Unlock Savings: Your Guide to Galvanized Steel Manufacturer (2025)
Introduction: Navigating the Global Market for galvanized steel manufacturer
Navigating the global market for galvanized steel manufacturers presents unique challenges, especially for international B2B buyers. The complexities of sourcing high-quality galvanized steel can be daunting, particularly when trying to balance cost-effectiveness with durability and compliance to industry standards. This guide aims to demystify the process by providing a comprehensive overview of galvanized steel types, their applications across various industries, and essential criteria for supplier vetting.
International buyers from regions such as Africa, South America, the Middle East, and Europe—including key markets like the UAE and Brazil—will find actionable insights tailored to their specific needs. From understanding the nuances of galvanization processes to evaluating suppliers based on quality certifications and delivery capabilities, this guide equips buyers with the knowledge necessary for making informed purchasing decisions.
Additionally, we will explore cost considerations, potential supply chain challenges, and market trends that influence the galvanized steel sector. By leveraging the insights provided in this guide, B2B buyers can navigate the complexities of the global galvanized steel market with confidence, ensuring they select suppliers that align with their operational and strategic goals.
Understanding galvanized steel manufacturer Types and Variations
Type Name | Key Distinguishing Features | Primary B2B Applications | Brief Pros & Cons for Buyers |
---|---|---|---|
Hot-Dip Galvanized Steel | Coated by dipping in molten zinc, thick layer | Construction, automotive, agriculture | Pros: Excellent corrosion resistance; durable. Cons: Heavier; higher initial cost. |
Electro-Galvanized Steel | Thin zinc coating applied via electroplating | Electrical components, light-duty parts | Pros: Smooth finish; good for aesthetics. Cons: Less corrosion resistance than hot-dip. |
Pre-Galvanized Steel | Coated before fabrication, uniform coating | HVAC systems, furniture, fencing | Pros: Cost-effective; consistent quality. Cons: Limited thickness; less durable in harsh environments. |
Galvannealed Steel | Zinc-iron alloy coating for superior paint adhesion | Appliances, automotive parts | Pros: Excellent paintability; strong coating. Cons: Higher processing costs; less corrosion resistance than hot-dip. |
Zinc-Aluminum Coated Steel | Coating with both zinc and aluminum for enhanced protection | Marine applications, roofing | Pros: Superior corrosion resistance; high-temperature stability. Cons: More expensive; requires specialized welding. |
What are the Characteristics of Hot-Dip Galvanized Steel?
Hot-dip galvanized steel is produced by immersing steel in molten zinc, forming a thick, protective layer. This method provides exceptional corrosion resistance, making it ideal for outdoor applications in construction, automotive, and agricultural sectors. Buyers should consider the weight and initial cost, which can be higher than other types. However, the long-term durability often justifies the investment, especially in harsh environments.
How Does Electro-Galvanized Steel Differ from Other Types?
Electro-galvanized steel features a thin zinc coating applied through electroplating, resulting in a smooth finish that is aesthetically pleasing. This type is commonly used in electrical components and light-duty applications where appearance matters. While it offers decent corrosion resistance, it is less robust than hot-dip galvanized steel. B2B buyers should weigh the benefits of visual appeal against the potential for reduced durability in more demanding environments.
Why Choose Pre-Galvanized Steel for Your Projects?
Pre-galvanized steel is coated before fabrication, ensuring a uniform zinc layer. This type is particularly cost-effective and is widely used in HVAC systems, furniture, and fencing. Its consistent quality makes it an attractive option for manufacturers. However, the limited thickness of the coating may not withstand extreme conditions, so buyers should evaluate their specific application needs carefully.
What are the Advantages of Galvannealed Steel?
Galvannealed steel features a unique zinc-iron alloy coating, which provides excellent adhesion for paint and other finishes. It is commonly used in appliances and automotive parts due to its strong coating and paintability. While it may have higher processing costs, its performance can be beneficial for manufacturers looking for high-quality finishes. Buyers should consider the application requirements and potential trade-offs in corrosion resistance.
When Should You Consider Zinc-Aluminum Coated Steel?
Zinc-aluminum coated steel combines zinc and aluminum, offering enhanced corrosion resistance and high-temperature stability. This makes it suitable for marine applications and roofing where exposure to harsh environments is a concern. While it provides superior protection, it is generally more expensive and may require specialized welding techniques. B2B buyers in these industries should evaluate the cost versus the long-term benefits of using this advanced material.
Related Video: The manufacture of rolled/ galvanized/ color-coated steel sheet
Key Industrial Applications of galvanized steel manufacturer
Industry/Sector | Specific Application of galvanized steel manufacturer | Value/Benefit for the Business | Key Sourcing Considerations for this Application |
---|---|---|---|
Construction | Structural framing and supports | Provides durability and corrosion resistance, extending the lifespan of buildings. | Ensure compliance with local building codes and standards. Consider weight and load-bearing specifications. |
Automotive | Body panels and chassis components | Enhances vehicle longevity by preventing rust and reducing maintenance costs. | Verify compatibility with various automotive models and standards for safety. |
Agriculture | Fencing and storage solutions | Increases the protection of livestock and crops, reducing losses. | Assess the environmental impact and suitability for local climates. |
Infrastructure | Utility poles and communication towers | Supports critical services with minimal maintenance needs, ensuring reliability. | Evaluate local regulations for installation and safety protocols. |
Energy | Pipelines and storage tanks | Ensures safe and efficient transport of resources while minimizing leakage risks. | Confirm adherence to international safety standards and material certifications. |
How is Galvanized Steel Used in the Construction Industry?
