it easier to compare prices and features. However, the challenge lies in ensuring quality assurance, as products can vary significantly. Buyers should look for platforms that offer customer reviews and ratings to aid their purchasing decisions.
Related Video: Electrical Fitting Name & Pictures | Electrical Materials Name | Electrical Accessories List
Key Industrial Applications of accessories supplier
Industry/Sector | Specific Application of Accessories Supplier | Value/Benefit for the Business | Key Sourcing Considerations for this Application |
---|---|---|---|
Consumer Electronics | Mobile Device Accessories (cases, chargers, etc.) | Enhances product usability and protection | Quality standards, compatibility with various models, lead time |
Smart Home Technology | Smart Home Devices (sensors, cameras, etc.) | Increases customer engagement and satisfaction | Integration capabilities, local regulations, customer support |
Health & Fitness | Wearable Technology Accessories (bands, chargers) | Promotes health tracking and user convenience | Durability, comfort, and compatibility with existing devices |
Automotive | Vehicle Accessories (dash cams, phone mounts) | Improves driver safety and convenience | Compliance with safety regulations, compatibility with models |
Creative Industries | Photography Accessories (tripods, lights) | Enhances creative output and productivity | Versatility, portability, and ease of use for professionals |
What Are the Key Applications of Accessories Suppliers in Consumer Electronics?
In the consumer electronics sector, accessories suppliers play a crucial role by providing mobile device accessories such as cases, chargers, and screen protectors. These accessories not only enhance the usability of devices but also provide essential protection against wear and tear. For international B2B buyers, especially in regions like Africa and South America, sourcing high-quality and compatible accessories is vital to meet local consumer expectations and ensure product longevity. Buyers should prioritize suppliers that adhere to quality standards and can guarantee timely delivery to maintain inventory levels.
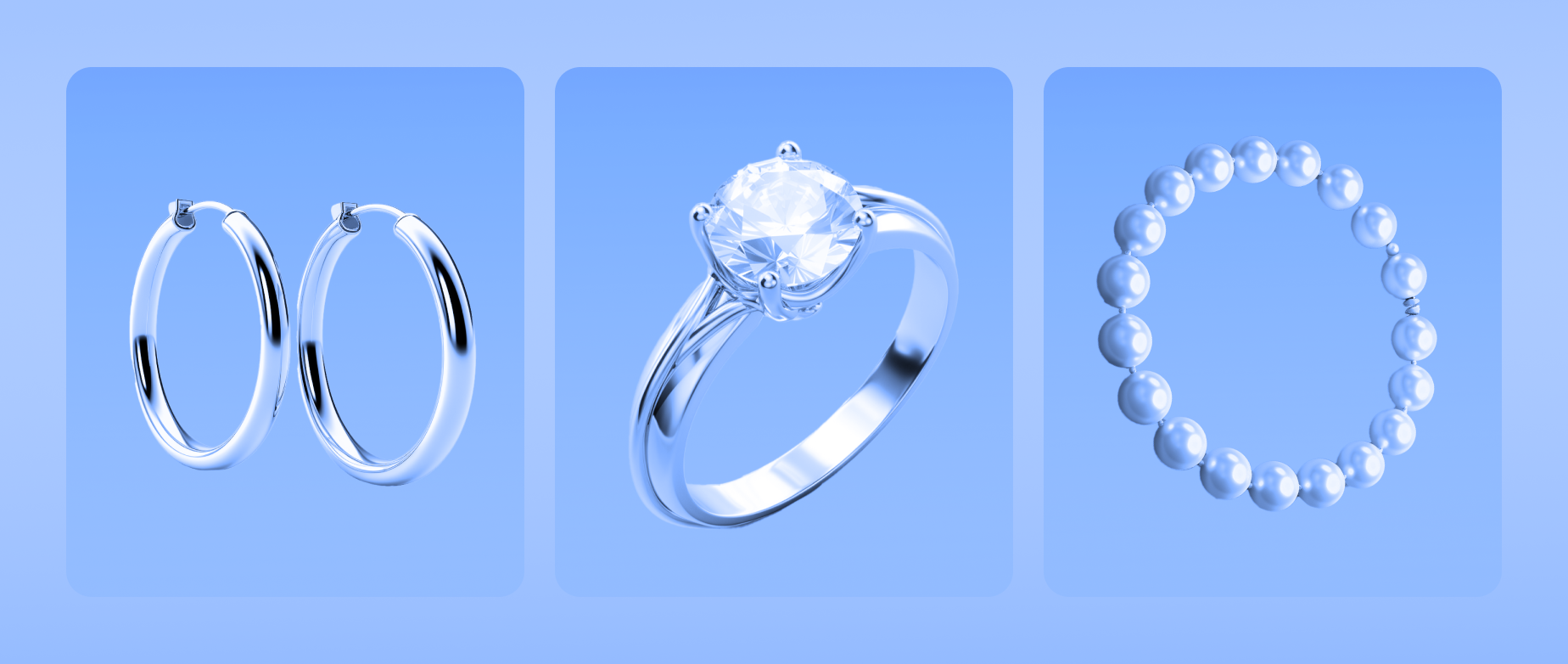
A stock image related to accessories supplier.
How Do Accessories Suppliers Enhance Smart Home Technology?
Smart home technology relies heavily on accessories suppliers for devices like sensors, cameras, and smart plugs. These accessories improve customer engagement by offering enhanced functionalities that promote convenience and security in daily life. For businesses in the Middle East and Europe, understanding local regulations and integration capabilities is essential when sourcing these products. Buyers should consider suppliers that offer robust customer support and can provide integration assistance to ensure seamless operation within existing smart home ecosystems.
