Unlock Savings: Your Guide to Smart Lock Manufacturers (2025)
Introduction: Navigating the Global Market for smart lock manufacturer
Navigating the global market for smart lock manufacturers presents a unique set of challenges for international B2B buyers. With the increasing demand for security solutions across various sectors, sourcing reliable and innovative smart locks has become a critical task. This guide offers a comprehensive overview of the smart lock landscape, including the types of smart locks available, their diverse applications, and essential supplier vetting criteria. By addressing key factors such as pricing, technology integration, and regional compliance standards, we aim to empower buyers from Africa, South America, the Middle East, and Europe—specifically targeting markets like Colombia and Italy.
Understanding the intricacies of smart lock technology is vital for making informed purchasing decisions. This guide not only highlights the latest trends in smart lock features, such as biometric access and remote control functionalities, but also provides actionable insights into evaluating suppliers. Whether you are looking to enhance security for commercial properties or residential buildings, this resource is designed to help you navigate the complexities of the market confidently. Ultimately, our goal is to equip you with the knowledge and tools necessary to select the best smart lock solutions that align with your specific business needs, ensuring both safety and efficiency in your operations.
Understanding smart lock manufacturer Types and Variations
Type Name | Key Distinguishing Features | Primary B2B Applications | Brief Pros & Cons for Buyers |
---|---|---|---|
Bluetooth Smart Locks | Wireless connectivity, mobile app control | Hospitality, Offices | Pros: Easy installation, remote access. Cons: Limited range, potential connectivity issues. |
Keypad Smart Locks | Numeric or alphanumeric entry, no physical key | Residential, Commercial Spaces | Pros: No need for keys, customizable codes. Cons: Vulnerable to code sharing or guessing. |
Biometric Smart Locks | Fingerprint or facial recognition technology | High-security facilities | Pros: High security, unique access. Cons: Higher cost, potential for false rejections. |
Networked Smart Locks | Integration with IoT and cloud services | Smart buildings, Warehouses | Pros: Centralized management, data analytics. Cons: Dependency on internet connectivity. |
Smart Deadbolts | Enhanced security with smart features | Residential, Retail | Pros: Reinforced security, mobile control. Cons: May require professional installation, battery dependency. |
What Are the Characteristics of Bluetooth Smart Locks?
Bluetooth smart locks are characterized by their wireless connectivity, allowing users to control access through mobile applications. They are particularly suitable for hospitality and office environments where quick access management is essential. When purchasing Bluetooth smart locks, B2B buyers should consider the installation process, as well as potential connectivity issues that may arise in larger buildings or areas with interference.
How Do Keypad Smart Locks Benefit Businesses?
Keypad smart locks utilize a numeric or alphanumeric code for entry, eliminating the need for physical keys. This feature makes them ideal for residential and commercial spaces where multiple users need access. B2B buyers should evaluate the ease of code management and the potential risks associated with code sharing or guessing, which may compromise security.
What Are the Advantages of Biometric Smart Locks?
Biometric smart locks employ advanced technology such as fingerprint or facial recognition to grant access, making them suitable for high-security facilities. Their unique access features provide a high level of security, which is essential for sensitive areas. Buyers should weigh the higher costs and possible false rejection rates against the enhanced security benefits when considering these locks for their operations.
Why Choose Networked Smart Locks for Smart Buildings?
Networked smart locks integrate seamlessly with IoT and cloud services, providing centralized management for smart buildings and warehouses. This type of lock offers data analytics and improved access control. However, B2B buyers must consider the reliance on internet connectivity, which can be a drawback in areas with unstable networks.
What Makes Smart Deadbolts a Secure Choice?
Smart deadbolts enhance traditional locking mechanisms with smart technology, providing features such as remote control via mobile apps. They are suitable for both residential and retail environments looking for reinforced security. Buyers should consider the installation requirements and battery dependency, as these factors can impact long-term usability and maintenance.
Related Video: Tenon – Top Smart Lock Manufacturer In China
Key Industrial Applications of smart lock manufacturer
Industry/Sector | Specific Application of Smart Lock Manufacturer | Value/Benefit for the Business | Key Sourcing Considerations for this Application |
---|---|---|---|
Hospitality | Keyless entry systems for hotels and resorts | Enhances guest experience and operational efficiency | Compatibility with existing property management systems; ability to integrate with mobile apps. |
Logistics and Warehousing | Smart locks for secure storage units and warehouses | Increases security and reduces theft risk | Durability in harsh environments; remote access capabilities for logistics managers. |
Healthcare | Smart access control for medical facilities | Ensures patient safety and compliance with regulations | Compliance with health regulations; ease of use for staff. |
Education | Keyless entry for schools and universities | Improves safety and access control for students | Scalability for multiple campuses; integration with student ID systems. |
Retail | Smart locks for inventory management and showrooms | Protects high-value items and enhances customer experience | Flexibility in installation; ability to monitor access in real-time. |
How Are Smart Locks Transforming the Hospitality Sector?
In the hospitality industry, smart lock manufacturers are revolutionizing guest access through keyless entry systems. These systems allow hotel guests to use their smartphones or keycards to access their rooms, enhancing the overall guest experience. By eliminating the need for physical keys, hotels can streamline check-in processes, reduce lost key incidents, and improve security. For international buyers, it is crucial to ensure compatibility with existing property management systems and assess the potential for integration with mobile applications for seamless guest interactions.
What Benefits Do Smart Locks Offer to Logistics and Warehousing?