In the construction sector, galvanized steel is predominantly utilized for structural framing and supports. This application offers significant benefits, including enhanced durability and corrosion resistance, which are vital for structures exposed to harsh weather conditions. International buyers, particularly from Africa and the Middle East, should prioritize sourcing galvanized steel that complies with local building codes and standards to ensure safety and longevity.
What Role Does Galvanized Steel Play in the Automotive Sector?
In the automotive industry, galvanized steel is commonly used for body panels and chassis components. Its rust-resistant properties not only enhance the vehicle’s lifespan but also reduce maintenance costs for owners. Buyers from South America and Europe should ensure that the galvanized steel they procure meets the specific safety and compatibility standards of various automotive models, which can vary significantly by region.
How is Galvanized Steel Beneficial for Agriculture?
Galvanized steel finds vital applications in agriculture, particularly for fencing and storage solutions. By providing robust protection for livestock and crops, galvanized steel fencing helps minimize losses due to theft or animal intrusion. Buyers in Africa and South America should consider the environmental impact and the suitability of galvanized steel for local climates, ensuring the material can withstand specific weather conditions.
What is the Application of Galvanized Steel in Infrastructure?
In the infrastructure sector, galvanized steel is utilized for utility poles and communication towers. Its robustness ensures that critical services remain operational with minimal maintenance requirements. International B2B buyers should evaluate local regulations regarding installation and safety protocols, as these can vary widely between regions, particularly in Europe and the Middle East.
How Does Galvanized Steel Enhance Energy Sector Operations?
In the energy sector, galvanized steel is essential for pipelines and storage tanks. Its corrosion resistance is crucial for ensuring the safe and efficient transport of resources, while minimizing the risk of leaks. Buyers from all regions, particularly those in South America and Europe, should confirm that the galvanized steel meets international safety standards and material certifications, ensuring compliance and reliability in their operations.
Related Video: Uses Of Metals – Gold, Copper, Aluminium, Steel | Properties of Matter | Chemistry | FuseSchool
3 Common User Pain Points for ‘galvanized steel manufacturer’ & Their Solutions
Scenario 1: Quality Assurance in Sourcing Galvanized Steel
The Problem: Many B2B buyers in industries such as construction, automotive, or manufacturing face significant challenges in ensuring the quality and durability of galvanized steel products. The galvanized steel must meet specific standards to resist corrosion and ensure longevity. However, buyers often encounter discrepancies between the promised quality and the actual product received, leading to costly delays and project setbacks.
The Solution: To mitigate quality assurance issues, B2B buyers should implement a rigorous sourcing strategy. Start by requesting certifications from manufacturers that comply with international standards, such as ASTM A123 for zinc coatings. Additionally, conducting a thorough supplier audit can provide insights into the manufacturer’s production processes, quality control measures, and material traceability. Establishing a clear communication channel with the manufacturer to discuss specifications and quality expectations can also help prevent misunderstandings. Finally, consider ordering a small batch for initial testing before making a larger commitment, ensuring that the galvanized steel meets the required standards for your specific applications.
Scenario 2: Understanding Pricing Structures for Galvanized Steel
The Problem: Pricing transparency is often a pain point for B2B buyers dealing with galvanized steel manufacturers. Buyers may find themselves confused by fluctuating prices, hidden fees, and varying quotes from different suppliers. This lack of clarity can lead to budget overruns and financial strain, especially for projects with tight margins.
The Solution: To navigate the complexities of pricing, buyers should establish a clear understanding of the factors influencing galvanized steel prices, such as raw material costs, manufacturing processes, and market demand. Request detailed quotes that break down the pricing structure, including material costs, labor, and any potential additional fees. It’s also beneficial to develop relationships with multiple suppliers to compare quotes and negotiate better terms. Utilize tools such as price trend reports and market analysis to stay informed about fluctuations in the galvanized steel market. By being proactive and educated about pricing, buyers can better manage budgets and avoid unexpected costs.
Scenario 3: Timely Delivery and Logistics Challenges
The Problem: Timeliness in delivery can be a critical concern for B2B buyers. Delays in receiving galvanized steel can halt construction projects, disrupt production schedules, and ultimately lead to financial losses. Buyers often struggle with manufacturers who provide vague timelines or fail to communicate effectively about shipping and handling processes.
The Solution: To ensure timely delivery, buyers should establish clear logistical expectations upfront with their galvanized steel manufacturers. This includes setting specific timelines for production and delivery, as well as discussing contingencies for potential delays. Implementing a just-in-time inventory system can also help manage stock levels and reduce the impact of delivery delays on ongoing projects. Consider using third-party logistics providers with expertise in handling galvanized steel to streamline the shipping process. Finally, regular follow-ups and tracking shipments can help buyers stay informed about the status of their orders and address any issues before they escalate. By taking these proactive steps, buyers can enhance their supply chain efficiency and minimize the risk of delays.
Strategic Material Selection Guide for galvanized steel manufacturer
What Are the Key Materials Used in Galvanized Steel Manufacturing?
When selecting materials for galvanized steel manufacturing, it’s essential to consider the properties, advantages, and limitations of various options. This analysis focuses on four common materials: carbon steel, stainless steel, aluminum, and zinc. Each material has unique characteristics that affect performance, cost, and suitability for specific applications.
How Does Carbon Steel Perform in Galvanized Steel Manufacturing?
Key Properties: Carbon steel is known for its excellent strength-to-weight ratio, making it a popular choice in construction and manufacturing. It has good weldability and can withstand moderate temperature and pressure conditions.
Pros & Cons: The primary advantage of carbon steel is its cost-effectiveness, making it accessible for large-scale projects. However, its susceptibility to corrosion necessitates galvanization, which adds to manufacturing complexity. While it offers durability, it may not perform well in highly corrosive environments without proper coating.