What Role Do Accessories Suppliers Play in Health & Fitness?
In the health and fitness industry, accessories suppliers provide wearable technology accessories, including fitness bands and chargers. These accessories are designed to promote user convenience and encourage regular health tracking. For B2B buyers, especially in regions like Africa, sourcing durable and comfortable accessories is essential to meet the needs of health-conscious consumers. Suppliers should be evaluated based on their ability to deliver products that are compatible with various wearable devices and offer reliable performance.
How Are Accessories Suppliers Beneficial in the Automotive Sector?
In the automotive industry, accessories suppliers offer products such as dash cams, phone mounts, and safety gadgets. These accessories enhance driver safety and convenience while on the road. For international buyers in South America and Europe, it’s crucial to source products that comply with local safety regulations and are compatible with a variety of vehicle models. Buyers should focus on suppliers who provide detailed specifications and have a proven track record in the automotive sector to ensure product reliability.
What Advantages Do Accessories Suppliers Provide to Creative Industries?
Accessories suppliers significantly benefit the creative industries by offering photography accessories like tripods, lighting equipment, and camera bags. These products enhance the creative output and productivity of professionals in fields such as photography and videography. For B2B buyers in Europe and Africa, sourcing versatile and portable accessories is key to meeting the demands of various creative projects. Suppliers should be assessed based on the quality of their products, ease of use, and the ability to support creative professionals with innovative solutions.
3 Common User Pain Points for ‘accessories supplier’ & Their Solutions
Scenario 1: Difficulty in Sourcing Quality Accessories
The Problem:
B2B buyers often struggle with sourcing high-quality accessories that meet their specific business needs. This is particularly true for companies in Africa and South America, where local suppliers may offer limited options or inferior products. Inconsistent quality can lead to dissatisfaction among end-users, damage a company’s reputation, and result in increased returns or exchanges. Additionally, navigating international suppliers can be challenging due to language barriers, different quality standards, and varying regulations.
The Solution:
To effectively source quality accessories, B2B buyers should conduct thorough market research to identify reputable suppliers with a proven track record. Utilize platforms like Alibaba or Global Sources to find suppliers with high ratings and positive reviews. It’s essential to request samples before making bulk orders to assess the quality firsthand. Furthermore, establishing clear communication with suppliers about quality standards and certifications is crucial. Buyers should also consider working with local agents or intermediaries who understand the regional market dynamics and can facilitate smoother transactions.
Scenario 2: Managing Inventory and Supply Chain Challenges
The Problem:
Another prevalent pain point for B2B buyers is managing inventory and supply chain logistics. Many businesses face issues with stockouts or overstocking due to inaccurate demand forecasting or delays in shipment. This is particularly challenging in regions like the Middle East and Europe, where demand can fluctuate rapidly based on trends and seasons. Inconsistent supply chains can lead to missed sales opportunities and increased operational costs.
The Solution:
Implementing a robust inventory management system can significantly alleviate these issues. Buyers should utilize software that integrates with their existing ERP systems to track inventory levels in real-time and forecast demand more accurately. Additionally, establishing strong relationships with multiple suppliers can provide flexibility and reduce the risk of stockouts. Regularly reviewing and adjusting order quantities based on sales data and market trends is essential. Moreover, working closely with logistics partners to optimize shipping routes and timelines can enhance supply chain efficiency, ensuring that products are available when needed without incurring excess inventory costs.
Scenario 3: Navigating Regulatory Compliance and Import Challenges
The Problem:
B2B buyers often encounter challenges related to regulatory compliance and import restrictions, especially when dealing with accessories from different countries. These challenges can include tariffs, safety standards, and import quotas, which can complicate the purchasing process and lead to unexpected costs or delays. Buyers in Europe, for instance, must comply with stringent EU regulations, while those in Africa may face varying import policies across different countries.
The Solution:
To navigate these complexities, buyers should invest time in understanding the regulatory landscape of their target markets. Consulting with legal experts or trade compliance specialists can provide valuable insights into the specific requirements for importing accessories. Additionally, buyers should ensure that suppliers are compliant with all necessary standards and can provide relevant documentation, such as safety certifications or proof of origin. Utilizing customs brokers can also streamline the import process, reducing the risk of delays. Keeping abreast of changes in trade agreements and tariffs can help buyers adjust their strategies proactively, ensuring compliance while minimizing costs.
By addressing these common pain points with actionable solutions, B2B buyers can enhance their purchasing strategies, build stronger supplier relationships, and ultimately improve their bottom line.
Strategic Material Selection Guide for accessories supplier
What Are the Key Materials for Accessories Suppliers?
When selecting materials for accessories, suppliers must consider various factors that influence product performance, cost, and compliance with international standards. Below are analyses of four common materials used in the production of accessories, focusing on their properties, advantages, disadvantages, and considerations for international B2B buyers.
How Does Plastic Perform in Accessory Manufacturing?
Key Properties:
Plastic is lightweight, versatile, and resistant to moisture, making it suitable for a wide range of applications. It can withstand moderate temperatures and is often used in consumer electronic accessories.
Pros & Cons:
The durability of plastic varies depending on the type (e.g., ABS, polycarbonate), but it generally offers good impact resistance. However, it can be prone to scratches and may not withstand high temperatures. Manufacturing complexity is relatively low, leading to lower costs.
Impact on Application:
Plastic is compatible with various media, including water and air, but it can degrade under UV exposure. Buyers should consider the specific environmental conditions in their regions, such as high humidity in tropical climates.
Considerations for International Buyers:
Plastic materials must comply with regulations such as REACH in Europe and similar standards in South America and Africa. Buyers should ensure that suppliers provide certifications that confirm compliance with local and international standards.