In logistics and warehousing, smart locks are increasingly used to secure storage units and warehouse entrances. These locks provide enhanced security by allowing authorized personnel to access sensitive areas while keeping unauthorized individuals out. The ability to monitor access remotely helps logistics managers track movements and reduce theft. Buyers in this sector should consider the durability of smart locks in harsh environments and the necessity for remote access capabilities to manage inventory effectively.
How Are Smart Locks Enhancing Security in Healthcare Facilities?
Healthcare facilities benefit significantly from smart access control systems that ensure only authorized personnel can access sensitive areas. By implementing smart locks, hospitals and clinics can enhance patient safety and comply with strict regulations regarding access to medical records and pharmaceuticals. International B2B buyers must focus on compliance with health regulations and the ease of use for staff to ensure smooth operations within the facility.
In What Ways Are Smart Locks Improving Safety in Educational Institutions?
Educational institutions are adopting smart locks for keyless entry to enhance safety and access control. By using these systems, schools and universities can restrict access to certain areas, ensuring that only students and authorized personnel can enter. This not only improves security but also fosters a safer learning environment. Buyers should look for scalable solutions that can accommodate multiple campuses and ensure integration with student ID systems for streamlined access.
How Do Smart Locks Protect Retail Inventory?
In the retail sector, smart locks are utilized to secure high-value inventory and manage access to showrooms. These locks help retailers protect their assets while enhancing customer experience by allowing easy access for employees. The ability to monitor access in real-time adds an additional layer of security. Retail buyers should prioritize flexibility in installation and the capability for real-time access monitoring to adapt to changing security needs.
Related Video: $25 DIY “Smart” Door Locks – ElectroMagnet + Sonoff + Tasmota
3 Common User Pain Points for ‘smart lock manufacturer’ & Their Solutions
Scenario 1: Security Concerns in High-Crime Areas
The Problem:
B2B buyers in regions with high crime rates, such as parts of South America and Africa, face significant challenges when it comes to ensuring the security of their facilities. Traditional locking systems may be vulnerable to tampering or forced entry, leaving businesses at risk of theft and loss of sensitive information. This situation is exacerbated by the need for quick access solutions that do not compromise security, as businesses often operate in environments where time is of the essence.
The Solution:
To address these security concerns, B2B buyers should look for smart locks equipped with advanced features such as biometrics, encryption, and remote access capabilities. When sourcing smart lock manufacturers, prioritize those that offer robust security certifications and have a proven track record in high-risk markets. For example, consider locks that feature dual authentication methods, such as a fingerprint and a PIN code, to enhance security. Additionally, evaluate solutions that allow for real-time monitoring and alerts through a centralized management system. This ensures businesses can respond swiftly to unauthorized access attempts, significantly reducing the risk of security breaches.
Scenario 2: Integration with Existing Security Systems
The Problem:
Many businesses have already invested heavily in existing security infrastructure, such as CCTV systems and alarm networks. A common pain point arises when trying to integrate new smart locking systems with these legacy systems. B2B buyers often find themselves dealing with compatibility issues that can lead to increased costs and operational disruptions.
The Solution:
To mitigate integration challenges, B2B buyers should choose smart lock manufacturers that provide comprehensive API documentation and compatibility with various security platforms. Conduct thorough research on the integration capabilities of potential suppliers. Look for manufacturers that offer modular solutions, allowing for seamless integration without the need to overhaul existing systems. Moreover, consider engaging with a supplier that provides on-site technical support and consultation services. This can facilitate a smoother transition and ensure that all components work harmoniously together, ultimately enhancing overall security.
Scenario 3: Managing Access Control for Multiple Locations
The Problem:
For businesses operating in multiple geographical locations, managing access control can be a logistical nightmare. The inability to effectively control who has access to which facilities can lead to security vulnerabilities and complicate operational processes. B2B buyers often struggle with keeping track of access permissions, especially when employees move between sites or when temporary access is needed for contractors.
The Solution:
To streamline access management, B2B buyers should opt for smart lock solutions that feature centralized access control systems. These systems allow for the management of multiple locations from a single dashboard, enabling businesses to easily grant, revoke, or modify access permissions. When selecting a smart lock manufacturer, look for options that include cloud-based management platforms, which provide flexibility and remote access capabilities. Additionally, consider solutions that offer customizable user roles and access schedules, ensuring that only authorized personnel can enter specific areas at designated times. This not only enhances security but also improves operational efficiency by simplifying access management across multiple sites.
Strategic Material Selection Guide for smart lock manufacturer
What are the Key Properties of Common Materials Used in Smart Locks?
When selecting materials for smart lock manufacturing, it is crucial to consider their properties that directly impact performance, durability, and suitability for various applications. Here, we analyze four common materials: stainless steel, zinc alloy, polycarbonate, and brass.
Stainless Steel: A Durable Choice for Smart Locks
Key Properties: Stainless steel is renowned for its high corrosion resistance and strength, making it suitable for a variety of environments. It can withstand extreme temperatures, which is essential for locks exposed to outdoor conditions.
Pros & Cons: The durability of stainless steel ensures a long lifespan, reducing the need for frequent replacements. However, it tends to be more expensive than other materials, which may affect the overall cost of the smart lock. Manufacturing complexity is moderate, requiring specialized tools for shaping and finishing.
Impact on Application: Stainless steel is compatible with most environments, including humid and coastal areas, where corrosion is a significant concern.
Considerations for International Buyers: Buyers from regions like Europe and the Middle East should ensure compliance with standards such as ASTM or DIN for corrosion resistance. The higher initial cost may be justified by the long-term savings in maintenance and replacement.
Zinc Alloy: Cost-Effective and Versatile
Key Properties: Zinc alloy offers good strength and is relatively lightweight. It has decent corrosion resistance, especially when treated with protective coatings.