Impact on Application: Carbon steel is suitable for structural applications, such as beams and columns, where strength is paramount. However, in regions with high humidity or saline environments, it may require additional protective measures.
Considerations for International Buyers: Buyers from Africa, South America, the Middle East, and Europe should ensure compliance with local standards such as ASTM or DIN. In the UAE, for instance, adherence to local building codes is critical for project approval.
What Are the Benefits of Using Stainless Steel in Galvanized Steel Manufacturing?
Key Properties: Stainless steel is renowned for its corrosion resistance, high-temperature tolerance, and aesthetic appeal. It contains chromium, which forms a protective layer against oxidation.
Pros & Cons: The key advantage of stainless steel is its longevity and low maintenance requirements, making it ideal for applications exposed to harsh environments. However, it comes with a higher cost compared to carbon steel, which can be a limiting factor for budget-conscious projects.
Impact on Application: Stainless steel is often used in food processing, chemical industries, and architectural applications due to its hygienic properties and resistance to staining. Its compatibility with various media makes it a versatile choice.
Considerations for International Buyers: Buyers should be aware of the specific grades of stainless steel that meet local standards. In Europe, for example, compliance with EN standards is essential for market acceptance.
How Does Aluminum Compare in Galvanized Steel Manufacturing?
Key Properties: Aluminum is lightweight, corrosion-resistant, and has excellent thermal and electrical conductivity. It is also non-magnetic, making it suitable for various applications.
Pros & Cons: The primary advantage of aluminum is its lightweight nature, which reduces transportation costs and simplifies installation. However, its lower strength compared to steel can be a drawback in structural applications. Additionally, aluminum can be more expensive than carbon steel.
Impact on Application: Aluminum is often used in applications where weight savings are critical, such as in aerospace and automotive industries. Its corrosion resistance makes it suitable for outdoor applications in coastal areas.
Considerations for International Buyers: Buyers must consider the specific grades of aluminum that comply with regional standards. In Brazil, for example, adherence to ABNT standards is crucial for regulatory compliance.
What Role Does Zinc Play in Galvanized Steel Manufacturing?
Key Properties: Zinc is primarily used as a protective coating for steel to enhance its corrosion resistance. It provides a sacrificial layer, meaning it will corrode before the underlying steel does.
Pros & Cons: The key advantage of zinc is its cost-effectiveness and ability to extend the lifespan of steel products significantly. However, the process of galvanization can add complexity and time to manufacturing.
Impact on Application: Zinc-coated steel is widely used in construction, automotive, and appliance industries due to its durability and resistance to corrosion. It is particularly effective in environments prone to moisture.
Considerations for International Buyers: Buyers should ensure that the galvanization process meets relevant standards such as ASTM A123 or ISO 1461, which dictate the thickness and quality of the zinc coating.
Summary Table of Material Selection for Galvanized Steel Manufacturing
Material | Typical Use Case for galvanized steel manufacturer | Key Advantage | Key Disadvantage/Limitation | Relative Cost (Low/Med/High) |
---|---|---|---|---|
Carbon Steel | Structural beams and columns | Cost-effective | Susceptible to corrosion | Low |
Stainless Steel | Food processing and chemical industries | High corrosion resistance | Higher cost | High |
Aluminum | Aerospace and automotive applications | Lightweight and corrosion-resistant | Lower strength compared to steel | Medium |
Zinc | Protective coating for steel products | Extends lifespan of steel | Adds complexity to manufacturing | Low |
This guide provides international B2B buyers with actionable insights into material selection for galvanized steel manufacturing, ensuring informed decisions that align with local standards and application requirements.
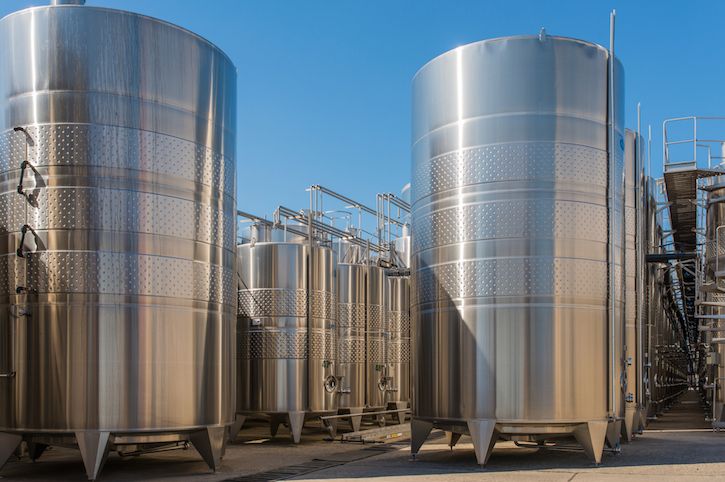
A stock image related to galvanized steel manufacturer.
In-depth Look: Manufacturing Processes and Quality Assurance for galvanized steel manufacturer
What Are the Main Stages of Manufacturing Galvanized Steel?
Manufacturing galvanized steel involves several critical stages that ensure the final product meets industry standards and customer requirements. The typical process can be broken down into four main stages: material preparation, forming, assembly, and finishing.
Material Preparation: What Steps Are Involved?
The first step in the manufacturing process is material preparation, which begins with the selection of high-quality steel. This steel is typically cleaned to remove any contaminants, such as rust, grease, or scale, which could affect the galvanizing process. The most common cleaning methods include pickling (using acid solutions) and abrasive blasting.
Once the steel is cleaned, it is cut to the desired dimensions based on specifications provided by the customer. This stage is crucial as it sets the foundation for the subsequent forming processes.
How Is Steel Formed into Desired Shapes?