What Advantages Does Metal Offer for Accessories?
Key Properties:
Metals such as aluminum and stainless steel are known for their strength, corrosion resistance, and high-temperature tolerance. They are often used in high-end accessories where durability is paramount.
Pros & Cons:
While metals provide excellent durability and a premium feel, they are generally heavier and more expensive than plastics. Manufacturing processes for metal can be complex, often requiring specialized equipment, which can increase costs.
Impact on Application:
Metals are suitable for applications requiring structural integrity, such as mounts or casings for electronics. However, they may not be ideal for environments with high moisture unless adequately treated or coated.
Considerations for International Buyers:
International buyers should be aware of the varying standards for metal products, such as ASTM in the U.S. and DIN in Europe. Additionally, they should consider the environmental impact of metal extraction and processing, which may influence purchasing decisions in regions focused on sustainability.
How Do Textiles Enhance Accessories?
Key Properties:
Textiles, including cotton, polyester, and nylon, offer flexibility, comfort, and aesthetic appeal. They are particularly useful in accessories like bags, straps, and cases.
Pros & Cons:
While textiles can be lightweight and customizable, they may not offer the same durability as plastics or metals. They can be susceptible to wear and tear, especially in high-friction applications. The manufacturing process can vary significantly in complexity, affecting costs.
Impact on Application:
Textiles are generally compatible with a range of media but may absorb moisture, which can lead to degradation over time. Buyers should consider the specific use case and environmental conditions to select the appropriate textile.
Considerations for International Buyers:
Textiles must meet various safety and environmental regulations, particularly regarding flammability and chemical treatments. International buyers should verify compliance with local standards and consumer preferences, which can vary greatly across regions.
What Role Does Glass Play in Accessory Design?
Key Properties:
Glass is often used in high-end accessories for its aesthetic appeal and scratch resistance. It can withstand high temperatures and is chemically stable.
Pros & Cons:
While glass offers a premium look and feel, it is fragile and can break easily under impact. The manufacturing process can be complex and costly, making glass accessories more expensive.
Impact on Application:
Glass is suitable for applications requiring transparency and aesthetic appeal, such as display cases or decorative elements. However, its fragility limits its use in rugged environments.
Considerations for International Buyers:
Buyers should consider the shipping and handling requirements for glass products, as they are more prone to damage during transport. Compliance with safety standards, such as those regarding shatter resistance, is also crucial.
Summary of Material Selection for Accessories Suppliers
Material | Typical Use Case for Accessories Supplier | Key Advantage | Key Disadvantage/Limitation | Relative Cost (Low/Med/High) |
---|---|---|---|---|
Plastic | Phone cases, straps | Lightweight and versatile | Prone to scratches | Low |
Metal | High-end mounts, casings | Excellent durability | Heavier and more expensive | High |
Textile | Bags, straps, cases | Flexible and customizable | Less durable than plastics/metals | Medium |
Glass | Decorative elements, display cases | Premium look and feel | Fragile and costly | High |
This guide provides a comprehensive overview of material selection for accessories suppliers, emphasizing the importance of understanding each material’s properties and implications for international B2B buyers.
In-depth Look: Manufacturing Processes and Quality Assurance for accessories supplier
What Are the Main Stages of Manufacturing for Accessories Suppliers?
The manufacturing process for accessories involves several critical stages, each designed to ensure the final product meets quality standards and customer expectations. Understanding these stages can help B2B buyers make informed decisions when selecting suppliers.
1. Material Preparation: Sourcing and Quality Control
The first step in the manufacturing process is material preparation. Suppliers must source high-quality raw materials that comply with international standards. This stage often includes:
- Supplier Selection: Choose suppliers who are certified and have a track record of reliability. Look for certifications such as ISO 9001, which indicates adherence to quality management systems.
- Material Inspection: Conduct Incoming Quality Control (IQC) to verify the quality of materials before they enter the production line. This can involve checking for defects, dimensions, and compliance with specifications.
2. Forming: Techniques Used in Manufacturing Accessories
Once materials are prepared, the next stage is forming. This involves converting raw materials into specific shapes and forms required for the accessories. Key techniques include:
- Injection Molding: Commonly used for plastic accessories, this technique allows for high-volume production with precision and consistency.
- Die Casting: Often used for metal parts, die casting provides intricate designs and reduces waste.
- 3D Printing: Gaining popularity for custom accessories, 3D printing allows for rapid prototyping and flexibility in design.
These techniques must be carefully monitored to ensure that they meet both the design specifications and the quality standards expected by international buyers.
3. Assembly: Ensuring Proper Functionality and Aesthetics
Assembly is where various components are brought together to create the final product. This stage typically includes:
- Manual Assembly: Skilled workers assemble parts, ensuring attention to detail and quality.
- Automated Assembly: Robots can be used for repetitive tasks, increasing efficiency and consistency.
- Quality Checks: In-Process Quality Control (IPQC) is crucial during assembly. This involves regular checks to identify any defects before the product moves to the next stage.
4. Finishing: Final Touches and Quality Assurance
The finishing stage involves adding any final touches to the accessories, including surface treatments, painting, or coating. This stage is essential for both aesthetics and durability. Key aspects include:
- Surface Treatment: Techniques like anodizing, painting, or polishing enhance the product’s appearance and protect it from wear.
- Final Quality Control: Final Quality Control (FQC) inspections ensure that products meet all specifications before they are packaged and shipped. This can include functionality tests, dimensional checks, and visual inspections.
How Do International Standards Impact Quality Assurance in Accessory Manufacturing?