Pros & Cons: The primary advantage of zinc alloy is its cost-effectiveness, making it a popular choice for budget-sensitive projects. However, it may not perform as well under extreme conditions compared to stainless steel. The manufacturing process is simpler, allowing for intricate designs.
Impact on Application: Zinc alloy is suitable for indoor applications or regions with mild climates but may not hold up well in harsher environments.
Considerations for International Buyers: Buyers from Africa and South America should evaluate the environmental conditions where the locks will be installed. Compliance with local standards for strength and durability is essential to ensure product reliability.
Polycarbonate: Lightweight and Impact-Resistant
Key Properties: Polycarbonate is a thermoplastic known for its high impact resistance and lightweight characteristics. It can withstand a wide range of temperatures, making it suitable for various applications.
Pros & Cons: The lightweight nature of polycarbonate allows for easier installation and transport. However, it may not offer the same level of security as metal materials. Additionally, it can be more susceptible to scratching and UV degradation.
Impact on Application: Polycarbonate is ideal for applications where weight is a concern, such as in portable locks or electronic access systems.
Considerations for International Buyers: Buyers in regions with high UV exposure, such as parts of Africa, should consider UV-resistant coatings to prolong the material’s life. Compliance with safety standards is also essential to ensure product reliability.
Brass: A Classic Material with Aesthetic Appeal
Key Properties: Brass is an alloy of copper and zinc, known for its excellent corrosion resistance and attractive appearance. It has good machinability and can be easily shaped.
Pros & Cons: The aesthetic appeal of brass makes it a popular choice for decorative locks. However, it is softer than other materials, which may affect its durability in high-security applications. The cost is moderate, and manufacturing processes are relatively straightforward.
Impact on Application: Brass is often used in residential settings where aesthetics are as important as functionality.
Considerations for International Buyers: Buyers from Europe may prefer brass for its traditional look, but should be aware of the need for regular maintenance to prevent tarnishing. Compliance with relevant standards for strength and corrosion resistance is also essential.
Summary Table of Material Properties for Smart Lock Manufacturing
Material | Typical Use Case for smart lock manufacturer | Key Advantage | Key Disadvantage/Limitation | Relative Cost (Low/Med/High) |
---|---|---|---|---|
Stainless Steel | High-security outdoor locks | High corrosion resistance | Higher cost | High |
Zinc Alloy | Budget-friendly indoor locks | Cost-effective and versatile | Limited performance in harsh conditions | Low |
Polycarbonate | Lightweight portable locks | Impact-resistant and lightweight | Less secure than metal materials | Medium |
Brass | Decorative residential locks | Aesthetic appeal | Softer, less durable | Medium |
This strategic material selection guide provides international B2B buyers with insights into the advantages and limitations of each material, helping them make informed decisions based on their specific needs and compliance requirements.
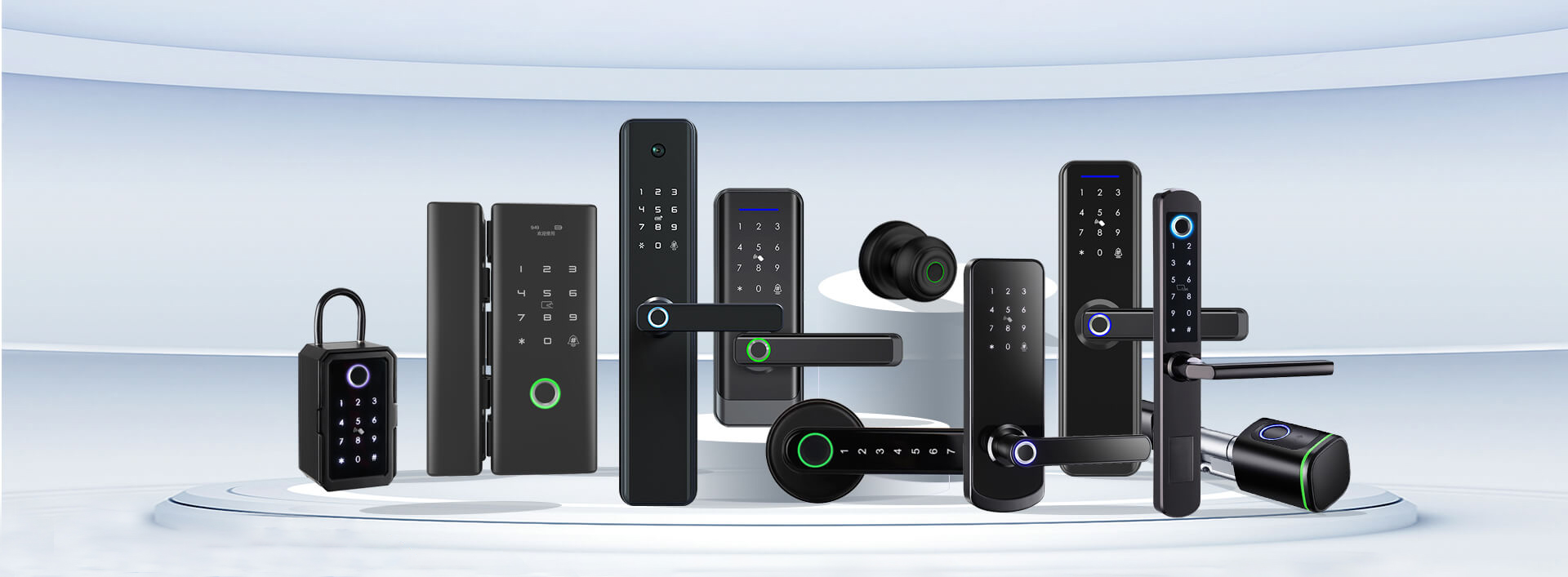
A stock image related to smart lock manufacturer.