The forming stage involves shaping the prepared steel into the desired configuration. This can be achieved through various techniques such as rolling, bending, or stamping. For instance, hot rolling is often used for thicker materials, while cold rolling may be employed for thinner gauges.
Advanced technologies like CNC (Computer Numerical Control) machines are increasingly utilized to enhance precision and repeatability in the forming process. The formed steel is then subjected to further processing, such as welding, if necessary, to create larger structures or components.
What Is the Assembly Process for Galvanized Steel Products?
Following the forming stage, the next step is assembly. This involves joining multiple formed pieces together to create the final product. Welding, riveting, or bolting are common techniques used in this stage.
Attention to detail during assembly is critical, as any misalignment or improper joining can lead to structural weaknesses in the final product. For large structures, assembly often takes place on-site, while smaller components may be assembled in a factory setting.
What Finishing Techniques Are Applied to Galvanized Steel?
Finishing is the final stage in the manufacturing process, focusing on enhancing the surface quality and protective properties of the galvanized steel. The primary technique used is galvanization, which involves coating the steel with a layer of zinc to protect against corrosion.
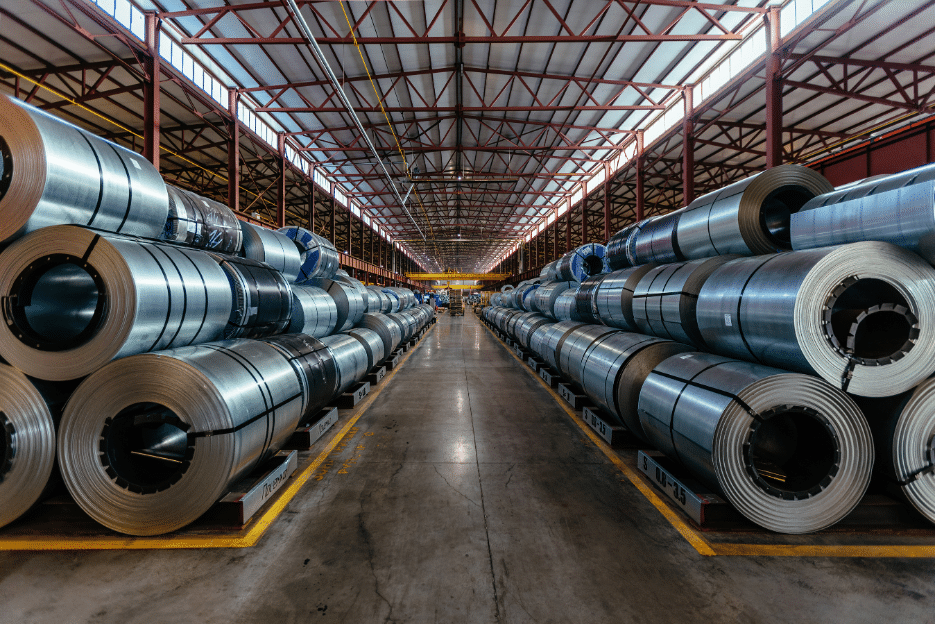
A stock image related to galvanized steel manufacturer.
There are two main methods of galvanization: hot-dip galvanization and electro-galvanization. Hot-dip galvanization involves immersing the steel in molten zinc, creating a thick and durable coating. Electro-galvanization uses an electrochemical process to apply a thinner layer of zinc.
After galvanization, additional finishing processes may include painting or applying protective films to improve aesthetics and performance.
How Is Quality Assurance Implemented in Galvanized Steel Manufacturing?
Quality assurance (QA) is a critical aspect of the manufacturing process, ensuring that the galvanized steel products meet both international standards and specific customer requirements.
What International Standards Govern Galvanized Steel Quality?
International standards such as ISO 9001 provide a framework for quality management systems, which help manufacturers improve their processes and ensure consistent quality. In addition, industry-specific standards like CE marking for the European market and API (American Petroleum Institute) specifications for oil and gas applications are also essential.
These standards outline specific requirements for product quality, safety, and performance, making it crucial for manufacturers to align their processes accordingly.
What Are the Key Quality Control Checkpoints?
Quality control (QC) is implemented at several checkpoints throughout the manufacturing process, including:
-
Incoming Quality Control (IQC): This involves inspecting raw materials upon arrival to ensure they meet specifications. Non-conforming materials are rejected or returned.
-
In-Process Quality Control (IPQC): During the manufacturing stages, random checks are conducted to monitor processes and detect any deviations from quality standards. This helps in identifying issues early in the production cycle.
-
Final Quality Control (FQC): Before shipment, finished products undergo a thorough inspection to ensure they meet the required specifications and standards. This includes dimensional checks, coating thickness measurements, and visual inspections for defects.
What Common Testing Methods Are Used for Galvanized Steel?
Various testing methods are employed to verify the quality and performance of galvanized steel products. Common testing methods include:
-
Coating Thickness Measurement: Ensures that the zinc coating meets specified thickness requirements, which is critical for corrosion resistance.
-
Adhesion Testing: Assesses how well the zinc coating adheres to the steel substrate, using methods like the cross-cut test.
-
Corrosion Testing: Simulates environmental conditions to evaluate the corrosion resistance of the galvanized steel.
How Can B2B Buyers Verify Supplier Quality Control?
For international B2B buyers, especially those from Africa, South America, the Middle East, and Europe, verifying supplier quality control is vital to ensuring product reliability. Here are some actionable insights:
-
Conduct Supplier Audits: Regular audits of potential suppliers can provide insights into their manufacturing processes and quality assurance practices. Look for certifications like ISO 9001 and industry-specific credentials.