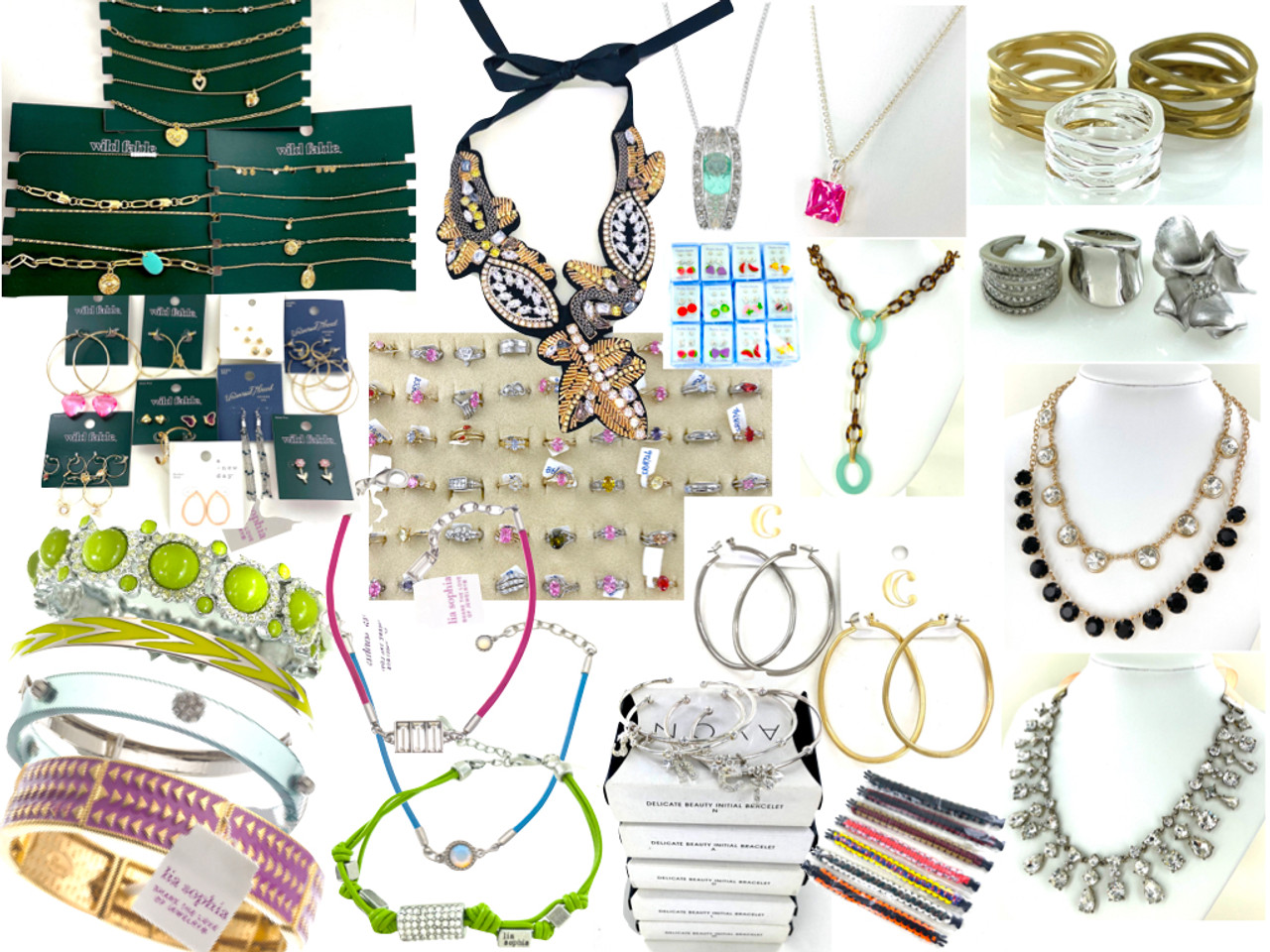
A stock image related to accessories supplier.
Quality assurance is a critical component of the manufacturing process, especially for international B2B buyers who require consistent quality across borders. Understanding the relevant standards is essential.
What Are the Key International Standards for Quality Assurance?
- ISO 9001: This standard focuses on quality management systems and is essential for suppliers aiming to meet international quality benchmarks. It ensures that processes are standardized and continuously improved.
- CE Marking: For products sold in Europe, CE marking indicates conformity with health, safety, and environmental protection standards. Suppliers must ensure their products meet these requirements to avoid penalties and ensure market access.
- API Certification: In certain industries, such as oil and gas, API standards ensure that products meet rigorous safety and performance criteria.
What Are the Quality Control Checkpoints in the Manufacturing Process?
Quality control checkpoints are vital for maintaining product quality throughout the manufacturing process. B2B buyers should be aware of the following checkpoints:
- Incoming Quality Control (IQC): At this stage, raw materials are inspected for quality before they enter the manufacturing process.
- In-Process Quality Control (IPQC): Regular checks during manufacturing help identify defects early, reducing waste and ensuring consistency.
- Final Quality Control (FQC): Comprehensive checks before shipment ensure that the final products meet all specifications.
How Can B2B Buyers Verify Supplier Quality Control Practices?
To ensure that suppliers maintain high-quality standards, B2B buyers can take several actions:
- Conduct Audits: Regular audits of suppliers can help verify their adherence to quality standards. This should include reviewing their quality management systems, production processes, and compliance with international standards.
- Request Quality Reports: Suppliers should provide documentation of their quality control processes, including inspection reports and compliance certifications. These reports should detail the methodologies used and the results of various quality checks.
- Third-Party Inspections: Engaging third-party inspection agencies can provide an unbiased assessment of the supplier’s quality practices. This is particularly beneficial for international buyers who may not be able to conduct on-site inspections.