In-depth Look: Manufacturing Processes and Quality Assurance for smart lock manufacturer
What are the Main Stages of Manufacturing Smart Locks?
The manufacturing process of smart locks involves several critical stages, each essential for ensuring the final product meets the desired quality and functionality. Here are the main stages:
Material Preparation
The first step in manufacturing smart locks is the preparation of materials. Common materials used include metals like stainless steel and aluminum, along with plastics and electronic components. Suppliers should ensure that all materials comply with international standards and specifications, which can significantly impact the durability and security of the locks. B2B buyers should request certifications for the materials used, such as ASTM (American Society for Testing and Materials) standards, to ensure quality.
Forming Techniques
Once materials are prepared, they undergo various forming processes. Techniques such as die casting, injection molding, and CNC machining are commonly employed. Die casting is particularly beneficial for creating complex metal parts with high precision. Injection molding is used for plastic components, which are integral to the smart lock’s functionality. Buyers should inquire about the specific forming techniques used by manufacturers to ensure they can produce the desired quality and design specifications.
Assembly Process
The assembly stage is where components come together to create the final product. This process often involves automated machinery, especially for electronic components, to ensure precision and efficiency. Each smart lock typically consists of several parts, including the locking mechanism, electronic circuitry, and user interface. B2B buyers should ensure that the manufacturer has robust assembly protocols in place to minimize errors and defects, which can impact the reliability of the locks.
Finishing Touches
The final stage of manufacturing involves applying finishing touches, which can include surface treatments, painting, and coating. This step not only enhances the aesthetic appeal of the smart locks but also provides additional protection against corrosion and wear. Manufacturers may use techniques like anodizing for metals or UV coating for plastics. Buyers should verify the types of finishes applied and whether they meet industry standards for durability and environmental resistance.
How is Quality Assurance Implemented in Smart Lock Manufacturing?
Quality assurance (QA) is an essential aspect of manufacturing smart locks, ensuring that the products are safe, reliable, and meet customer expectations. Here are key elements of QA in this industry:
What are the Relevant International Standards for Smart Lock Quality?
Manufacturers often adhere to international standards such as ISO 9001, which outlines criteria for a quality management system. This certification indicates that a manufacturer consistently provides products that meet customer and regulatory requirements. Additionally, certifications like CE (Conformité Européenne) and API (American Petroleum Institute) may apply depending on the market and application of the smart locks. B2B buyers should look for these certifications as a benchmark for quality assurance.
What Are the Key Quality Control Checkpoints?
Quality control (QC) checkpoints are integrated throughout the manufacturing process to identify and address issues early. Key checkpoints include:
-
Incoming Quality Control (IQC): This stage involves inspecting raw materials and components as they arrive from suppliers. Ensuring that these inputs meet specifications is critical for maintaining overall product quality.
-
In-Process Quality Control (IPQC): Throughout the manufacturing process, periodic checks are performed to ensure that each stage meets quality standards. This can include monitoring the precision of machining processes and the integrity of assemblies.
-
Final Quality Control (FQC): Before shipment, finished products undergo thorough testing to ensure they function correctly and meet all specifications. This may involve performance testing, durability assessments, and safety checks.
B2B buyers should inquire about the specific QC processes employed by manufacturers to ensure that they are comprehensive and effective.
What Common Testing Methods Are Used for Smart Locks?
Testing methods are crucial for validating the performance and reliability of smart locks. Common methods include:
-
Functional Testing: Ensuring that all electronic components, such as sensors and Wi-Fi connectivity, operate correctly under various conditions.
-
Durability Testing: Subjecting locks to extreme conditions, including temperature fluctuations and humidity, to assess their performance over time.
-
Security Testing: Evaluating the lock’s resistance to tampering and unauthorized access, which is vital for customer confidence.
-
Compliance Testing: Verifying that the smart locks meet all relevant regulatory standards.
B2B buyers should request documentation of testing results, as these provide insights into the quality and reliability of the products.
How Can B2B Buyers Verify Supplier Quality Control?
Verifying a supplier’s quality control processes is essential for B2B buyers, especially in international markets where standards may vary. Here are effective strategies:
Conducting Audits
Regular audits of suppliers can provide firsthand insights into their manufacturing and QC processes. Buyers should consider both scheduled audits and surprise inspections to ensure compliance with quality standards.
Reviewing Quality Reports
Requesting access to quality reports, including those from past audits and testing results, can help buyers assess the reliability of a supplier. These documents should detail the processes followed and any corrective actions taken.
Utilizing Third-Party Inspections
Engaging third-party inspection services can provide an impartial evaluation of a supplier’s quality control measures. These inspectors can assess compliance with international standards and provide detailed reports that inform purchasing decisions.
What Are the Quality Control Nuances for International B2B Buyers?
International B2B buyers, particularly from regions like Africa, South America, the Middle East, and Europe, should be aware of several nuances in quality control:
-
Regulatory Differences: Understanding the regulatory landscape in different regions is crucial. For instance, European buyers should be familiar with CE marking requirements, while buyers in the Middle East may need to consider local certifications.
-
Cultural Expectations: Cultural differences can affect quality perceptions. Buyers should communicate clearly with suppliers about their quality expectations and standards.
-
Logistical Challenges: Cross-border logistics can impact the quality of materials and finished products. Buyers should establish clear agreements regarding shipping, handling, and quality checks at various points in the supply chain.
By understanding these nuances, B2B buyers can better navigate the complexities of international procurement and ensure they partner with reliable smart lock manufacturers.