-
Request Quality Control Reports: Ask suppliers for detailed QC reports that outline their testing methods, results, and any corrective actions taken for non-conforming products.
-
Engage Third-Party Inspectors: Utilizing third-party inspection services can provide an unbiased assessment of the supplier’s quality control measures and product quality.
-
Check for Compliance with International Standards: Ensure that the supplier’s products comply with relevant international standards, which can be verified through documentation or certifications.
What Are the Quality Control Nuances for International B2B Buyers?
When sourcing galvanized steel internationally, B2B buyers should be aware of specific nuances that may affect quality assurance. Different regions may have varying standards and regulations that impact product quality and compliance.
Buyers from Europe, for instance, must be particularly vigilant about CE marking, which certifies that products meet EU safety, health, and environmental protection requirements. In contrast, buyers from the Middle East may prioritize compliance with local standards that cater to specific environmental conditions.
Understanding these regional differences allows buyers to make informed decisions and ensures that the galvanized steel products they procure meet their quality expectations and regulatory requirements.
By focusing on these aspects of manufacturing processes and quality assurance, B2B buyers can enhance their procurement strategies, ensuring they partner with reliable galvanized steel manufacturers that deliver high-quality products tailored to their specific needs.
Practical Sourcing Guide: A Step-by-Step Checklist for ‘galvanized steel manufacturer’
To effectively source galvanized steel manufacturers, B2B buyers must navigate a complex landscape of suppliers, specifications, and market conditions. This step-by-step checklist is designed to streamline the procurement process, ensuring buyers make informed decisions that align with their operational needs.
Step 1: Define Your Technical Specifications
Establish clear requirements for your galvanized steel needs. This includes dimensions, grades, coating thickness, and intended applications. By defining these specifications upfront, you can ensure that potential suppliers can meet your exact requirements, thus minimizing delays and discrepancies later in the process.
Step 2: Research and Shortlist Potential Suppliers
Conduct thorough market research to identify reputable suppliers. Utilize industry directories, trade shows, and online platforms to compile a list of potential manufacturers. Focus on suppliers with a strong presence in your region, as they may better understand local regulations and logistics.
Step 3: Verify Supplier Certifications and Compliance
Ensure that your selected suppliers possess necessary certifications. Look for ISO certifications, compliance with ASTM standards, and any relevant local certifications. Certifications not only demonstrate quality assurance but also indicate that the manufacturer adheres to international safety and environmental standards.
Step 4: Assess Production Capabilities and Capacity
Evaluate the manufacturing capabilities of potential suppliers. Inquire about their production capacity, technology used, and quality control processes. A manufacturer with advanced technology and robust quality assurance practices is more likely to deliver consistent products that meet your specifications.
Step 5: Request Samples and Conduct Quality Inspections
Always request samples before finalizing your order. Assess the quality of the galvanized steel samples against your specifications. Furthermore, consider hiring a third-party inspection service to conduct a quality audit of the manufacturer’s facilities to ensure they meet your standards.
Step 6: Analyze Pricing and Payment Terms
Compare pricing structures and payment terms among shortlisted suppliers. While it may be tempting to choose the lowest price, it’s essential to consider the overall value, including quality, delivery times, and after-sales support. Negotiate payment terms that align with your cash flow needs to avoid financial strain.
Step 7: Establish Clear Communication and Logistics Plans
Set up a robust communication plan with your chosen supplier. Clear lines of communication can facilitate timely updates on production status and delivery schedules. Additionally, discuss logistics and shipping arrangements to ensure that the galvanized steel is delivered on time and in the expected condition.
By following this structured checklist, international B2B buyers can enhance their sourcing process for galvanized steel manufacturers, ensuring that they select reliable suppliers who meet their technical and operational needs.
Comprehensive Cost and Pricing Analysis for galvanized steel manufacturer Sourcing
What Are the Key Cost Components in Sourcing Galvanized Steel?
When sourcing galvanized steel, international B2B buyers need to understand the various cost components that contribute to the overall price. These include:
-
Materials: The primary cost driver is the raw materials, which typically include steel and zinc. Prices for these materials can fluctuate based on market demand, geopolitical factors, and availability. Buyers should regularly monitor commodity prices to make informed purchasing decisions.
-
Labor: Labor costs vary significantly by region. For instance, manufacturing in regions with higher wage standards, such as Europe, may lead to increased costs compared to manufacturing in areas like Africa or South America. Understanding local labor laws and wage standards is crucial for accurate cost estimation.
-
Manufacturing Overhead: This includes costs associated with running the factory, such as utilities, maintenance, and administrative expenses. A manufacturer with efficient processes may offer competitive pricing due to lower overhead costs.
-
Tooling: The cost of tools and equipment necessary for manufacturing galvanized steel can be substantial. Buyers should inquire about the tooling costs, especially if custom designs are required.
-
Quality Control (QC): Ensuring high-quality standards is essential, especially for industries like construction and automotive where safety is paramount. Investments in QC processes can add to the overall cost but are often necessary to meet regulatory standards and customer expectations.
-
Logistics: Transportation and shipping costs can significantly impact the final price. Factors such as distance, mode of transport, and fuel prices should be considered. Additionally, international buyers should be aware of tariffs and customs duties that may apply.
-
Margin: Manufacturers typically add a profit margin to their costs. This margin can vary based on the manufacturer’s market position, reputation, and the level of competition.
How Do Price Influencers Affect Sourcing Decisions for Galvanized Steel?
Several factors can influence the pricing of galvanized steel and should be carefully considered by buyers:
-
Volume and Minimum Order Quantity (MOQ): Larger orders often lead to lower per-unit costs. Buyers should negotiate MOQs that align with their needs to optimize pricing.