What Are the Quality Control Nuances for International B2B Buyers?
International B2B buyers, particularly those from regions like Africa, South America, the Middle East, and Europe, must navigate various challenges when dealing with suppliers. Key nuances include:
- Cultural Differences: Understanding cultural attitudes towards quality and business practices can help facilitate better communication and expectations with suppliers.
- Regulatory Compliance: Different regions have varying regulations regarding product safety and quality. B2B buyers must ensure that suppliers comply with the relevant local and international standards.
- Logistical Considerations: Shipping and logistics can impact product quality. Buyers should work with suppliers who have robust logistics systems to minimize risks of damage during transit.
Conclusion: The Importance of Manufacturing Processes and Quality Assurance
For international B2B buyers, understanding the manufacturing processes and quality assurance practices of accessory suppliers is essential for ensuring product quality and consistency. By focusing on material preparation, forming, assembly, and finishing, as well as adhering to international standards and implementing robust quality control measures, buyers can make informed decisions that enhance their supply chain and customer satisfaction.
Practical Sourcing Guide: A Step-by-Step Checklist for ‘accessories supplier’
To successfully source accessories suppliers in the global market, particularly if you’re an international B2B buyer from regions like Africa, South America, the Middle East, or Europe, a systematic approach is essential. This checklist provides a structured way to navigate the sourcing process effectively.
Step 1: Define Your Technical Specifications
Begin by clearly outlining the technical specifications of the accessories you need. This step is crucial as it sets the foundation for your entire sourcing process. Consider factors such as material quality, compatibility with existing products, and design standards.
- Material Specifications: Identify the materials that meet your quality standards and customer preferences.
- Compatibility Requirements: Ensure the accessories are compatible with the devices or systems your business supports.
Step 2: Conduct Market Research
Research the market to identify potential suppliers. Understanding the competitive landscape and regional variations in quality and pricing can help you make informed decisions. Utilize industry reports, trade shows, and online platforms.
- Industry Reports: Look for reports that provide insights into market trends and key players.
- Trade Shows: Attend relevant trade shows to network and discover new suppliers.
Step 3: Evaluate Potential Suppliers
Before committing, it’s crucial to vet suppliers thoroughly. Request company profiles, case studies, and references from buyers in a similar industry or region. Don’t just rely on their website.
- Supplier Background: Investigate the supplier’s history, including years in business and previous clientele.
- References: Ask for and contact references to understand their reliability and service quality.
Step 4: Verify Supplier Certifications
Ensure that your potential suppliers have the necessary certifications and compliance with international standards. Certifications can indicate quality assurance and adherence to safety regulations.
- ISO Certifications: Check for ISO certifications relevant to the accessories you are sourcing.
- Local Regulations: Be aware of any regional certifications that may be required in your target market.
Step 5: Request Samples
Before making a bulk purchase, request samples of the accessories. This allows you to assess the quality firsthand and ensure they meet your specifications.
- Quality Assessment: Evaluate the samples for durability, design, and functionality.
- Feedback Loop: Gather feedback from your team or customers on the samples to guide your decision.
Step 6: Negotiate Terms and Pricing
Once you have identified a suitable supplier, negotiate terms and pricing. This step is essential to ensure that you receive the best possible deal while establishing a mutually beneficial relationship.
- Payment Terms: Discuss payment terms that align with your cash flow needs.
- Delivery Schedules: Clarify delivery timelines to ensure they meet your operational requirements.
Step 7: Finalize Contracts and Agreements
Finally, solidify your partnership by drafting contracts that outline all agreed-upon terms. This legal framework protects both parties and ensures clarity in expectations.
- Contract Details: Include specifics about pricing, delivery, quality standards, and dispute resolution.
- Review Process: Have legal counsel review the contract to avoid any potential pitfalls.
By following this structured checklist, you can streamline your sourcing process and establish productive relationships with accessories suppliers, ensuring that your business remains competitive and responsive to market demands.
Comprehensive Cost and Pricing Analysis for accessories supplier Sourcing
What Are the Key Cost Components in Accessories Supplier Sourcing?
When sourcing accessories, understanding the cost structure is crucial for B2B buyers. The primary cost components include:
-
Materials: The choice of materials significantly affects the overall cost. High-quality materials may lead to higher upfront costs but can enhance durability and customer satisfaction.
-
Labor: Labor costs vary by region and the complexity of the accessory. For instance, skilled labor in Europe may be more expensive than in parts of Africa or South America.
-
Manufacturing Overhead: This includes costs related to production facilities, equipment maintenance, and utilities. Efficient manufacturing processes can lower these overhead costs.
-
Tooling: Custom tooling can be a significant upfront investment, especially for unique designs. Buyers should evaluate whether they require customized tooling or if standard options suffice.
-
Quality Control (QC): Implementing robust QC processes ensures that products meet specified standards. While this adds to costs, it can prevent costly returns and enhance brand reputation.
-
Logistics: Shipping and handling costs can vary widely based on the distance, mode of transport, and urgency. Incoterms chosen can also influence logistics costs significantly.
-
Margin: Suppliers typically add a profit margin to their costs. Understanding typical margins in the accessories market can help buyers gauge fair pricing.
How Do Price Influencers Impact Accessories Procurement?
Several factors can influence pricing in the accessories market:
-
Volume/MOQ (Minimum Order Quantity): Larger orders often lead to lower per-unit costs. Buyers should assess their needs against suppliers’ MOQs to optimize pricing.
-
Specifications and Customization: Custom designs or specific features may increase costs. Buyers should weigh the benefits of customization against potential price increases.