Practical Sourcing Guide: A Step-by-Step Checklist for ‘smart lock manufacturer’
To effectively procure smart locks from manufacturers, B2B buyers must follow a structured approach that ensures quality, reliability, and suitability for their specific needs. This checklist serves as a practical guide to streamline the sourcing process.
Step 1: Define Your Technical Specifications
Before reaching out to suppliers, it’s essential to outline the technical requirements of the smart locks you intend to purchase. Consider aspects such as compatibility with existing security systems, connectivity options (e.g., Wi-Fi, Bluetooth), and specific features like biometric access or remote management. Having clear specifications helps in identifying manufacturers that can meet your needs.
Step 2: Research Potential Suppliers
Conduct thorough research to compile a list of potential smart lock manufacturers. Utilize online marketplaces, industry directories, and trade shows to gather options. Look for manufacturers with a solid reputation and experience in the smart lock industry. Pay attention to their product offerings, market presence, and customer reviews to gauge their reliability.
Step 3: Evaluate Supplier Certifications
✅ Verify Supplier Certifications
It’s crucial to ensure that your chosen suppliers hold relevant certifications such as ISO 9001 for quality management systems or specific certifications for electronic security products. This verification is important as it reflects the manufacturer’s commitment to quality and compliance with industry standards. Check if they also comply with local regulations in your region.
Step 4: Request Product Samples
Once you have shortlisted potential suppliers, request samples of their smart locks. Testing these samples will provide insight into the product quality, functionality, and ease of use. During this phase, assess not only the locks themselves but also the accompanying software or apps that may be integral to their operation.
Step 5: Assess Pricing and Payment Terms
💰 Compare Pricing and Payment Options
Gather detailed quotations from multiple suppliers to compare pricing structures. Be cautious of prices that seem too good to be true, as they may indicate inferior quality. Additionally, understand the payment terms, including deposit requirements and credit options, to avoid financial strain during procurement.
Step 6: Conduct Background Checks
Before finalizing your decision, conduct background checks on the suppliers. This may include checking their financial stability, history of legal disputes, and overall market reputation. Engaging with other businesses in your industry can provide valuable insights into the supplier’s performance and reliability.
Step 7: Establish Clear Communication Channels
📞 Set Up Communication Protocols
Effective communication is key to a successful sourcing relationship. Establish clear communication channels and protocols to ensure that all parties are aligned throughout the procurement process. Discuss timelines, responsibilities, and any potential challenges openly to foster a collaborative environment.
By following this checklist, international B2B buyers can confidently navigate the procurement process for smart locks, ensuring they select the most suitable manufacturer for their specific needs.
Comprehensive Cost and Pricing Analysis for smart lock manufacturer Sourcing
What Are the Key Cost Components in Smart Lock Manufacturing?
When sourcing smart locks, understanding the cost structure is vital for effective budgeting and negotiation. The primary cost components include:
-
Materials: This includes the raw materials used in the production of smart locks, such as metals, plastics, and electronic components. The choice of materials can significantly impact the overall cost and durability of the product.
-
Labor: Labor costs encompass wages paid to workers involved in the manufacturing process. In regions like Africa and South America, labor costs may be lower, potentially providing a competitive advantage.
-
Manufacturing Overhead: This covers indirect costs associated with production, such as utilities, rent, and equipment depreciation. Efficient management of overhead can improve profit margins.
-
Tooling: The cost of molds, dies, and other tools required for manufacturing can be substantial. Custom tooling may be necessary for unique designs, influencing initial costs.
-
Quality Control (QC): Investing in quality assurance processes is essential to ensure product reliability. This includes inspections and testing, which can add to the overall cost but are critical for maintaining standards.
-
Logistics: Transportation and warehousing expenses must be factored in, especially for international shipments. Choosing the right logistics partner can help manage these costs effectively.
-
Margin: Manufacturers typically include a profit margin in their pricing. Understanding industry standards for margins can help buyers gauge fair pricing.
How Do Pricing Influencers Affect Smart Lock Costs?
Several factors can influence the pricing of smart locks:
-
Volume and Minimum Order Quantity (MOQ): Purchasing in bulk usually leads to lower per-unit costs. Buyers should negotiate MOQs that align with their inventory needs to optimize cost savings.
-
Specifications and Customization: Tailored products often incur additional costs. It’s crucial for buyers to communicate their specific needs clearly to avoid unexpected charges.
-
Materials Quality and Certifications: Higher-quality materials and certifications (e.g., ISO standards) can increase costs but may offer long-term benefits in terms of durability and marketability.
-
Supplier Factors: Supplier reliability and reputation can affect pricing. Established suppliers might charge a premium for their proven track record, while new entrants may offer lower prices to attract business.
-
Incoterms: The terms of delivery can significantly impact costs. Understanding Incoterms can help buyers anticipate additional charges related to shipping, insurance, and customs clearance.
What Are the Best Negotiation Strategies for International B2B Buyers?
Effective negotiation is key to achieving favorable pricing:
-
Research and Benchmarking: Buyers should conduct market research to understand average pricing and competitor offerings, allowing them to negotiate from a position of knowledge.
-
Leverage Total Cost of Ownership (TCO): Highlighting the long-term savings associated with higher-quality locks can justify a higher upfront cost and lead to better negotiations.
-
Be Transparent About Budget Constraints: Communicating budget limits can encourage suppliers to offer more competitive pricing or flexible payment terms.
-
Establish Relationships: Building long-term partnerships with suppliers can lead to better pricing and preferential treatment over time.