-
Specifications and Customization: Custom specifications can lead to higher costs due to the need for specialized processes or materials. Buyers must weigh the benefits of customization against the potential for increased expenses.
-
Materials Quality and Certifications: Steel with specific quality certifications (e.g., ISO, ASTM) may command a higher price. Buyers should assess the importance of these certifications relative to their application requirements.
-
Supplier Factors: The reputation and reliability of the supplier can affect pricing. Established suppliers with a history of quality and reliability may charge a premium, but they can also reduce risks associated with sourcing.
-
Incoterms: Understanding the agreed-upon Incoterms is critical as they define the responsibilities of buyers and sellers in terms of costs and risks. This can impact the total landed cost of the galvanized steel.
What Are Effective Buyer Tips for Negotiating Galvanized Steel Prices?
B2B buyers from Africa, South America, the Middle East, and Europe should consider the following strategies to enhance their purchasing process:
-
Negotiate Wisely: Build relationships with suppliers to foster trust and open communication. Use market data to leverage negotiations, and be prepared to walk away if the terms do not meet your expectations.
-
Focus on Cost Efficiency: Evaluate suppliers not only on price but also on their total cost of ownership (TCO). This includes costs related to quality issues, logistics, and potential delays. A cheaper upfront price may lead to higher long-term costs if the product does not meet quality standards.
-
Understand Pricing Nuances: Be aware of regional pricing variations due to local market conditions, currency fluctuations, and economic factors. For instance, tariffs on imported steel can significantly affect prices in certain regions.
-
Stay Informed: Regularly review market trends and pricing forecasts for galvanized steel. Being proactive can help buyers make timely purchasing decisions and avoid price spikes.
Conclusion: What to Keep in Mind About Pricing for Galvanized Steel?
While this analysis provides a framework for understanding the costs and pricing of galvanized steel, it is important to note that actual prices can vary widely based on specific circumstances and supplier negotiations. Buyers should conduct thorough due diligence and seek multiple quotes to ensure they are getting the best possible price for their requirements.
Alternatives Analysis: Comparing galvanized steel manufacturer With Other Solutions
In the realm of construction and manufacturing, choosing the right material is critical to achieving desired performance while balancing cost and sustainability. Galvanized steel, known for its corrosion resistance and durability, is a popular choice. However, several alternatives can also meet similar needs. This section provides an analysis of galvanized steel in comparison to alternative materials, helping B2B buyers make informed decisions.
Comparison Aspect | Galvanized Steel Manufacturer | Stainless Steel Manufacturer | Aluminum Manufacturer |
---|---|---|---|
Performance | High durability and corrosion resistance; suitable for outdoor use | Excellent corrosion resistance; suitable for harsh environments | Lightweight and corrosion-resistant; ideal for non-structural applications |
Cost | Moderate initial cost; cost-effective over time due to longevity | Higher initial cost; long-term savings due to durability | Lower initial cost; may require more frequent replacements |
Ease of Implementation | Requires specialized tools for cutting and welding; moderate complexity | Requires specialized tools; moderate to high complexity | Easy to cut and shape; low complexity |
Maintenance | Low maintenance; periodic inspection recommended | Very low maintenance; resistant to staining and rust | Low maintenance; susceptible to denting |
Best Use Case | Structural applications, fencing, and outdoor furniture | Marine applications, chemical processing, and high-end architecture | Transportation, packaging, and consumer goods |
What Are the Advantages and Disadvantages of Stainless Steel as an Alternative?
Stainless steel is renowned for its exceptional corrosion resistance and strength, making it suitable for various applications, including marine and chemical industries. Its ability to withstand extreme temperatures and harsh environments is a significant advantage. However, its higher initial cost can be a drawback for projects with tight budgets. Additionally, while stainless steel requires similar implementation tools as galvanized steel, the complexity of working with it may be higher, necessitating skilled labor.
How Does Aluminum Compare to Galvanized Steel in Terms of Usability?
Aluminum is a lightweight and versatile material that offers excellent corrosion resistance, making it ideal for non-structural applications such as packaging and transportation. Its lower initial cost can be attractive to buyers; however, aluminum may require more frequent replacements in structural applications due to lower strength compared to galvanized steel. The ease of cutting and shaping aluminum makes it user-friendly, allowing for quicker project turnaround times. Nonetheless, its susceptibility to denting can be a concern in high-impact environments.
Conclusion: How Can B2B Buyers Choose the Right Solution for Their Needs?
When selecting between galvanized steel and its alternatives, B2B buyers must consider factors such as application requirements, budget constraints, and long-term maintenance needs. Galvanized steel offers a robust solution for structural applications, while stainless steel excels in environments requiring superior corrosion resistance. Aluminum presents a cost-effective and lightweight option for less demanding uses. By evaluating these aspects against their specific project needs, buyers can make an informed decision that aligns with their operational goals and financial parameters.
Essential Technical Properties and Trade Terminology for galvanized steel manufacturer
What Are the Key Technical Properties of Galvanized Steel?
When selecting galvanized steel for industrial applications, understanding its technical properties is crucial. Here are some essential specifications to consider:
1. Material Grade
Material grade indicates the chemical composition and mechanical properties of the steel. Common grades for galvanized steel include ASTM A123 (hot-dip galvanized) and ASTM A653 (galvanized steel sheet). The grade affects the material’s strength, ductility, and corrosion resistance, directly influencing performance and durability in various applications.
2. Coating Thickness
The thickness of the zinc coating is vital for ensuring corrosion protection. It is typically measured in microns (µm) and should meet specific standards, such as ASTM A123, which prescribes minimum coating weights. A thicker coating provides better protection, especially in harsh environments, making it essential for B2B buyers in construction and manufacturing sectors to consider their specific exposure conditions.