-
Material Quality and Certifications: Higher quality materials and certifications (e.g., ISO) can enhance product value but typically come at a higher price. Buyers should consider the importance of these factors for their target market.
-
Supplier Factors: The reputation, reliability, and experience of the supplier can impact pricing. Established suppliers may charge more but can offer better quality assurance.
-
Incoterms: The choice of Incoterms affects who bears the cost and risk during shipping. Understanding these terms can help buyers negotiate better deals.
What Are Effective Buyer Tips for Negotiating Prices?
International B2B buyers, particularly from Africa, South America, the Middle East, and Europe, can employ several strategies to ensure cost efficiency:
-
Negotiate Terms: Always negotiate payment terms, delivery schedules, and pricing. Suppliers may be willing to offer discounts for upfront payments or larger order commitments.
-
Assess Total Cost of Ownership (TCO): Consider not just the purchase price but also long-term costs such as maintenance, shipping, and disposal. A lower initial price may result in higher TCO.
-
Understand Pricing Nuances: Be aware that pricing can vary based on market conditions, currency fluctuations, and regional economic factors. Regularly check market trends to make informed decisions.
-
Build Relationships: Establishing strong relationships with suppliers can lead to better pricing and terms. Loyalty can often result in preferential treatment during negotiations.
-
Leverage Local Knowledge: Engage local agents or experts familiar with the market to navigate complexities in pricing and sourcing. Their insights can lead to significant savings.
Conclusion
In the competitive landscape of accessories sourcing, understanding the cost structure and pricing dynamics is essential for effective procurement. By focusing on key cost components, recognizing price influencers, and utilizing strategic negotiation tips, international B2B buyers can optimize their sourcing processes, resulting in improved margins and business growth. Always remember to consider indicative prices as fluctuating market conditions may impact final costs.
Alternatives Analysis: Comparing accessories supplier With Other Solutions
In the competitive landscape of accessories supply, international B2B buyers face a variety of options. While traditional accessories suppliers offer a range of products, exploring alternatives can provide enhanced value and efficiency. This section examines two viable alternatives to accessories suppliers: direct manufacturer partnerships and online marketplaces. Each option presents unique advantages and challenges that can significantly impact purchasing decisions.
Comparison of Accessories Supplier with Alternatives
Comparison Aspect | Accessories Supplier | Direct Manufacturer Partnership | Online Marketplace |
---|---|---|---|
Performance | High-quality, diverse offerings | Customized products, potentially lower quality control | Varies widely based on sellers |
Cost | Moderate to high prices | Potentially lower costs with bulk purchases | Competitive pricing, but variable |
Ease of Implementation | Streamlined, established processes | Requires negotiation and relationship building | Quick setup, easy to browse and purchase |
Maintenance | Support and warranty options | Direct support, but variable based on manufacturer | Limited support, reliant on seller |
Best Use Case | General business needs, bulk purchases | Custom needs, specialized products | Quick, diverse purchases, testing new products |
What Are the Pros and Cons of a Direct Manufacturer Partnership?
Partnering directly with manufacturers can be an attractive alternative for B2B buyers looking for customized products. This approach allows businesses to tailor products to their specific needs, potentially leading to better integration into their existing systems. However, this route often requires significant upfront investment in relationship building and negotiation. Additionally, quality control can vary significantly between manufacturers, which may impact the final product’s performance. For buyers in Africa and South America, establishing a direct line to manufacturers can also mitigate supply chain challenges.
How Does an Online Marketplace Compare?
Online marketplaces, such as Alibaba or Amazon Business, offer a diverse range of accessories from various sellers. This option is particularly advantageous for companies needing quick access to a broad selection of products without the commitment of bulk purchases. Pricing can be highly competitive, allowing businesses to find deals that suit their budget. However, the quality of products can vary significantly, and support may be limited. Buyers must conduct thorough research and vet sellers to ensure product quality, which can be a time-consuming process.
Conclusion: How to Choose the Right Solution for Your Needs
When selecting between an accessories supplier and alternative solutions, B2B buyers should carefully assess their specific needs. Consider the scale of your business, the importance of product customization, and your budget constraints. For those requiring a wide variety of products quickly, online marketplaces may offer the best flexibility. Conversely, businesses looking for tailored solutions and long-term partnerships might find value in direct manufacturer relationships. Ultimately, the right choice will depend on balancing cost, quality, and the level of support required for your operational success.
Essential Technical Properties and Trade Terminology for accessories supplier
What Are the Essential Technical Properties for Accessories Suppliers?
Understanding the technical specifications of accessories is crucial for international B2B buyers to ensure product quality, compatibility, and overall value. Here are some critical technical properties to consider:
1. Material Grade
Material grade refers to the classification of the materials used in manufacturing accessories. Common materials include plastics, metals, and textiles, each with different grades affecting durability, flexibility, and aesthetic appeal. For instance, accessories made from high-grade polymers tend to be more resistant to wear and tear, making them suitable for long-term use. B2B buyers should prioritize suppliers who provide detailed material specifications to ensure they meet industry standards.
2. Tolerance Levels
Tolerance levels indicate the permissible limits of variation in a physical dimension of an accessory. For example, if a connector is designed to fit a specific port, the tolerance level determines how much deviation is acceptable without compromising functionality. Understanding tolerance is essential for ensuring compatibility with existing products, reducing returns, and enhancing customer satisfaction.
3. Weight Capacity
Weight capacity refers to the maximum load an accessory can support without failure. This is particularly important for accessories like mounts, cases, or bags. B2B buyers must assess the weight capacity to ensure that the accessory can handle the intended use case, especially in industrial or commercial applications.