-
Utilize Local Insights: For buyers from Africa, South America, the Middle East, and Europe, leveraging local market knowledge can provide advantages in negotiations, such as understanding cultural nuances that may affect pricing discussions.
Are There Pricing Nuances for International Buyers?
International buyers should be aware of specific pricing nuances:
-
Currency Fluctuations: Changes in exchange rates can impact the total cost. It is wise to negotiate prices in a stable currency or include clauses that account for significant fluctuations.
-
Tariffs and Duties: Import tariffs can substantially increase costs. Buyers should research applicable tariffs in their country to factor these into their budgeting.
-
Cultural Considerations: Different regions may have varying expectations regarding pricing negotiations. Being attuned to these cultural nuances can facilitate smoother discussions.
Conclusion
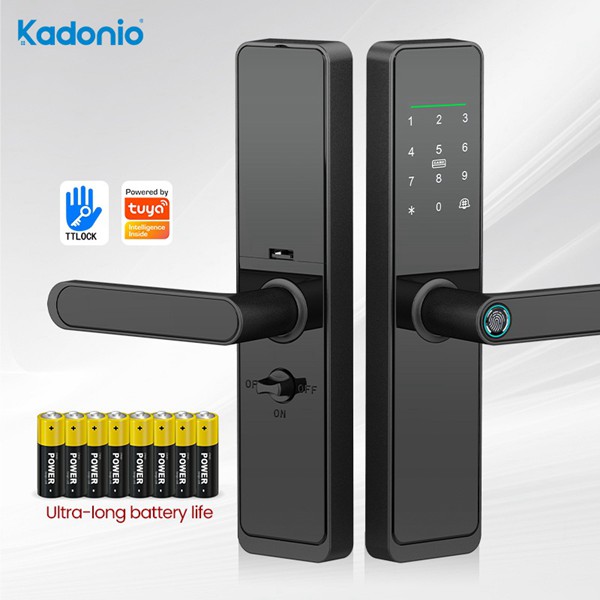
A stock image related to smart lock manufacturer.
Understanding the comprehensive cost structure and pricing dynamics in smart lock manufacturing is crucial for international B2B buyers. By analyzing cost components, recognizing pricing influencers, and employing effective negotiation strategies, buyers can make informed decisions that align with their business goals.
Alternatives Analysis: Comparing smart lock manufacturer With Other Solutions
Understanding Alternatives in Smart Lock Solutions
When considering smart lock solutions, it’s essential to explore various alternatives that meet security and access needs. While smart locks from reputable manufacturers offer advanced features, there are other technologies and methods that can fulfill similar objectives. This analysis compares smart lock manufacturers with traditional mechanical locks and biometric access systems, providing a comprehensive view for international B2B buyers.
Comparison Table of Smart Lock Solutions
Comparison Aspect | Smart Lock Manufacturer | Traditional Mechanical Locks | Biometric Access Systems |
---|---|---|---|
Performance | High; includes remote access & monitoring | Moderate; requires physical keys | Very high; instant access control |
Cost | Medium to High; initial investment in tech | Low to Medium; affordable options | High; advanced technology costs |
Ease of Implementation | Moderate; requires installation & setup | Easy; typically DIY installation | Complex; may require professional installation |
Maintenance | Low; software updates needed | Low; periodic key replacements | Moderate; hardware checks needed |
Best Use Case | Ideal for businesses needing remote access | Suitable for low-security environments | Best for high-security areas needing strict access control |
In-Depth Analysis of Alternatives
What are the Advantages and Disadvantages of Traditional Mechanical Locks?
Traditional mechanical locks have been the standard for securing doors for decades. They are cost-effective and straightforward to install, making them an attractive option for many businesses, especially those operating on a tight budget. However, they come with significant drawbacks, including the risk of lock picking, the inconvenience of physical keys, and the potential for key loss or duplication. Businesses with low security needs may find them sufficient, but they lack the advanced features of smart locks.
How do Biometric Access Systems Compare?
Biometric access systems utilize unique biological traits, such as fingerprints or facial recognition, to grant access. This technology offers high security and convenience, as users do not need to remember keys or codes. However, the initial setup and costs can be prohibitive for some businesses, particularly those in developing regions. Additionally, these systems may require ongoing maintenance and updates to ensure accuracy and security. They are best suited for high-security environments, such as financial institutions or data centers.
Conclusion: How to Choose the Right Solution for Your Needs
When selecting the appropriate locking solution, B2B buyers should assess their specific requirements, including the level of security needed, budget constraints, and ease of implementation. Smart locks provide advanced features and flexibility for businesses requiring remote access and monitoring. In contrast, traditional mechanical locks may suffice for lower-security settings, while biometric systems are ideal for environments demanding stringent access controls. Ultimately, understanding the trade-offs between these options will empower buyers to make informed decisions that align with their organizational needs and security objectives.
Essential Technical Properties and Trade Terminology for smart lock manufacturer
What Are the Essential Technical Properties of Smart Locks?
Understanding the technical properties of smart locks is crucial for B2B buyers, especially in markets such as Africa, South America, the Middle East, and Europe. Here are some key specifications to consider:
1. Material Grade: What Should You Look For in Smart Locks?
Smart locks are typically made from materials like stainless steel, aluminum, or high-impact plastics. The material grade affects the durability, corrosion resistance, and overall security of the lock. For instance, a higher-grade stainless steel lock will offer better resistance to wear and tear, making it ideal for high-traffic areas. This is particularly important for commercial applications where security and longevity are paramount.