3. Yield Strength
Yield strength is the stress at which a material begins to deform permanently. For galvanized steel, this property is critical as it defines how much load the steel can bear before yielding. Knowing the yield strength helps buyers ensure the steel will perform adequately in structural applications, reducing the risk of failure.
4. Tolerance
Tolerance refers to the permissible variation in dimensions and properties of the steel. In galvanized steel, it affects the fit and assembly of components in construction and manufacturing. Strict adherence to tolerance specifications ensures product compatibility and performance, which is vital for international buyers to avoid costly modifications.
5. Elongation
Elongation measures the material’s ability to stretch before breaking, expressed as a percentage. Higher elongation values indicate better ductility, allowing the steel to be formed or welded without cracking. This property is particularly important for manufacturers who require intricate shapes or joints in their products.
6. Corrosion Resistance
While galvanized steel is inherently resistant to corrosion due to its zinc coating, the level of resistance can vary based on the galvanizing process and environmental factors. For B2B buyers, understanding the expected lifespan of galvanized steel in specific environments helps in making informed purchasing decisions.
What Common Trade Terms Should B2B Buyers Know?
Familiarity with industry terminology is essential for effective communication and negotiation in the galvanized steel market. Here are some key terms:
1. OEM (Original Equipment Manufacturer)
OEM refers to companies that produce parts or equipment that may be marketed by another manufacturer. In the context of galvanized steel, understanding OEM relationships can help buyers identify reliable suppliers and manufacturers who adhere to quality standards.
2. MOQ (Minimum Order Quantity)
MOQ is the smallest quantity of a product that a supplier is willing to sell. This term is crucial for international buyers as it directly impacts inventory management and cost efficiency. Understanding MOQ can assist buyers in negotiating better terms and planning procurement strategies.
3. RFQ (Request for Quotation)
An RFQ is a document sent to suppliers requesting pricing and availability for specific products or services. For galvanized steel buyers, submitting an RFQ can streamline the procurement process, ensuring they receive competitive offers and detailed specifications.
4. Incoterms
Incoterms (International Commercial Terms) are a set of rules that define the responsibilities of buyers and sellers in international transactions. Understanding these terms is vital for B2B buyers to clarify shipping costs, insurance, and risk management, ensuring smooth logistics in the galvanized steel supply chain.
5. Lead Time
Lead time refers to the period between placing an order and receiving the product. This term is critical for buyers who need to plan their production schedules effectively. Knowing lead times can help in managing supply chain expectations and avoiding project delays.
6. Certification
Certification indicates that the galvanized steel meets specific industry standards and regulations. Certifications such as ISO or ASTM can provide buyers with assurance regarding quality and compliance, which is essential for maintaining industry standards and customer satisfaction.
Understanding these technical properties and trade terms will empower B2B buyers from Africa, South America, the Middle East, and Europe to make informed decisions when sourcing galvanized steel, ultimately contributing to their project’s success.
Navigating Market Dynamics and Sourcing Trends in the galvanized steel manufacturer Sector
What Are the Current Market Dynamics and Key Trends in the Galvanized Steel Manufacturing Sector?
The galvanized steel manufacturing sector is experiencing a transformative phase driven by global economic recovery, infrastructure development, and increased demand for durable materials. In regions like Africa and South America, rapid urbanization and industrialization are pushing demand for galvanized steel in construction, automotive, and energy sectors. For instance, the UAE is investing heavily in infrastructure projects, thus presenting lucrative opportunities for international B2B buyers looking to source high-quality galvanized steel products.
Emerging technologies such as artificial intelligence and the Internet of Things (IoT) are reshaping sourcing trends in this sector. Manufacturers are leveraging these technologies for better supply chain management, predictive maintenance, and real-time monitoring of production processes. Moreover, the rise of e-commerce platforms is facilitating easier access to suppliers, allowing buyers from diverse regions to compare prices and quality more effectively.
Another notable trend is the increasing focus on customization. B2B buyers are seeking suppliers that can provide tailored solutions to meet specific project requirements, enhancing the importance of strong supplier relationships. Additionally, the demand for innovative coatings and finishes in galvanized steel is on the rise, driven by aesthetic and functional needs in various applications.
How Is Sustainability Shaping the Sourcing Practices in Galvanized Steel Manufacturing?
Sustainability has become a critical consideration for B2B buyers in the galvanized steel sector. The environmental impact of steel production, particularly regarding carbon emissions and resource depletion, has led to a shift toward ethical sourcing practices. Buyers are increasingly prioritizing suppliers that demonstrate a commitment to sustainable manufacturing processes, such as utilizing recycled materials and energy-efficient technologies.
Ethical supply chains are essential for maintaining brand reputation and meeting regulatory requirements. For international buyers, especially in Europe and the Middle East, certifications such as ISO 14001 for environmental management systems and LEED (Leadership in Energy and Environmental Design) can be important indicators of a supplier’s commitment to sustainability.
In addition, the demand for ‘green’ galvanized steel products is rising. Buyers are looking for materials that not only meet their functional requirements but also contribute to their sustainability goals. This includes products that are free from hazardous substances and have lower lifecycle impacts. Collaborating with suppliers who prioritize sustainable practices can provide a competitive edge in the marketplace.
What Is the Historical Context of the Galvanized Steel Manufacturing Sector?
The galvanized steel manufacturing sector has evolved significantly over the decades. Initially developed in the 19th century, the process of galvanization was introduced to prevent corrosion in steel, thereby extending its lifespan and usability in various applications. The post-World War II economic boom led to a surge in demand for galvanized steel, particularly in construction and automotive industries.