4. Performance Standards
Performance standards, such as IP ratings for water and dust resistance, are critical for determining how well an accessory will perform under various conditions. An accessory with a higher IP rating will be better suited for environments with exposure to moisture or dust. Buyers should seek suppliers who adhere to recognized performance standards to guarantee reliability in their products.
5. Compatibility Specifications
Compatibility specifications detail which devices or systems an accessory can work with. This includes information on device models, operating systems, and connectivity protocols. For B2B buyers, ensuring compatibility is crucial to avoid product mismatches and ensure seamless integration into existing systems.
What Trade Terms Should B2B Buyers Understand?
Familiarizing yourself with trade terminology can enhance communication with suppliers and streamline procurement processes. Here are some essential terms:
1. OEM (Original Equipment Manufacturer)
OEM refers to a company that produces parts or equipment that may be marketed by another manufacturer. In the context of accessories, B2B buyers may choose OEM products for their reliability and compatibility with branded devices. Understanding OEM relationships can help buyers assess quality and sourcing options.
2. MOQ (Minimum Order Quantity)
MOQ is the smallest amount of product that a supplier is willing to sell. This term is crucial for buyers to understand as it affects inventory management and cash flow. By negotiating MOQ terms, buyers can ensure they meet their needs without overcommitting resources.
3. RFQ (Request for Quotation)
An RFQ is a document that solicits price quotes from suppliers for specified products or services. For international buyers, submitting an RFQ can help compare pricing and terms across different suppliers, facilitating better negotiation outcomes.
4. Incoterms (International Commercial Terms)
Incoterms are internationally recognized rules that define the responsibilities of sellers and buyers in international transactions. They cover aspects such as shipping costs, insurance, and risk transfer. Understanding Incoterms is vital for B2B buyers to mitigate risks and ensure smooth logistics operations.
5. Lead Time
Lead time refers to the amount of time it takes from placing an order to receiving the goods. For B2B buyers, understanding lead times is crucial for inventory management and planning. Suppliers with shorter lead times can enhance a buyer’s ability to respond quickly to market demands.
By being well-versed in these technical properties and trade terms, international B2B buyers can make informed decisions when sourcing accessories, ultimately leading to improved operational efficiency and product satisfaction.
Navigating Market Dynamics and Sourcing Trends in the accessories supplier Sector
What Are the Current Market Dynamics and Key Trends in the Accessories Supplier Sector?
The accessories supplier sector is currently experiencing significant transformation driven by several global factors. The rise of e-commerce and digital marketplaces has made it easier for international B2B buyers, particularly from Africa, South America, the Middle East, and Europe, to source products. Moreover, the COVID-19 pandemic accelerated digital adoption, leading to a surge in online shopping for accessories. Buyers are increasingly looking for suppliers who can provide a seamless digital experience, including easy navigation of product catalogs and efficient payment processes.
Emerging technologies, such as artificial intelligence and machine learning, are reshaping how suppliers manage inventory and customer relationships. For instance, AI-driven analytics help suppliers predict demand trends, enabling them to optimize stock levels and reduce lead times. Additionally, the trend toward customization and personalization in accessories is growing, as buyers seek unique products that cater to local tastes. This shift is particularly relevant in diverse markets like Africa and South America, where cultural preferences play a significant role in purchasing decisions.
The sustainability movement is also influencing market dynamics. International buyers are increasingly prioritizing suppliers who demonstrate a commitment to eco-friendly practices. This has led to a rise in demand for accessories made from sustainable materials, which in turn impacts sourcing strategies. Buyers should keep an eye on suppliers who can offer innovative solutions that align with both market trends and consumer expectations.
How Important Is Sustainability and Ethical Sourcing in the Accessories Supplier Sector?
Sustainability and ethical sourcing are no longer optional in the accessories supplier sector; they are crucial for long-term success. The environmental impact of manufacturing processes, particularly in plastics and textiles, has drawn scrutiny from consumers and regulatory bodies alike. B2B buyers are now more inclined to partner with suppliers who adopt sustainable practices, such as using recycled materials, minimizing waste, and ensuring ethical labor practices.
Green certifications are becoming increasingly important in the B2B landscape. Certifications like GOTS (Global Organic Textile Standard) for textiles, FSC (Forest Stewardship Council) for wood products, and ISO 14001 for environmental management systems are valuable indicators of a supplier’s commitment to sustainability. Buyers should prioritize suppliers with these certifications to ensure compliance with international standards and to meet the growing demand for eco-friendly products.
Additionally, transparency in the supply chain is essential. Buyers should seek suppliers that provide clear information about their sourcing practices, labor conditions, and environmental impact. This transparency not only builds trust but also mitigates risks associated with unethical practices. As the global market increasingly values sustainability, aligning with ethical suppliers will be a key differentiator for B2B buyers.
How Has the Accessories Supplier Sector Evolved Over Time?
The accessories supplier sector has evolved significantly over the past few decades, transitioning from traditional brick-and-mortar operations to a highly digitized landscape. Initially dominated by local artisans and small businesses, the sector has seen a surge in globalization, with suppliers expanding their reach to international markets. This evolution has been facilitated by advancements in technology and logistics, allowing suppliers to efficiently manage global supply chains.
In the early 2000s, the rise of e-commerce platforms transformed how accessories were marketed and sold. Suppliers began to leverage online marketplaces to reach a broader audience, leading to increased competition and innovation. Fast forward to today, and we see a landscape where technology, sustainability, and customization are at the forefront. As international B2B buyers navigate this dynamic environment, understanding these historical shifts will be essential for making informed sourcing decisions and staying ahead of market trends.
Frequently Asked Questions (FAQs) for B2B Buyers of accessories supplier
-
How do I choose the right accessories supplier for my business needs?