2. Tolerance Levels: Why Are They Important?
Tolerance levels refer to the permissible limits of variation in the lock’s dimensions. High-precision tolerances ensure that components fit together perfectly, which is critical for the lock’s functionality and security. Inaccurate tolerances can lead to operational failures or vulnerabilities, making this specification a key consideration for B2B buyers who prioritize reliability.
3. Power Source: What Options Are Available?
Smart locks can operate on battery power, hardwired connections, or even solar power. Understanding the power source is essential for evaluating the lock’s usability and maintenance needs. Battery-operated locks, for example, may require regular battery replacements, while hardwired options might involve more complex installation processes. Buyers should assess their specific application needs when choosing a power source.
4. Connectivity Options: How Do They Impact Functionality?
Smart locks often come with various connectivity options such as Wi-Fi, Bluetooth, or Zigbee. These options determine how the lock interacts with other devices, such as smartphones or home automation systems. A lock with multiple connectivity options can offer greater flexibility and integration into existing security systems, which is a significant advantage for B2B buyers looking for comprehensive solutions.
5. Security Certifications: What Should You Verify?
Security certifications, such as ANSI/BHMA grades, indicate the level of security a smart lock offers. These certifications are essential for B2B buyers, as they provide assurance about the lock’s performance under various conditions. A lock with a higher grade typically offers better resistance to forced entry and tampering, which is crucial for commercial applications.
What Are Common Trade Terms Related to Smart Lock Manufacturing?
Familiarity with industry jargon is essential for effective communication and negotiation in B2B transactions. Here are some common trade terms relevant to smart lock manufacturing:
1. OEM (Original Equipment Manufacturer): What Does It Mean?
An OEM refers to a company that produces parts or equipment that may be marketed by another manufacturer. In the context of smart locks, buyers may work with OEMs to produce custom locks that meet specific requirements. Understanding OEM relationships can help buyers ensure they receive high-quality products tailored to their needs.
2. MOQ (Minimum Order Quantity): Why Is It Important?
MOQ is the smallest number of units a supplier is willing to sell in a single order. Knowing the MOQ is crucial for B2B buyers as it affects inventory management and cost efficiency. Buyers should negotiate MOQs that align with their purchasing capabilities to avoid overstocking or stockouts.
3. RFQ (Request for Quotation): How to Use It Effectively?
An RFQ is a document sent to suppliers to request pricing and other information for specific products. B2B buyers should use RFQs to compare prices, specifications, and terms from multiple suppliers, ensuring they make informed purchasing decisions.
4. Incoterms (International Commercial Terms): What Do They Cover?
Incoterms are a set of international rules that define the responsibilities of buyers and sellers in the shipping process. Understanding Incoterms helps B2B buyers clarify shipping costs, risks, and responsibilities, which can significantly impact the overall cost and logistics of acquiring smart locks.
By grasping these technical properties and trade terms, B2B buyers can make informed decisions when sourcing smart locks, ensuring they meet their operational and security needs effectively.
Navigating Market Dynamics and Sourcing Trends in the smart lock manufacturer Sector
What Are the Current Market Dynamics and Key Trends in the Smart Lock Manufacturer Sector?
The smart lock manufacturing sector is experiencing rapid growth driven by technological advancements and an increasing demand for enhanced security solutions. Key market drivers include the surge in smart home technology adoption, the need for improved access control in commercial properties, and the rising concerns regarding safety and security. International B2B buyers, particularly from regions like Africa, South America, the Middle East, and Europe, should pay attention to emerging trends such as the integration of IoT technology, which allows for remote monitoring and control of locks via mobile applications.
Moreover, the emphasis on cybersecurity in smart lock systems is crucial. As manufacturers innovate, they are focusing on creating products that not only offer physical security but also incorporate advanced encryption and authentication protocols. This trend is particularly relevant for B2B buyers in sectors like hospitality and property management, where robust security measures are paramount.
Additionally, sustainability is becoming a significant factor in purchasing decisions. Companies are increasingly looking for suppliers that utilize environmentally friendly materials and manufacturing processes. B2B buyers should prioritize partnerships with manufacturers that demonstrate commitment to sustainable practices, as this can influence brand reputation and consumer trust.
How Important Is Sustainability and Ethical Sourcing in the Smart Lock Manufacturing Industry?
Sustainability and ethical sourcing are critical considerations for B2B buyers in the smart lock manufacturing sector. The environmental impact of manufacturing processes and materials is under scrutiny, pushing manufacturers to adopt greener practices. This includes utilizing recycled materials, reducing waste, and implementing energy-efficient production methods.
For buyers, prioritizing suppliers with certifications such as ISO 14001 (Environmental Management) or those that comply with the EU’s Eco-Design Directive can ensure that they are sourcing from environmentally responsible manufacturers. Additionally, ethical sourcing practices, including fair labor conditions and transparent supply chains, are increasingly important to end consumers. Buyers can enhance their brand image and market positioning by aligning with suppliers who uphold these values.
Investing in ‘green’ certifications and materials not only meets regulatory requirements but also appeals to a growing segment of environmentally conscious consumers. By focusing on sustainable sourcing, B2B buyers can mitigate risks and enhance their competitive advantage in the marketplace.
How Has the Smart Lock Manufacturing Sector Evolved Over Time?
The evolution of the smart lock manufacturing sector can be traced back to the integration of electronic and digital technologies into traditional locking mechanisms. Initially, these products were primarily mechanical, but advancements in technology have paved the way for smart locks that offer features such as keyless entry, biometric access, and remote control capabilities.
The historical shift from mechanical to electronic locks began in the late 20th century, with the advent of RFID technology. Over the past two decades, the rise of the Internet of Things (IoT) has transformed the landscape, allowing locks to connect to home automation systems and mobile devices. This evolution has not only improved convenience and accessibility but has also significantly enhanced security measures, as manufacturers continue to innovate with features designed to thwart unauthorized access.