In recent years, advancements in galvanization techniques, such as hot-dip galvanization and electro-galvanization, have further enhanced the quality and efficiency of production. These innovations have allowed manufacturers to meet the increasing demands for high-performance materials while adhering to stricter environmental regulations.
As the global landscape continues to change, the galvanized steel sector is poised for further growth, driven by technological advancements and a strong emphasis on sustainability. For international B2B buyers, understanding these historical trends is crucial for making informed sourcing decisions that align with current market dynamics.
Frequently Asked Questions (FAQs) for B2B Buyers of galvanized steel manufacturer
-
How do I ensure the quality of galvanized steel products from a manufacturer?
To ensure the quality of galvanized steel products, request certifications such as ISO 9001 or equivalent standards from the manufacturer. Conducting a factory audit can provide insight into their production processes and quality control measures. Additionally, asking for samples and third-party testing reports can help assess the durability and performance of the galvanized steel. Establishing a clear quality assurance agreement with the supplier can further safeguard your interests. -
What is the best way to evaluate a galvanized steel manufacturer for international sourcing?
When evaluating a galvanized steel manufacturer for international sourcing, consider their industry experience, production capacity, and previous client testimonials. Utilize platforms like Alibaba or Global Sources to review ratings and feedback. Additionally, check their compliance with international standards and regulations. Engaging in direct communication can also provide insights into their responsiveness and willingness to accommodate your specific needs. -
What are typical minimum order quantities (MOQs) for galvanized steel products?
Minimum order quantities (MOQs) for galvanized steel products can vary widely among manufacturers, often ranging from 1 ton to 10 tons or more. Factors influencing MOQs include the type of product, customization options, and the manufacturer’s capacity. It’s advisable to discuss your specific requirements with potential suppliers to negotiate favorable terms. If you’re unsure about quantities, consider collaborating with other buyers to meet MOQ thresholds.
-
What payment terms should I negotiate with a galvanized steel manufacturer?
Negotiating payment terms is crucial for managing cash flow and minimizing risk. Common practices include a 30% deposit upfront, with the remaining 70% due upon shipment or delivery. For larger orders, consider negotiating payment via letter of credit (LC) for added security. Always clarify terms related to payment methods, currency, and any potential financing options available through the manufacturer. -
How can I customize my galvanized steel order to meet specific project requirements?
Customization options for galvanized steel orders can include dimensions, thickness, and surface finish. Discuss your project specifications with potential suppliers and ask about their capabilities to accommodate these changes. Many manufacturers offer design assistance and can provide prototypes. Ensure that all customizations are documented in your contract to avoid misunderstandings during production. -
What logistics considerations should I be aware of when importing galvanized steel?
When importing galvanized steel, consider logistics aspects such as shipping methods, lead times, and customs clearance processes. Choose a reliable freight forwarder familiar with handling heavy materials. Evaluate the shipping terms (e.g., FOB, CIF) to understand who bears the costs and risks at each stage. Additionally, ensure compliance with local import regulations to avoid delays or additional charges. -
How do I handle quality assurance and inspections for imported galvanized steel?
To manage quality assurance for imported galvanized steel, consider hiring a third-party inspection service that can verify product specifications and compliance with standards before shipment. Specify inspection criteria in your contract with the manufacturer. It’s beneficial to have pre-shipment inspections that assess the quality, quantity, and packaging of your order to mitigate risks associated with defects or non-compliance. -
What are the common challenges faced when sourcing galvanized steel internationally?
Common challenges in sourcing galvanized steel internationally include navigating customs regulations, fluctuating shipping costs, and potential language barriers. Currency exchange rates can also impact pricing. To mitigate these issues, maintain open communication with your supplier, understand the logistics involved, and consider using a local agent who can provide on-the-ground support. Conducting thorough market research can also help you anticipate and address these challenges effectively.
Important Disclaimer & Terms of Use
⚠️ Important Disclaimer
The information provided in this guide, including content regarding manufacturers, technical specifications, and market analysis, is for informational and educational purposes only. It does not constitute professional procurement advice, financial advice, or legal advice.
While we have made every effort to ensure the accuracy and timeliness of the information, we are not responsible for any errors, omissions, or outdated information. Market conditions, company details, and technical standards are subject to change.
B2B buyers must conduct their own independent and thorough due diligence before making any purchasing decisions. This includes contacting suppliers directly, verifying certifications, requesting samples, and seeking professional consultation. The risk of relying on any information in this guide is borne solely by the reader.
Strategic Sourcing Conclusion and Outlook for galvanized steel manufacturer
In today’s competitive landscape, the importance of strategic sourcing in the galvanized steel sector cannot be overstated. By prioritizing quality, cost-efficiency, and supplier reliability, international B2B buyers—especially those from Africa, South America, the Middle East, and Europe—can significantly enhance their procurement processes. Understanding the nuances of regional market dynamics and aligning them with supplier capabilities is crucial for optimizing supply chains.
What Are the Key Takeaways for B2B Buyers in Galvanized Steel?
Investing in robust supplier relationships and leveraging technology for supply chain transparency can lead to better negotiation outcomes and risk mitigation. Additionally, staying informed about global market trends and regulatory changes will empower buyers to make proactive sourcing decisions.
How Can Buyers Prepare for Future Trends in the Galvanized Steel Market?
Looking ahead, the galvanized steel market is poised for growth, driven by infrastructure development and sustainability initiatives. Buyers are encouraged to engage with manufacturers that prioritize eco-friendly practices, as this not only meets regulatory demands but also aligns with consumer preferences.
As you navigate your sourcing strategies, consider establishing partnerships with reputable galvanized steel manufacturers that can offer innovative solutions and adaptability. Embrace the future of strategic sourcing to secure your competitive advantage in this evolving market.