Choosing the right accessories supplier involves assessing various factors such as product quality, price, reliability, and delivery times. Start by identifying your specific needs and preferences, such as the types of accessories required and any customization options. Research potential suppliers through online directories, industry trade shows, and recommendations. Request samples to evaluate quality, and don’t hesitate to ask for references or case studies from other clients. Finally, consider their ability to scale with your business, especially if you plan to expand your product offerings. -
What is the best way to negotiate payment terms with an accessories supplier?
Negotiating favorable payment terms is crucial for cash flow management. Start by understanding standard payment practices in the industry, which can vary by region. Consider proposing a payment plan that aligns with your cash flow, such as 30% upfront and the balance upon delivery. Be transparent about your financial capabilities and express your intent for a long-term partnership. Additionally, inquire about discounts for early payments or bulk orders, which can help in securing better deals while maintaining a positive relationship with your supplier. -
What should I consider regarding minimum order quantities (MOQ) when sourcing accessories?
Minimum Order Quantities (MOQ) can significantly impact your purchasing strategy. When evaluating suppliers, inquire about their MOQ policies and assess whether they align with your inventory needs. If the MOQ is too high, consider negotiating for a smaller initial order to test the market. Additionally, explore whether the supplier offers tiered pricing based on order volume, which can provide cost benefits as you scale. Understanding their flexibility on MOQ can also indicate their willingness to build a collaborative relationship. -
How can I ensure quality assurance (QA) when sourcing accessories internationally?
Implementing a robust quality assurance process is essential when sourcing accessories from international suppliers. Start by clearly defining quality standards in your contract, including materials, specifications, and compliance with relevant regulations. Conduct pre-production inspections and request samples for evaluation. Additionally, consider hiring a third-party inspection service to conduct quality checks during production and before shipment. Establishing a clear communication channel with your supplier can also help address any quality issues promptly. -
What logistics considerations should I keep in mind when importing accessories?
Logistics play a crucial role in the successful importation of accessories. Understand the shipping options available, including air freight for speed or sea freight for cost-effectiveness. Be aware of customs regulations and import duties that may apply in your country, as these can impact overall costs. Collaborating with a reliable freight forwarder can streamline the shipping process and help navigate complex paperwork. Also, factor in lead times and potential delays when planning your inventory to ensure you meet customer demands without interruption. -
How do I verify the credibility of an accessories supplier?
Verifying a supplier’s credibility is vital to mitigating risks in international trade. Start by conducting thorough background checks, including their business registration, financial stability, and reputation in the industry. Look for certifications, such as ISO or product-specific certifications, that demonstrate compliance with quality standards. Additionally, seek feedback from previous clients through testimonials or reviews on platforms like Alibaba or industry forums. A site visit can also provide valuable insights into their operations and commitment to quality. -
What customization options are typically available when ordering accessories?
Customization options can vary widely among accessories suppliers. Common options include branding with your logo, color variations, and tailored packaging. Some suppliers may also offer product modifications based on functionality or design preferences. When discussing customization, clearly communicate your requirements and ask for mock-ups or prototypes to ensure they meet your expectations. Understanding the lead times and costs associated with customization is essential for effective planning and budget management. -
What are the common challenges faced by international B2B buyers in sourcing accessories?
International B2B buyers often face challenges such as language barriers, cultural differences, and varying regulations across countries. Additionally, managing logistics and navigating customs can complicate the import process. Quality control is another concern, as differences in manufacturing standards can lead to discrepancies in product quality. Establishing strong communication with suppliers and utilizing local experts can help mitigate these challenges. Networking within industry groups can also provide valuable insights and support for overcoming sourcing difficulties.
Important Disclaimer & Terms of Use
⚠️ Important Disclaimer
The information provided in this guide, including content regarding manufacturers, technical specifications, and market analysis, is for informational and educational purposes only. It does not constitute professional procurement advice, financial advice, or legal advice.
While we have made every effort to ensure the accuracy and timeliness of the information, we are not responsible for any errors, omissions, or outdated information. Market conditions, company details, and technical standards are subject to change.
B2B buyers must conduct their own independent and thorough due diligence before making any purchasing decisions. This includes contacting suppliers directly, verifying certifications, requesting samples, and seeking professional consultation. The risk of relying on any information in this guide is borne solely by the reader.
Strategic Sourcing Conclusion and Outlook for accessories supplier
In navigating the complex landscape of sourcing accessories, international B2B buyers must prioritize strategic sourcing to enhance their competitive edge. By leveraging data-driven decision-making, buyers can identify reputable suppliers that align with their quality and ethical standards. Establishing strong partnerships with suppliers from diverse regions—such as Africa, South America, the Middle East, and Europe—enables businesses to tap into unique market insights and innovative products.
What Are the Key Takeaways for Successful Sourcing?
The importance of thorough market research cannot be overstated. Buyers should engage in comprehensive supplier evaluations, considering factors like reliability, cost-effectiveness, and compliance with international trade regulations. Additionally, fostering relationships with local distributors can facilitate smoother logistics and enhance product availability, ultimately leading to improved customer satisfaction.
How Can Buyers Prepare for Future Sourcing Opportunities?
Looking ahead, the accessories market is poised for growth, driven by technological advancements and evolving consumer preferences. B2B buyers are encouraged to remain agile and responsive to these changes. By staying informed about trends and emerging technologies, buyers can strategically position themselves to capitalize on new opportunities.
In conclusion, embracing strategic sourcing practices is not just a necessity but a pathway to sustainable growth. International buyers should act now to forge strong partnerships and innovate their sourcing strategies, ensuring they remain at the forefront of the accessories market.