For international B2B buyers, understanding this evolution is crucial, as it informs purchasing decisions and highlights the importance of selecting suppliers that are at the forefront of technological advancements. As the market continues to evolve, staying informed on trends and innovations will be key to making strategic sourcing decisions.
Frequently Asked Questions (FAQs) for B2B Buyers of smart lock manufacturer
-
How do I choose the right smart lock manufacturer for my business needs?
Choosing the right smart lock manufacturer involves assessing several key factors. Start by evaluating the manufacturer’s reputation and track record in the industry. Look for certifications and compliance with international standards, which can indicate quality assurance. Additionally, consider their product range and whether they offer customization options that align with your specific requirements. It’s also beneficial to review client testimonials and case studies to gauge their capability in delivering reliable solutions. -
What are the key features to look for in a smart lock?
When selecting a smart lock, prioritize features such as security protocols (e.g., AES encryption), ease of installation, and user-friendly access methods (like mobile app controls or biometric recognition). Check for compatibility with existing security systems and integration with smart home technologies. Moreover, consider the lock’s durability and weather resistance, especially if it will be used in outdoor settings or harsh environments. -
What minimum order quantities (MOQ) should I expect from smart lock manufacturers?
Minimum order quantities (MOQ) can vary significantly between manufacturers, typically ranging from 50 to several hundred units. It’s crucial to discuss MOQs upfront during negotiations, as many manufacturers are willing to be flexible, especially for new clients or bulk orders. For smaller businesses, some manufacturers may offer lower MOQs for initial trial orders, allowing you to assess product quality before committing to larger purchases. -
How can I ensure the quality of smart locks before purchasing?
To ensure quality, request samples from potential manufacturers to evaluate the product firsthand. Additionally, inquire about their quality assurance processes, including testing procedures for durability and security. Look for certifications such as ISO 9001, which indicates adherence to quality management standards. Engaging third-party inspection services before shipment can also provide an added layer of assurance regarding the product’s quality. -
What payment terms are typically offered by smart lock manufacturers?
Payment terms can vary, but many manufacturers offer options such as upfront payment, partial payments, or net 30/60/90 terms. For international transactions, consider using secure payment methods like letters of credit or escrow services to protect your investment. It’s advisable to clarify all payment details, including currency exchange rates and potential fees, before finalizing any agreements to avoid misunderstandings. -
How do I navigate international shipping and logistics for smart locks?
Navigating international shipping requires understanding the logistics involved in transporting goods across borders. Collaborate with a reliable freight forwarder who can assist with customs clearance, tariffs, and local regulations. Discuss shipping options with your manufacturer to identify the best methods that balance cost and delivery time. Always consider the logistics of returns and warranty services, particularly when dealing with international suppliers. -
What customization options are available for smart locks?
Many smart lock manufacturers offer customization options to meet specific business needs. This may include branding (such as logo printing), color choices, and tailored features like specific access controls or integrations with existing security systems. During initial discussions, clearly communicate your requirements and ask for examples of previous custom projects to gauge the manufacturer’s capability in delivering bespoke solutions. -
How can I verify the reliability of a smart lock supplier?
To verify a smart lock supplier’s reliability, conduct thorough research, including checking their business licenses and certifications. Request references from current clients and review their feedback on product quality and customer service. Additionally, consider visiting their production facilities if possible, or engage in a video call to assess their operations. Utilizing platforms like Alibaba or Global Sources can also provide insights into their reputation through buyer reviews and ratings.
Important Disclaimer & Terms of Use
⚠️ Important Disclaimer
The information provided in this guide, including content regarding manufacturers, technical specifications, and market analysis, is for informational and educational purposes only. It does not constitute professional procurement advice, financial advice, or legal advice.
While we have made every effort to ensure the accuracy and timeliness of the information, we are not responsible for any errors, omissions, or outdated information. Market conditions, company details, and technical standards are subject to change.
B2B buyers must conduct their own independent and thorough due diligence before making any purchasing decisions. This includes contacting suppliers directly, verifying certifications, requesting samples, and seeking professional consultation. The risk of relying on any information in this guide is borne solely by the reader.
Strategic Sourcing Conclusion and Outlook for smart lock manufacturer
In navigating the evolving landscape of smart lock manufacturing, international B2B buyers must prioritize strategic sourcing to harness value and innovation. A comprehensive understanding of market trends, supplier capabilities, and technological advancements is crucial for making informed procurement decisions. By focusing on strategic partnerships with manufacturers that emphasize quality, security, and sustainability, businesses can enhance their competitive edge.
What Are the Key Benefits of Strategic Sourcing for Smart Locks?
Strategic sourcing not only mitigates risks associated with supply chain disruptions but also fosters collaboration that can lead to customized solutions tailored to specific market needs. For buyers in regions such as Africa, South America, the Middle East, and Europe, aligning with manufacturers who understand local compliance and consumer preferences can significantly enhance market penetration.
How Can International Buyers Prepare for Future Trends in Smart Lock Technology?
Looking ahead, the integration of IoT, AI, and biometric technologies within smart locks presents exciting opportunities. Buyers are encouraged to stay informed about technological innovations and evolving consumer demands to make proactive sourcing decisions. Embracing these advancements will not only improve security measures but also streamline operations across various sectors.
In conclusion, as the smart lock industry continues to evolve, international B2B buyers should leverage strategic sourcing to ensure they are well-positioned to adapt and thrive. Engage with manufacturers who are committed to innovation and quality to secure a competitive advantage in this dynamic market.